- コラム
早く帰れる生産管理 〜日々の業務負担を減らすためにできること〜
目次
普段、私たちがご支援する生産管理の皆様からは、その業務の多忙さについてよくお話を伺います。その要因は、様々な部署との板挟みになりやすいことや、外部環境の変化に常に影響を受けることなどが挙げられます。その結果、突発的な事態に振り回され、残業続きの日々を送っている方も少なくありません。
本日は、そのような状況下で業務に取り組む生産管理の皆様が、いかに業務負担を軽減し、本来の生産管理業務に集中できるかについて、具体的な取り組みをご紹介いたします。
生産管理の理想と現実
生産管理は、製造業において非常に重要な役割を担っています。お客様からの注文受付、納期調整、製造現場への指示、購買部門との連携、物流部門との調整など、各部門のハブとして機能しています。
しかし、実際には多くの悩みや課題を抱えている現状があります。
「納期前倒しの依頼にどう対応すれば良いか」
「残業を減らすためにどこを調整すれば良いか」
「進捗の遅れの原因が特定できない」
「納期遅延のリスクがあるが、どう調整すべきか」
「計画変更が多く、現場が混乱している」
このような日々の業務に追われることで、生産管理の方々には大きな負担がかかっています。結果として、負のスパイラルに陥ってしまい、「毎回調整に追われないようにしたい」と思いながらも、目の前のトラブルに対処せざるを得ない状況が続いています。
根本的な原因とは?
生産管理の現場における課題の根本的な原因として、以下の3つが挙げられます。
ブラックボックス化
状況の可視化ができていないため、問題が発生しても原因究明に時間がかかってしまう状態です。
事例1: 工場の残業時間が増加した原因が特定できない
「先月の工場の残業時間、なぜこんなに多かったのか?」と後になって気づくも、原因が特定できないケースがあります。各工程の進捗状況やトラブル発生状況が可視化されておらず、担当者間の情報共有が不足しているため、原因を突き止めるのに関係部署に何度も問い合わせをしなければならない、といった問題です。
事例2: 部材の在庫不足の原因が特定できない
「今月、部材の在庫が予想以上に少ない。なぜだろう?」といった事例では、過去の発注記録や在庫データが整理されておらず、原因調査に膨大な時間がかかることがあります。結果として発注ミスだったことが判明するものの、対応が遅れて生産に支障が出てしまう、といったケースです。
属人化
業務が特定の担当者に集中し、特定の担当者しか業務内容を理解しておらず、担当者が不在になるとチーム全体が対応できず、業務が滞ってしまう状態です。
基本的な方法が引き継がれていても、イレギュラーな事象への対応が引き継がれていない場合など、部分的な属人化が残ってしまい、問題が発生するケースは少なくありません。
事例1: 計画作成が特定の担当者に依存
ベテラン社員が長年の経験と勘に基づいて計画を作成していたものの、退職後には誰も計画を作れず、納期遅延の危機に陥ってしまった。
事例2: トラブル対応が特定の担当者に依存
製造現場で機械トラブルが発生した際、いつも対応していた担当者が不在だったため、他の方が対応方法を把握しておらず、復旧に時間がかかり、計画の見直しが必要になってしまった。
マニュアル不在
標準化された手順書や業務フローがないため、担当者によって業務の進め方が異なり、ミスやトラブルの原因となってしまう状態です。
事例1: 新規受注時の納期回答にばらつき
営業担当から「新規受注時の納期回答をしてほしい」と依頼された際に、「誰が、どのタイミングで、どんな情報を基に回答するか」が明確になっていなかったため、ダブルブッキングが発生し、お客様とのトラブルに発展してしまった。
事例2: 急な仕様変更時の対応が担当者によって異なる
お客様から急な仕様変更の依頼があった際、担当者によって情報の伝達方法や対応が異なっていたため、製造現場に正確な情報が伝わらず、手戻りが発生。結果として納期遅延やコスト増加につながった。
課題解決への着手のポイント
これらの課題に対して、「何を改善するのか」という観点と「どの範囲で取り組むのか」という2つの視点から、着手のポイントを見ていきましょう。
何に着手するのか
- ルールを決めて合意する
- 業務の可視化を始める
- 業務の手順を明確にする
どの範囲で着手するのか
- 生産管理部門内のみで取り組む
- 生産管理と調達・購買部門が連携して取り組む
- 営業部門も巻き込んで取り組む
関与する組織が多くなれば成果も大きくなりますが、その分だけ難易度も上がります。まずは、自部門で完結する取り組みから始めるのがおすすめです。
具体的な事例紹介
事例1:ルールを決めて合意する
状況:短納期回答が担当者にとって変動する
営業部と生産管理部で納期に対する認識のずれが生じ、双方に負担がかかっていました。営業部は顧客ニーズに応えるべく短納期回答を優先するが、生産管理部は在庫リスクを減らすため、ある程度の余白を確保して計画生産を重視していました。
取り組み例:標準納期と特急対応のルールを明確化し、受注前後の情報共有を徹底
- 標準納期と特急対応のルールを明確化する
製品の種類やお客様のセグメントごとに標準納期を設定。特急対応については、上長の承認が必要など、例外扱いのルールを設定しました。すべてを厳格に決めるのではなく、標準ルールを定めることで、「基本」と「例外」を明確化するアプローチです。 - 受注前後の情報共有を徹底する
営業部が顧客の要望や商談状況を生産管理部と事前に共有。生産管理部が在庫状況や生産能力を踏まえて、納期回答の可否や条件を営業部に伝えるよう変更しました。
結果:スムーズな納期回答と計画変更の減少
営業部と生産管理部がお互いの制約を理解し、協力体制を構築することができました。
事例2:業務の可視化を始める
状況:残業時間過多の原因が特定できない
月末に工場の残業時間が大幅に増加していたが、原因が特定できません。担当者ごとに情報が散在しており、全体像を把握するのが難しい状況でした。
取り組み例:工程管理表を作成し、ボトルネックを特定
各工程の進捗状況、作業時間、トラブル発生状況を把握するための工程管理表を作成。可視化により、特定の工程に作業が集中してボトルネックが発生していることを特定しました。ボトルネックとなる工程を分析し、作業の標準化や平準化を実施しました。
結果:工程改善が進み、残業時間を削減
問題点が明確化されたことで、工程改善を進められるようになりました。また、計画的な残業管理が可能になりました。可視化の取り組みを通じて、問題の原因を早期に特定し、適切な解決策を打てるようになることがポイントです。
事例3:業務の手順を明確にする
状況:納期回答にばらつきがあり、二重受注や納期遅延が発生
営業担当からの依頼に対し、担当者や時期によって回答内容にばらつきがあり、お客様からの信頼を失いかねない状況でした。
取り組み例:業務フロー図とチェックリストを作成し、手順を標準化
誰がどのタイミングで、どんな情報を確認し、誰に承認を得て回答するのかをフロー図で明確に。フロー図に基づき、各ステップで確認すべき項目をリスト化しました。
例:必要な在庫量の確認、納期の優先順位、特殊な仕様変更の有無など。
結果:業務内容を標準化し、顧客からの信頼が向上
納期回答の手順を標準化し、チェックリストを導入したことで確認漏れが減少。業務手順を明確化することで、日常業務で発生するばらつきを防ぎ、安定した対応を可能にすることが重要です。
改善着手に向けたヒント
限られた時間で改善を進めるためには、以下の3つの視点が重要です。
上司や関係部署を巻き込む
現在の状況が持つリスクを正しく伝え、問題の深刻さを上司や関係部署に理解してもらうことが重要です。これにより、次のような効果が得られます。
- 業務改善のための時間を確保する合意が得られる
- 他部署との連携が必要な場合の協力を得やすくなる
上司は日々多くの情報に触れているため、特定のテーマのリスクや重要性を十分に理解していないことがあります。そのため、問題を解決しない場合の影響やリスクを明確に説明し、共通の認識を持つことが大切です。
チーム内で協力体制を作る
生産管理部門内で、業務状況や問題点を共有し、チーム全体で協力体制を構築します。
これにより、以下のような進め方が可能になります。
- 問題意識を部門内で共有することで、解決の方向性が一致する
- 業務改善を分担して進めやすくなる
業務改善には個人で進められる限界があります。チーム内で「ここが問題だ」「こう解決する必要がある」という共通認識を持つだけでも、取り組みやすい環境を作ることができます。
外部の力や新しいツールを活用する
自部門内だけで改善が難しい場合は、外部リソースを活用することも効果的です。
- セミナーや勉強会への参加:他社の事例やノウハウを吸収し、効率的に知識を得る
- 専門コンサルタントの活用:課題を客観的に分析し、最適な改善策を提案してもらう
- システムやツールの導入:業務効率化を支援するツールを活用し、手作業を減らす
他社事例や外部の専門知識を取り入れることで、改善の手戻りを防ぎ、スムーズに進めることが可能です。限られたリソースを補完する手段として、外部の力を積極的に検討することが推奨されます。
改善の入口として「生産計画」が有効
これらの視点を踏まえ、業務改善の最初の一歩として適しているのが、「生産計画」の領域です。
なぜ生産計画が入口に適しているのか?
生産計画は、生産管理業務全体の情報の起点となる場面が多く、営業部とのコミュニケーションや、現場への製造指示など、多岐にわたる業務の基盤となります。一方で、生産管理の部門内で比較的取り組みやすい範囲に収まることが多い業務です。
したがって、生産管理部門が業務改善に取り組む際の最初の一歩として、生産計画は非常に適したテーマであると言えます。
具体的な活用例:スザキ工業所様
生産計画を起点とした改善活動を実施し、大きな成果を上げた事例があります。次に、その具体的な事例についてご紹介いたします。
背景と課題
スザキ工業所様(岐阜県)は、自動車や農機具部品の製造・溶接を行う企業です。取引先の拡大に伴い、受注形式が多様化し、取り扱い製品数が増加するという状況に直面されました。その結果、以下のような課題が生じていました。
- 紙ベースでの計画作成による、計画粒度の荒さ
- 計画通りに製造が進まない
- 計画立案者への負荷が増大し、対応が難しくなる
解決への取り組み
これらの課題に対し、「生産計画のシステム化」が改善の起点になると判断され、社長を含む中心メンバーがリードして取り組みを開始しました。
はじめは、情報が揃わない中でも、目安となる計画を立て、実績に基づいて見直しを行うというサイクルを何度も繰り返す形で改善を進めました。
成果
この取り組みにより、生産計画が次第に機能し、以下のような成果を達成されました。生産計画を基点にして、顧客対応から製造現場の効率化まで幅広い改善が実現した事例となっています。
- 生産結果の可視化:タイムリーな納期回答が可能に
- 日々の活動内容の見直し:計画を基軸とした改善活動の推進
- 不良品率の低下
- 残業の常態化の改善
活用されたツール「最適ワークス」
スザキ工業所様が導入されたのが、スカイディスクが提供する「最適ワークス」という生産計画システムです。このツールは、AIを活用して生産計画を自動立案する機能を備えています。
特徴とメリット
- 計画立案の自動化:マスターデータやオーダーデータを登録後、「計画を作る」ボタンを押すだけで、ガントチャート形式で計画を作成。
- クラウド型サービス:導入のハードルが低く、初期投資が少ない。
- サポート体制:導入後も、弊社のカスタマーサクセスチームが継続的にサポート。
成果が出やすい理由
使いやすさに加え、運用までをサポートする体制が整っているため、企業の改善活動がスムーズに進みます。
他社事例や運用ノウハウを活用することで、短期間で効果を実感しやすいことも理由のひとつです。
さいごに
本日の内容を踏まえて、「自社の状況に当てはまりそう」「詳しく話を聞きたい」と思われた場合は、ぜひお気軽にご相談ください。どのような取り組みができるか、一緒に検討できればと思います。ご清聴ありがとうございました。
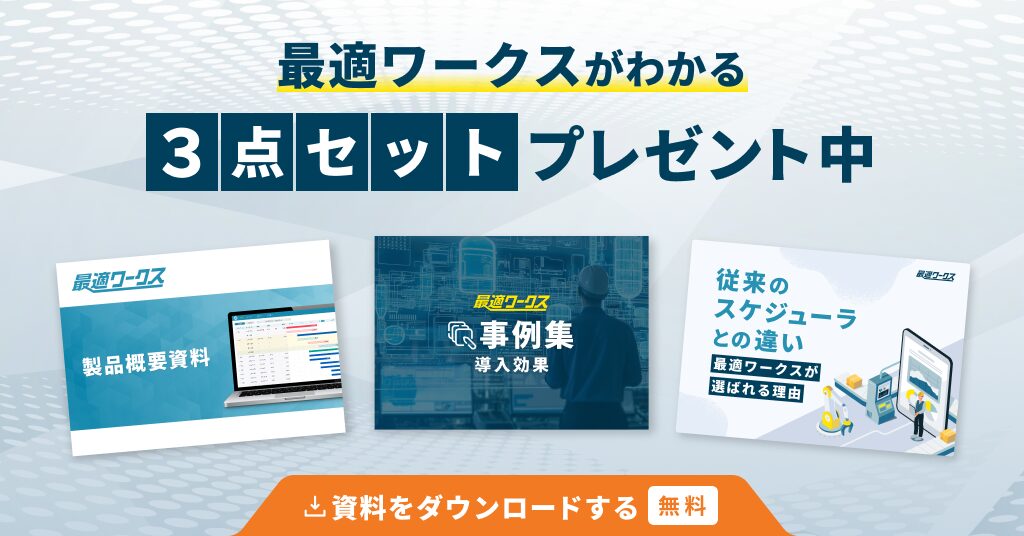