- コラム
生産スケジューラとは?製造業が知っておくべき基礎知識とメリットを解説
多品種少量生産が当たり前となった製造現場では、突発的な仕様変更に対応しきれず「在庫のムダ」「納期遅れ」に頭を抱える方も多いでしょう。そんな悩みを解決する糸口として注目されているのが、生産管理スケジューラです。本記事では導入メリットや具体的な活用法を解説し、属人的な計画づくりから脱却するヒントを提供します。作業負荷の見える化や在庫最適化などの成果を実現するためのポイントをわかりやすく紹介します。スケジューラを使いこなせば、予測精度の向上や部門間の連携強化など、多くのメリットを享受できるはずです。
生産スケジューラとは
生産スケジューラの定義
生産スケジューラとは、製造業における生産計画の立案や進捗管理を高度かつ効率的に行うためのシステムです。具体的には、以下のような機能を持ちます。
- いつ(タイミング)
- どこで(設備・ライン)
- どの順番で(優先順位・作業手順)
これらを最適化することで、納期遵守率や生産効率を向上させるだけでなく、リードタイムや在庫の削減にも寄与します。Excelなどで管理していた従来の生産計画と異なり、リアルタイムなデータ連携やシミュレーション機能を備えている点が特徴です。
生産スケジューラが必要な理由
製造現場では日々、「納期遅れ」「生産ラインの無駄」「在庫の過剰」など、さまざまな課題が発生します。生産スケジューラを導入することで、以下のような課題を解決できます。
- 生産計画の迅速な立案
- 設備や人員の効率的な配置
- 生産工程の見える化によるムダの削減
これにより、リードタイムの短縮やコスト削減、納期遵守の向上など、経営にも良い影響を与えることができます。
生産スケジューラと生産管理システムの違い
生産管理システムと生産スケジューラは、混同されがちですが、それぞれ役割が異なります。
- 生産管理システム:受注管理、在庫管理、品質管理など、生産活動全般を管理するシステム。
- 生産スケジューラ:特に生産工程のスケジュール管理に特化したシステムで、日々の現場での細かい生産計画をリアルタイムに作成・調整します。
例えば、生産管理システムは「今月中にA製品を500個作る」という大まかな計画を管理しますが、生産スケジューラは「本日、どのラインでA製品を何時から何個作るか」という詳細なスケジュールを決定します。
生産スケジューラ導入のメリット
リードタイム短縮・納期遵守率向上
生産スケジューラを導入する最大のメリットは、リードタイムを短縮し、納期遵守率を高められる点です。リアルタイムで工程の進捗を把握できるため、問題発生時や設備トラブルが起きた際にも迅速なリスケジュールが可能になります。これにより、最短のリードタイムで確実に製品を出荷する仕組みを構築できるのです。
在庫最適化・コスト削減
需要予測と生産計画がリンクすることで、在庫や仕掛品の適正化が進みます。余分な在庫を抱えるリスクが減り、倉庫スペースや在庫コストの削減につながります。さらに、必要なタイミングで必要な資材のみを調達することで、キャッシュフローの改善にも貢献します。
社内外の情報連携強化
生産スケジューラは、ERPやMES、販売管理システムなどと連携し、データを一元管理する役割も担います。営業部門からの受注状況や購買部門の資材手配、外注先への発注などをシームレスに共有することで、部門や協力会社とのコミュニケーションロスを大幅に削減できます。
AIやシミュレーションの活用による予測精度向上
最近ではAIを活用して需要予測の精度を高めたり、生産計画の最適化をリアルタイムで行う生産スケジューラも登場しています。受注の急増や部材の調達遅れなど、変動要因が多い現場でも、AIを使ったシミュレーションで複数のシナリオを立て、最適な計画を導き出すことが可能です。
生産スケジューラの主な機能
ガントチャートによるスケジュール可視化
生産スケジューラは、ガントチャートを用いて作業工程や設備負荷を「見える化」します。一目で現場の状況を把握できるため、管理者や作業者がタイムリーに意思決定を行いやすくなります。
自動スケジューリングと手動微調整
多くの生産スケジューラには、自動で最適な計画を組むアルゴリズムが搭載されています。しかし、現場では突然の仕様変更や緊急受注など、計画通りに進まないケースが日常茶飯事です。そのため、自動計画で作成したスケジュールを人間が微調整できる柔軟性も重要です。
需要予測・在庫管理機能
需要予測エンジンと連携して、来期の需要や売上予測データを元にした生産計画を立案する機能を持つスケジューラもあります。これにより、必要な数量だけを生産する「ジャストインタイム生産」に近づけることが可能です。
作業指示書・実績管理
スケジューラで作成した計画を自動で作業指示書に反映し、現場の作業者に配布するケースもあります。生産が完了すると、実績データがスケジューラに取り込まれ、計画と実績の差異を分析できるため、次回以降の計画精度向上に役立ちます。
生産スケジューラの種類と選定ポイント
オンプレミス型・クラウド型の比較
生産スケジューラは、大きく分けるとオンプレミス型とクラウド型に分類されます。
- オンプレミス型
自社サーバーに導入するため、カスタマイズ性が高い一方、導入コストやメンテナンスコストがかかりやすい。 - クラウド型
インターネット経由でサービスを利用する形態。初期費用を抑えられるうえ、リモートからのアクセスやバージョンアップも容易。
自社のセキュリティポリシーやITインフラ環境に合わせて、最適な導入形態を選ぶことが重要です。
自社の規模・業態に合わせた機能要件
生産ラインの規模、製品の種類、工程の複雑さなどに応じて、必要な機能は異なります。多品種少量生産を行う工場では、変更に強い柔軟性やシミュレーション機能が重視されます。一方、大量生産メインの工場では、高い処理速度や大量データの一括管理が求められるでしょう。
カスタマイズ性とサポート体制
生産管理は業種・企業ごとに独自の要件が多く、パッケージソフトだけでは対応できない場合もあります。そのため、ベンダーがどこまでカスタマイズに応じてくれるか、アフターサポートやアップデート体制が充実しているかを確認しましょう。
生産スケジューラ導入における課題と対策
システム統合・データ連携の壁
既存のERPや販売管理システム、MESなどとのデータ連携が円滑に進まないケースがあります。生産スケジューラを単独で導入しても、上流や下流のシステムから必要なデータを取得できなければ、計画の精度は向上しません。API連携やデータ変換ツールを活用し、システム間の壁をなくす工夫が必要です。
現場の抵抗感・運用定着への対策
「これまでExcelで管理してきたから慣れている」「新しいシステムは使いづらそう」といった声が現場から上がるのは珍しくありません。そのため、導入初期の段階から現場が主体となるプロジェクト体制を敷き、操作トレーニングやテスト導入を行うことが定着の鍵となります。
導入効果測定とKPI設定
導入後は、納期遵守率や在庫回転率などのKPIを設定し、定期的にモニタリングすることが大切です。数値で成果を示すことで、スケジューラの価値を社内に周知しやすくなり、さらなる改善意欲を高められます。
生産スケジューラ導入事例
部品メーカーA社:納期遵守率を大幅改善
A社では、これまでExcelで工程管理をしていたため、急な受注増に対応できず、納期遅れが多発していました。生産スケジューラ導入後は、リアルタイムに生産負荷を可視化できるようになり、遅延リスクを早期に発見。結果、納期遵守率が90%台後半にまで向上し、顧客満足度も高まりました。
製造業B社:在庫コスト削減に成功
B社は季節変動の激しい製品を多品種少量で生産しており、在庫管理が大きな課題でした。需要予測機能付きの生産スケジューラを導入することで、仕掛品や完成品の在庫量を最適化。約1年で在庫コストを30%削減し、倉庫スペースの有効活用とキャッシュフロー改善を達成しました。
C社:AIスケジューラによる予測精度向上
C社は急な仕様変更や試作品の受注が多く、従来の計画では頻繁なリスケジュールに追われていました。AI機能搭載の生産スケジューラを導入したことで、過去データを学習した予測モデルがリアルタイムに複数のシミュレーションを実行。結果、設備稼働率がアップし、短納期の案件でも対応できる柔軟性が生まれています。
生産スケジューラ導入を成功させるポイント
現場主体のプロジェクト体制
導入効果を最大化するには、実際に運用する現場部門の意見を最優先に取り入れることが不可欠です。プロジェクトチームに現場リーダーや熟練作業者を加え、運用フローとシステム仕様をすり合わせることで、導入後の定着度が大きく変わります。
システム連携とデータクレンジング
スケジューラ単独での効果に限界がある以上、ERPやMESなどと連携した一元管理が理想です。その際、既存データの整合性が取れていないとスケジューラに誤情報が入り、かえって混乱を招きます。導入前にデータクレンジングを実施し、マスターデータを整備しましょう。
導入段階からの変革意識共有
生産スケジューラの導入は、単に新しいシステムを入れるだけでなく、生産管理プロセスの再設計を伴います。経営層から現場作業者までが同じビジョンを共有し、今のやり方を変える意識を持つことで、システム導入の真価を引き出せます。
よくある質問(FAQ)
Q1. システム導入にかかるコスト・期間はどれくらい?
導入規模やカスタマイズ範囲によって大きく異なります。中小企業がクラウド型の生産スケジューラを導入する場合、数百万円~数千万円の範囲が多い傾向です。期間は、要件定義やテスト導入を含めて3~6か月ほどが一般的ですが、大規模プロジェクトだと1年以上要するケースもあります。
Q2. 小ロット多品種生産にも対応できるの?
多品種少量生産は変更が頻繁に発生するため、AIやシミュレーション機能が搭載されたスケジューラが有効です。製品ごとや工程ごとの設定を柔軟に行えるシステムを選ぶと、急な仕様変更にも対応しやすくなります。
Q3. 現場のPCスキルが高くないが、使いこなせる?
最近の生産スケジューラは、ガントチャートベースで視覚的に操作できるものが多く、特別なプログラミング知識は不要です。ベンダーによる操作トレーニングやマニュアルが整備されている場合もあるので、サポート体制を確認しましょう。
Q4. 既存の生産管理システムやERPと連携できるか?
多くのベンダーがAPI連携やカスタム開発に対応しており、既存のERPや販売管理システムとのデータ連携が可能です。連携要件を明確化し、システム間のデータ形式を統一する準備を事前に行っておくと、導入がスムーズに進みます。
まとめ
生産スケジューラの将来性と今後のキーワード
生産スケジューラは、従来の計画管理を高度化するだけでなく、AIやIoTとの連携によってさらなる進化が期待されています。たとえば、設備から取得されるリアルタイム稼働データと連動し、自動的にスケジュールを組み直す「自律的な生産計画」なども視野に入ってきています。
次に取るべきアクション
- 自社の課題を洗い出す
- 納期遵守率の低迷か、在庫過多か、属人化か。どの問題を最優先で解決したいのかを明確にする。
- 必要機能と要件を整理する
- ガントチャート、AI予測、クラウド型など、どの機能がどれくらい必要かを検討する。
- ベンダーとの打ち合わせ・トライアル導入
- 実際にデモやトライアル版を利用し、自社の運用に合うかを確かめる。
- プロジェクト体制を整備し、データを整頓する
- 現場を巻き込んでデータを一元化し、スムーズに導入できる土壌を作る。
生産管理スケジューラは、複雑化する現場の生産計画を「見える化」し、在庫最適化や納期遵守率の向上など、多くのメリットをもたらす強力なツールです。しかし、効果を最大化するには属人化した業務を洗い出し、運用ルールやデータ連携の整備を同時に進めることが不可欠となります。本記事で紹介したポイントを参考に、自社の規模や業態に合わせた導入・運用体制を構築しましょう。競争が激化する製造業の現場で、持続的な成長と競争力を確保するための重要なステップとなるはずです。
生産スケジューラの常識を変える、生産計画DXなら「最適ワークス」
生産スケジューラをお探しであれば「最適ワークス」を是非ご検討ください。最適ワークスの魅力は、そのコストパフォーマンス、迅速な導入、使いやすいシンプルな画面UI、手厚いサポート体制です。月額15万円という手頃な価格で、AIによる高度な最適化ソリューションを利用できるのは大きなメリットです。クラウドサービス(Saas)であるため、初期のハードウェア投資や複雑なシステム構築が不要で、導入スピードも非常に速いです。これにより、時間とリソースを節約し、迅速に業務改善を開始できます。
シンプルで直感的な画面UIは、特別な技術知識がなくても誰でも簡単に操作でき、誰でもスムーズに利用できます。また、カスタマーサクセスチームがユーザーと伴走し、最適ワークスを最大限に活用できるようサポートします。導入後も手厚いサービスを提供し、ビジネスの課題解決に直結した支援を行います。
低コストでありながら高機能、そしてサポート体制も充実しているため、DXや業務改善の第一歩として優れたサービスとなっています。
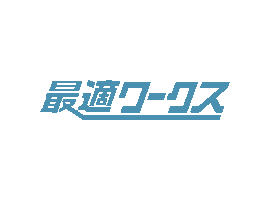
AIが生産計画を自動立案!生産計画・管理のDXを支援する製造業向けSaaS。工場の生産キャパ・製造進捗を可視化。納期回答の精度向上、残業時間を削減など中小・中堅工場での業績改善をサポート。専任エンジニア不要で使える!圧倒的コスパを実現。
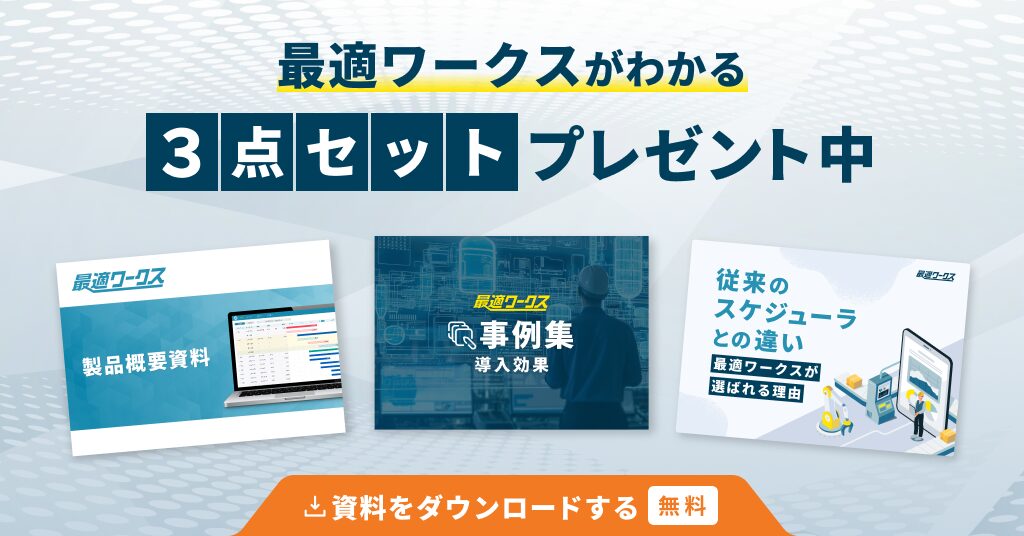