- コラム
工程管理におけるボトルネックの見つけ方|解消方法等も解説
工程管理ではボトルネック工程に着目することが重要です。ボトルネック工程とは生産性の低い工程で、納期遅れや過剰在庫などの問題はボトルネックが引き金になっている場合が多くあるためです。
しかし、数ある工程の中からどこがネックとなっており、それを解消するためにはどのような方法を取るべきかを考えることは簡単ではありません。
そこで今回はボトルネック工程の見つけ方や解消方法について解説します。納期遅れや生産性の低下、過剰在庫などに悩む方はぜひ参考にしてください。
ボトルネック工程とは
ボトルネック工程とは、製造工程の中で最も生産性の低い工程のことです。製造業において、生産工程ごとに処理スピードは異なるのが一般的です。複数の工程の中で一番処理スピードの遅い工程がボトルネック工程に当たります。
たとえばA工程→B工程→C工程→D工程といった工程があったとします。この時、製品1個当たりの処理スピードが10分→8分→15分→11分だとすれば、最も遅いC工程がボトルネック工程です。
『ザ・ゴール』という著書の中で提唱されたTOC(制約理論)では、工場全体の生産性はボトルネック工程以上にはならないとされています。
たとえばA工程で1時間当たり6個の製品を作ったとしても、ボトルネック工程であるC工程では4個しか作れないため、工場全体の生産性は1時間当たり4個となります。他の工程をフル稼働させて、どんなに頑張って生産性を上げたとしても、ボトルネック工程が全体の生産量を決めてしまうのです。
したがって、ボトルネック工程を改善し、いかに生産性を上げるかが工程管理の正しい姿になります。
ボトルネック工程の見つけ方
工程管理においては、まずボトルネック工程を見つけなければなりません。では複数の工程の中からボトルネック工程を見つけるにはどうすればよいでしょうか。代表的な見つけ方を解説します。
1 作業が停滞している工程を探す
1つ目は、作業が停滞している工程を探すことです。作業の中には加工にかかわる時間のほか、段取り替えや機械の調整、部品待ちといった時間も含まれます。
実際に製造している加工の時間よりも、段取り替えや機械の調整などが長くなると作業が停滞しがちです。したがって段取り替えなどが多い工程は作業が停滞しているため、ボトルネックの可能性があります。
2 稼働率が高い工程を探す
稼働率は高い方が望ましいものですが、他の工程よりも高い工程がある場合には注意が必要です。なぜなら他の工程はすでに作業が終わっているのに、まだ稼働している工程は生産性が低いと言えるからです。
他の工程と同じ生産量であるはずなのに、ある工程だけ機械が稼働している時間が長いなら、ボトルネック工程である可能性があるでしょう。
3 製造時間が長い工程を探す
製造時間が極端に長い工程は、処理スピードが遅いためボトルネック工程の可能性があります。1個当たりの製造時間を算出した場合に、他の工程よりも長い工程は注意する必要があります。
ただし、先述のように作業の中には段取り替えや機械の調整といったものもあります。製造時間が長い代わりに段取り替えなどが極端に少なければ、ボトルネック工程に当たらない可能性もあることも念頭に置いておきましょう。
4 トラブルがよく発生している工程を探す
機械トラブルや不良品がよく発生している工程は作業が停滞しがちであるため、ボトルネック工程になる可能性が高くなります。
製造現場を見て回ったり、製造記録を確認したりして、トラブルが発生している工程はどこか、日ごろから見ておく必要があります。
生産計画のDXで業績改善に成功した中小製造企業の取り組みとは?【事例集を無料プレゼント】
熟練社員の持つ技術継承、品質保持や納期対応の安定化など、多くの中小・中堅工場が様々な課題に直面するなか、生産計画のDXを成功させ「残業削減」や「納期遵守率」を大幅に改善させて企業もあります。
生産計画DXを成功させた中小・中堅工場は、どのような取り組みをおこなったのか。
スカイディスク株式会社はこれまで100社以上の生産計画のDX支援実績をおこない、計画工数の削減や納期遅延の解消などを実現してきました。
様々な取り組みの中から、業績改善に成功した中小製造業事例を無料で公開しています。さらに、そのうえで活用される生産スケジューラを選ぶ際のポイントについてもご紹介していますのでぜひご活用ください。
\この資料でわかること/
・生産計画DXによる中小製造業の業績改善事例集
・AIを活用した生産計画の可視化支援サービス「最適ワークス」とは
・最適ワークスが選ばれる理由、生産スケジューラとの比較資料付き
ボトルネック工程の解消方法
工場全体の生産性を向上させたい場合には、ボトルネック工程を解消することが大切です。
どのようなステップで解消すればよいかを解説します。
ステップ1 ボトルネックを見つける
まずはボトルネック工程を見つけましょう。
・作業が停滞している工程はどこか
・稼働率が高い工程はどこか
・製造時間が長い工程はどこか
・トラブルがよく発生している工程はどこか
先述していますが、上記の観点から生産工程を分析していくことで、生産性を低下させている工程を見つけることができます。ただし、ボトルネックは様々な要因が絡むため、なかなか見つけることが難しい場合もあります。
その際は、製造「現場」で「現物」を確認し、「現実」を認識するという三現主義に従って工程を分析することが大切です。
ステップ2 ボトルネック工程を100%稼働させる
ボトルネック工程を見つけたら、その工程の生産性を向上させてフル稼働しましょう。
生産性を上げる方法としては、「段取りの時間を短縮する」「材料や部品の待ち時間を短縮する」「不良品や機械トラブルを削減する」などの方法があります。生
産性を高める方法としてまず作業スピードを上げることを考えがちですが、作業スピードの向上よりも生産をストップさせている要因に着目する方が効果的です。
ステップ3 ボトルネック工程にすべての工程を合わせる
次の段階で必要なのは、他の工程の都合でボトルネック工程の生産をストップさせないことです。そのため、ボトルネック工程に他のすべての工程を合わせるようにスケジューリングします。
具体的には部品の待ち時間が発生しないように、前工程がボトルネックに合わせて部品を流すようにします。前工程でトラブルが発生した際に生産がストップしないように、ある程度の仕掛け在庫を持っておくことも大切です。
後工程はボトルネック工程から部品が流れてきたらスムーズに生産に着手できるように準備させます。このようにスケジューリングすれば部品がスムーズに流れ、全体として生産性を向上することができます。
また、他の工程をボトルネックの生産量に合わせることも重要です。ボトルネック工程以上に作りすぎないことで、過剰在庫を防ぐことができるからです。
ステップ4 ボトルネック工程の生産能力を上げる
続いて、ボトルネック工程の生産能力を上げることはできないか検討しましょう。具体的には新しい機械を購入したり、人員を増員したりといった投資です。そもそも生産能力が低いのは、設備が古い、人員が不足しているなどが原因かもしれません。
また、「処理スピードを上げる」「段取り替えの時間を削減する」といった改善活動も大切ですが、そればかりで生産能力を向上させるのは限界があります。そのため、設備投資も行うことで生産能力の向上を後押しします。
もう一つ有効なのは「多能工化」です。ひとりの作業者ができる作業や工程を増やすことで、工場全体の生産性を上げることができます。たとえば旋盤工程だけでなく、焼入れや研磨といった工程もできるようになれば、研磨工程に人手が不足している場合に応援に回ることが可能になります。
設備投資と作業者のスキルアップの両面からボトルネック工程の生産能力を向上させましょう。
ステップ5 1~4を繰り返す
ボトルネックを解消するためには、継続的な改善が欠かせません。そのため、1~4を繰り返して工場全体の生産性を上げることを目指しましょう。
具体的な手法としてPDCAが有効です。Plan(計画)、Do(実行)、Check(測定・評価)、Action(対策・改善)といった仮説と検証を繰り返すことで、改善目標を達成できるからです。
ボトルネック工程を解消した事例
ここでは事例として、ある医療機器の部品メーカーを紹介します。その会社が課題として挙げたのは納期遅れでした。納期遅れが頻発していたため、どうにかして生産性を向上できないかと考えます。
製造工程は、切断→加工→研磨→化学処理→洗浄→検査→出荷です。重要な工程は研磨工程で、製品の品質を左右するところでした。仕掛け在庫も研磨工程でたまっているため、ボトルネック工程は研磨だと分析します。
ところが各所から話しを聞いていると、実は研磨工程の都合で生産を行っていることが分かります。仕掛け在庫がたまっているのも、研磨工程の稼働率を上げるためでした。
そこで部分最適でなく全体最適の視点から分析を進めていくと、本当のボトルネック工程は洗浄だと分かりました。洗浄工程を最大限に活用するために「交代制を導入して洗浄設備の稼働時間を長くする」「洗浄機のレイアウトを変更する」「使っていない設備を活用して能力を高める」などの方法を取ります。
結果として洗浄工程の生産性を上げることに成功し、納期遅れも大幅に解消できました。真のボトルネック工程を見つけて改善に成功した事例です。
(参照 株式会社みどり合同経営 ボトルネックの改善で納期遅れを解決したS社の取り組み【今日から実践!基本からの生産管理・第7回】)
ボトルネック工程は常に存在する
ボトルネック工程に着目して改善を行う場合に大切なことは、ボトルネックは常に存在するということです。
A工程→B工程→C工程→D工程の処理スピードがそれぞれ10分→8分→15分→11分だったとします。最も遅いC工程の生産能力を上げて10分にしたら、次に生産能力の低いのはD工程になります。
そのため、ボトルネックは常に存在するという視点から継続的な改善を行うことが重要です。
最適ワークスの導入で、誰でも均質な生産計画を作成、管理できる!
直感的な入力作業で製造工程をデジタル化する。
最適ワークスでは、特定の社員の勘や経験に依存することなく、製造条件や独自ルールといった制約条件を考慮した、最適な生産計画をAIが立案します。具体的には、「どの製品を・何個・いつまでに」という受注情報(オーダー情報)から、設備・人員の最適な計画作成が可能です。
導入におけるメリット
・納期遅延を30%解消
・計画工数98%削減
・生産量10%アップ
・不良品・事故0件
・残業20%削減
まとめ
どんな工場でもボトルネック工程は存在するため、工程管理ではボトルネックに着目して改善を行うことが重要です。
まずは、ボトルネック工程を見つけて稼働率を上げるようにしましょう。続いて、ボトルネック工程に合わせて他の工程をスケジューリングします。
しかし、ボトルネック工程に合わせてスケジューリングするのは、エクセルなどを使っても手動では難しいものです。そこで、そのような時に効果的なツールが生産スケジューラです。
生産計画を自動立案できる生産スケジューラなら、ボトルネック工程に合わせて他の工程を簡単にスケジューリングできます。ボトルネック工程の解消に合わせて、生産計画業務を効率良く最適化したいのであれば、ぜひ便利なツールの活用をご検討ください。
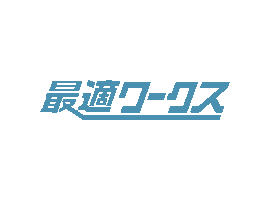
AIが生産計画を自動立案!生産計画・管理のDXを支援する製造業向けSaaS。工場の生産キャパ・製造進捗を可視化。納期回答の精度向上、残業時間を削減など中小・中堅工場での業績改善をサポート。専任エンジニア不要で使える!圧倒的コスパを実現。
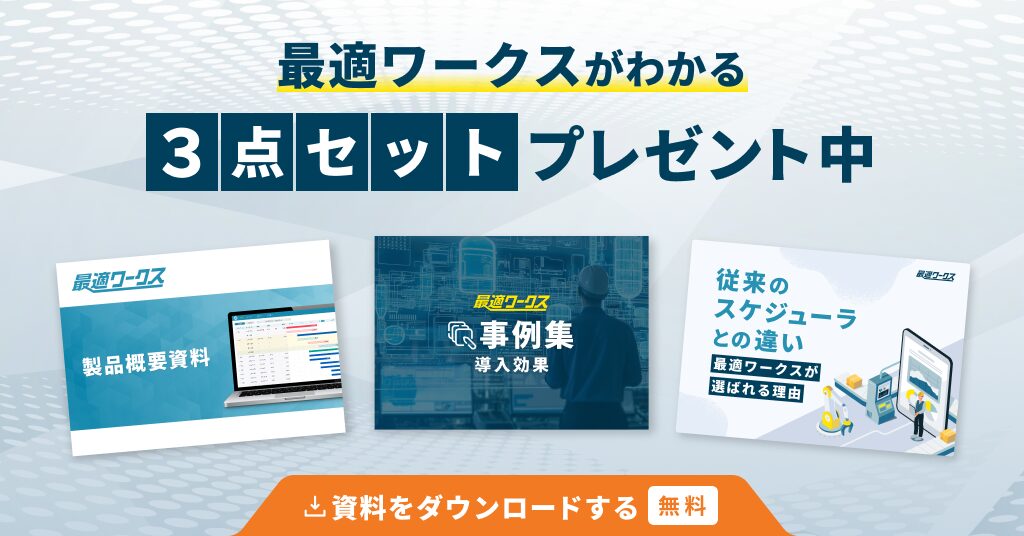