- コラム
生産リードタイムを短縮する方法|短縮するメリット・注意点も解説
製造業において、リードタイムという用語は切っても切れない関係にあるほど重要なものです。なぜならリードタイムを短縮することにより、企業競争力の向上やコスト削減などを達成できるからです。
ただし、リードタイムを短縮する方法は一つではありません。そこで本記事ではリードタイムとは何か、リードタイム短縮のメリットやその方法について解説します。
生産リードタイムとは
生産リードタイムとは、実際に生産を開始してから終了するまでにかかる時間のことを指します。
生産リードタイムを短縮することで、在庫の削減や短納期に対応できるようになるなどの様々なメリットをもたらすため、優先度の高い課題と言えるでしょう。
また、生産リードタイムには実際に製造にかかわる時間だけでなく、運搬や工程の待ち時間などの停滞時間も含まれます。そのため、生産リードタイムの短縮にはこういったムダな時間を解消していくことも含まれます。
なお、製造業に関わるリードタイムには生産リードタイム以外にも、開発リードタイム(製品の企画、開発設計、生産準備といったプロセスにかかる時間)、調達リードタイム(部品や原材料といった資材を取引先に依頼してから実際に納品されるまでにかかる時間)、配送リードタイム(出荷の指示を出してから顧客に製品が納品されるまでに要する時間)の3つのリードタイムがあります。整理して覚えておきましょう。
リードタイムに関連する用語
リードタイムと混同されやすい用語に「タクトタイム」と「サイクルタイム」があります。タクトタイムとサイクルタイムも生産性向上や効率化に欠かせない用語のため、ここで整理しておきましょう。
タクトタイム
タクトタイムとは、製品1個あたりの製造時間のことです。以下のように計算します。
・タクトタイム=稼働時間÷必要生産数
タクトタイムはオーダーの数量に対して、1個あたり何秒かかるかを表したものです。
サイクルタイム
サイクルタイムは、ひとつの製品において工程開始から完了までの1サイクルにかかる時間のことです。以下の計算方法となります。
・サイクルタイム=稼働時間÷実際の生産数
サイクルタイムとタクトタイムは、よく混同されます。タクトタイムはオーダーをこなすために1個あたり何秒で生産すればよいかを導き出したものです。一方のサイクルタイムは自社の生産設備で1個あたりにかかった製造時間であり、それぞれ目線が異なります。
生産リードタイム短縮のメリット
生産リードタイムはできるかぎり短縮することが大切です。短縮すると「コスト削減」「キャッシュフローの向上」「自社サービスの差別化」につながります。
生産リードタイムメリット1 コスト削減
生産リードタイムの短縮は仕掛り在庫を抑えることができるため、コスト削減につながります。仕掛り在庫とは工程と工程の間に滞留している在庫であり、製品を完成させるためには欠かせない在庫ではあります。
しかし、仕掛り在庫が過剰になってしまうと保管スペースが足りなくなり、在庫管理に要する人手も必要となるため、コストが増加します。生産リードタイムを短縮すると、工程の待ち時間が短くなり、それに伴って仕掛り在庫も減らすことができるのです。
生産リードタイムメリット2 キャッシュフローの向上
製品在庫は企業の資金が形を変えたものであり、棚卸資産です。つまり、在庫を長期間抱えるということはキャッシュフローが減少し、企業の資金繰りを苦しくする一面があります。さらに製品在庫を過剰に抱えると、品質が劣化したりデッドストックになったりします。
しかし、生産リードタイムを短縮すると受注から納品までの期間が短くなり、キャッシュフローが改善します。キャッシュとして持っていれば流動性が高く、投資のチャンスになるため、生産設備や人員などに適切な投資が可能になり将来的に利益を拡大できるのです。
生産リードタイムメリット3 他社との差別化
リードタイムを短縮できると、顧客が要望する短納期にも対応できるようになり、納期の面で他社より競争優位になります。近年では短納期化が進んでいると言われており、納期にスピーディーに対応することで販売機会の増大にもつながるでしょう。
また、これまでにはない新製品を素早く市場に投入すれば、競合他社がいないため先行者利益を獲得できるというメリットもあります。このように生産リードタイムの短縮は単なる在庫削減やコスト削減だけでなく、企業の市場競争力をアップさせる役割を持ちます。
生産リードタイムを短縮する方法
では、生産リードタイムを短縮する方法には何があるでしょうか。ここでは代表的な7つの方法について解説します。
方法1 生産計画の最適化
生産リードタイムを短縮するには、生産計画の段階から考えることが重要です。たとえば効率だけを考えてまとめ生産を行うとリードタイムは長くなりますが、小ロットでの生産を計画できれば工程の待ち時間は少なくなるため、リードタイムを短くできます。
また、各工程で生産に着手するタイミングを合わせる同期化も必要となります。組み立て工程の場合、前工程から部品が流れてこないと必要な部品が揃わず生産に着手できません。そこで組み立て工程が欲しいタイミングに間に合うように、前工程の着手順序を計画段階で作り込みます。
しかし、小ロット生産や工程間の同期化をエクセルや人手で考えることは難しいものです。生産計画を自動立案できる生産スケジューラは、リードタイム短縮を含めた生産計画の最適化に役立ちます。
各工程の生産状況の見える化ができるため、「工程を同期させる」「段取り替えの回数を極力減らすように小ロットでの生産を計画する」といった難しいスケジューリングも可能です。
生産スケジューラについては、こちらで詳しく解説しています。
「生産スケジューラとは?導入メリット・導入の流れを解説」
方法2 段取りの無駄を無くす
生産リードタイムを分解すると、加工や組立などの製品に付加価値を与える時間と運搬や検査、待ち時間のほか、段取りにかかる時間もあります。そのため段取りの中に無駄があればそれを排除することでリードタイムを短縮できるのです。
段取りは外段取りと内段取りに分けられます。外段取りとは生産を止めずに行う段取りであり、内段取りは生産を止めてから行う段取りです。段取りの無駄を無くすためには、できるかぎり外段取りで行える作業を増やします。また原料を準備する手間も減らすように努力するとよいでしょう。
方法3 運搬の無駄を無くす
トヨタ生産方式が提唱している「7つのムダの排除」で排除するべきムダの1つとしても挙げられている「運搬のムダ」。リードタイム短縮のためには運搬にかかる時間を減らす必要があります。もし設備のレイアウトを変更できるようなら、生産の流れを意識して各工程の配置を近づけると運搬に要する距離も短くなります。
運搬の無駄は、回数も大きな要因となります。たとえば製造現場が予定生産数よりも多く作ってしまった場合、そのぶん製品を運搬する回数も増えてしまいます。そのため、距離を短くするとともに、回数も削減することが大切です。
方法4 整理整頓する
製造業では5S(整理、整頓、清掃、清潔、しつけ)が重要だと言われています。中でも整理・整頓を徹底すると現場に潜む無駄を排除することができ、作業時間の短縮につながります。整理とは、使うモノと使わないモノを分けて、不要なモノを捨てることです。整頓は、必要なモノを定められた場所に保管し、使いやすい状態にします。
整理と整頓の徹底された現場では、作業者が工具を探すために手を止めてしまうなどの無駄がなくなり、結果として効率のよい生産が可能となります。
方法5 人員配置の最適化
人員配置を計画的に行うのもリードタイム短縮に効果的です。各工程の負荷に応じて適切に人員を配置すれば、ボトルネック工程に応援を回すことができるため効率的な生産が可能になるでしょう。
さらに多能工化を推し進めると、従業員が幅広い業務をこなせるため、よりフレキシブルな人員配置を計画できます。
方法6 作業を標準化する
現場の従業員ごとに作業方法や手順がバラバラだと、標準の作業時間よりも時間がかかってしまうため、リードタイムを長くする要因になります。それを防ぐためには作業を標準化し、すべての人が同じレベルで作業ができるようにすることです。マニュアル作成や作業手順の見直しを定期的に行うのがよいでしょう。
方法7 不良品発生率を抑える
生産時間を長くする要因には、不良品の発生も関係しています。なぜなら不良品の発生率が高くなると機械の調整に手間取ったり、予定生産数までに多くの時間を要したりするためです。不良品を抑えるためには、QC7つの道具(データを活用した品質管理のフレームワーク)や三現主義(現場で問題の解決を図るフレームワーク)などが効果的です。
生産リードタイムを短縮する際の注意点
生産リードタイムの短縮にあたって以下のような注意点があります。
・部門間の連携を強化する
・QCDのバランスを適切に保つ
生産リードタイムの短縮は、製造部門や生産管理部門だけが取り組むのではなく、全部門が協力しなければなりません。たとえば調達部門の材料手配が遅れてしまえば、製造は手待ちが発生します。そういった問題を防ぐためにも部門間の連携を強化して生産計画の最適化を図りましょう。
またリードタイムの短縮だけにとらわれてしまうとQCDのバランスを崩しかねません。作業時間の短縮のために設備や人員を増やせば、間違いなくコストが増大します。自社の最適なQCDのバランスを見極めながら、生産リードタイムの短縮に取り組むことが重要です。
まとめ
生産開始から終了までの時間を意味する生産リードタイムは、コストやキャッシュフロー、企業競争力など、多岐にわたって影響を与える重要なものです。
生産リードタイム短縮の手法としては、運搬や段取りの無駄を無くしたり、人員計画を作りこんだりといったことも考えられますが、生産計画の最適化も効果があります。
もしエクセルや人手では生産計画を最適化できないとお悩みの方は、生産計画を自動立案できる生産スケジューラをぜひご検討ください。
生産性や品質不良にお困りの方に。AIを活用した生産計画の可視化・カイゼン支援サービスである最適ワークスの導入で製造効率をアップしよう。
最適ワークスの特徴と導入効果
最適ワークスとはAIを活用した生産計画の可視化・カイゼン支援サービスです。
🔸特徴と導入効果
・計画機能では、納期・条件・標準時間を遵守。予定外の残業を削減する。
・計画に対する焦りをゼロに。不良品やトラブルを軽減させる。
・長期の計画平準化により、原価率を改善。
計画機能では、納期・条件・標準時間を遵守。予定外の残業を削減する。
最適ワークスでは、AIが生産計画を自動立案します。具体的には、「どの製品を・何個・いつまでに」という受注情報(オーダー情報)から、設備・人員の最適な計画作成が可能です。計画工数が大幅削減できるので、空いた工数で製造現場の改善活動を進めることができます。
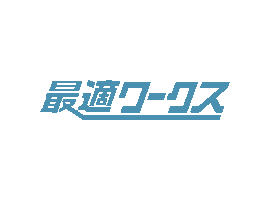
AIが生産計画を自動立案!生産計画・管理のDXを支援する製造業向けSaaS。工場の生産キャパ・製造進捗を可視化。納期回答の精度向上、残業時間を削減など中小・中堅工場での業績改善をサポート。専任エンジニア不要で使える!圧倒的コスパを実現。
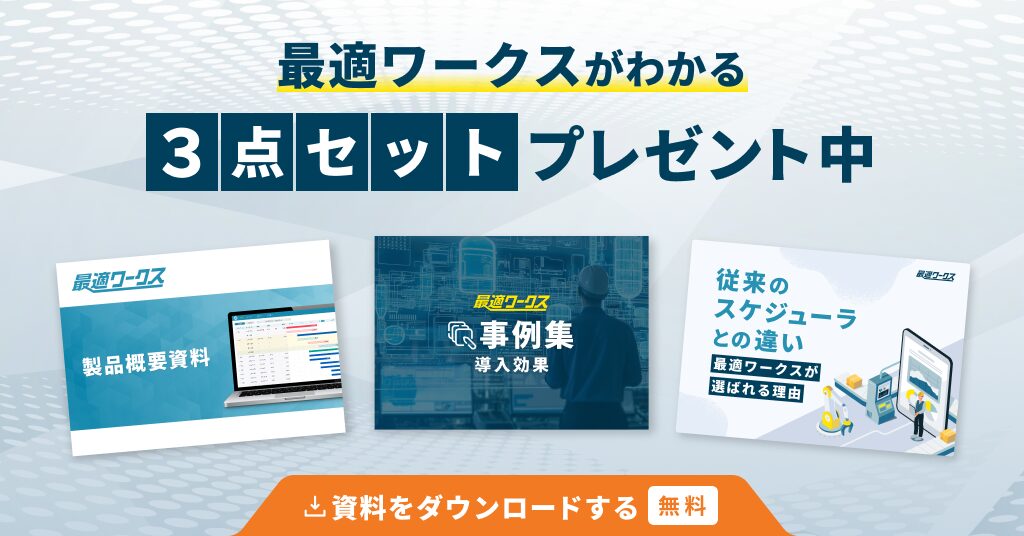