- コラム
生産計画を使うことがゴールだけど、生産計画を作れることも大切だしすごい、という話
ご存じの通り当社スカイディスクでは、生産計画の立案をAIが支援し、中堅・中小企業の生産管理を支援する「最適ワークス」を提供しています。そういった中で、生産計画を活用して、どう生産管理を機能させるかについて話すことが多いのですが、今日はその一歩手前の話、生産計画を作るということについて考えていきたいと思います。
「マスター情報がない」、製造工程は班長の頭の中に
生産計画を用いて生産管理をしっかり回していきましょう、という類のウェビナーや講演をすると、必ずといってもいいほど、製品の製造工程マスターについての質問を受けます。具体的には、うちの工場では製品毎に製造工程を書き出して、各工程の作業時間を整理するところから始めなければいけないが、これをどうやって進めていったらいいか、といった類のご質問です。
各現場の班長やリーダーが、オーダーをこなすことにコミットし、しっかりやり切る、という、暗黙の合意のもと日常業務が進められている現場は多いのではないでしょうか。
各責任者が業務執行にコミットするので、各現場責任者以外に具体的な仕事の進め方は分からないし、納期通りに終わらせるという約束が守られている限り踏み込むこともない。
……そういった前提で業務が進んでいたとすれば、製品毎にどう製造を進めていくかという情報であるマスター情報が言語化できていない、というのも不思議ではないかと思います。
なぜ今、製品マスターの言語化が必要なのか
いま、この現場の進め方が、徐々に機能しなくなっているのだろうなと感じます。これは改めて詳細に考えてみる機会を持ちますが、今回は概要のみご紹介します。
現場力、あうんの呼吸が通用しない
まず一つには製造業全般にある人手不足の問題です。人手不足が慢性化する中で、非正規雇用や海外技能実習生の登用により人手をまかなっている工場は多くあります。
こういったスタッフは熟練工と比較すると経験値が低いケースが多く、言語の問題も相まって「あ、うん」の呼吸で仕事を進めることは難しくなっています。加えて、働き方改革の影響から、残業をしてどうにか終わらせる、という仕事の進め方も難しくなってきています。
多様化するオーダーに現場を回し切れない
二つ目の理由として、取引先の多様化と取扱品目の拡大があげられます。個性を重視する消費者嗜好の変化や、大手完成品メーカーによる海外現地での直接製造・販売が増えていることにより、大量生産・大量販売の時代から少量多品種へとシフトし、また各社ごとの注文量は全般的に減少している印象です。
そういった中で、太客である特定の完成品メーカーの仕事だけでは売上高が維持できなくなったり、取引先から要求される部品点数が増えたりなど、製造現場に対する期待値も多様化しています。
こういった状況の中、小ロット多品種製造が多くなり、製造現場のカン・コツだけでは効果的に製造を回せなくなってきているのが現状です。
これらの理由から、やはり経営や生産管理の視点としては生産計画を活用し、生産管理体制を浸透させていきたい。その為にも、これまで言語化してこなかった製品マスターを作らなければいけないが、どう進めたらいいか、そういった悩みが出てきているのかな、と拝察しています。
マスター情報の整理をどうやって進めるべきか?
時間を割り切らず、通常業務と並行して進める
この質問に対しては、「まずは仮で、適当でもいいから業務と並行してマスター整備と登録を進めていってはいかがでしょう」、というご回答をさせていただくことが多いです。
大企業であれば生産管理の担当者が、製品毎の製造工程マスターを書き出したうえで、実際の作業工程をストップウォッチで測り、何百回と同じ作業をする中で標準作業時間を統計的に割り当てて……と製造マスターを精緻化していくことはあるかもしれません。
一方で、中堅・中小企業では、製造現場だけでなく工場の運営サイドも、生産管理も人手が足りていないことが常です。こういった進め方はリソースの面だけでなく、時間軸の観点から見ても魅力的な選択肢ではないことが多いでしょう。
まずは目安時間で入力
したがって、スカイディスクではよく計画をシステム上で仮作成しながらこのマスターの調整をしていくことをお勧めしています。まずは目安でもいいから製造マスターを作ってみます。段取り時間は計測できていなくてわからないけど、ひとまずは前も後も20分、作業時間は300回設備が作動する工程だから大体30分……など、ときには現場責任者と話をしつつ、何となくの想定ベースで数値を設定してもらえばいいかと思います。
計画と実績のずれを修正していく
こういった設定をして計画を実際に立案してみると、大体の場合において、スケジュールが合わないことが通常かと思います。出来上がった計画上で製造できる製品数が、実際の製造数よりも圧倒的に少なかったり、多かったりするかと思います。少ないときには、作業工程に余裕を見過ぎているので、どこに余裕が出すぎているかを見てみる、多いときには、作業工程に余裕が無さ過ぎるので、どこが遅延しているかを見て修正する、こういった修正を進めていきます。
この違いを把握するために、生産実績や各作業者の日報と計画内の想定数値を突き合わせてみたり、あるいは作業者にヒアリングをしたりしていくことで、工程毎の作業時間を合わせていきます。
システムで今までの計画を再現しない
生産計画の仮作成段階では、作業順序など計画の見え方ではなく、計画上想定されている製造量と実際の製造量を見つつ計画の妥当性を検証していくことをお勧めしています。
これまで生産計画を作ってきた、という工場であっても、多くの工場においてその計画通り業務が進められていたのかは把握できていないのが現状です。そういった状況であれば、これまでの計画自体そもそも正しかったのかが検証できていない、というわけです。そうだとした場合、これまでの計画に似せて計画を作っていくのが、使える生産計画を作るという観点からは無駄である可能性があります。
したがって、これまで比較できていなかった計画の見え方ではなく、比較可能な生産数量を実績と突き合わせ、計画の妥当性を図ることをお勧めしています。
生産計画が作れている状態に向け、第一歩を
この文章タイトルに、生産計画が作れること自体すごいこと、と書かせていただきました。
「最適ワークス」上で「生産計画が作れている」状態というのは、つまり概ね製造マスターが可視化され、工程毎の業務把握が必要十分なレベルでなされ、その結果として実際の製造量と近しい数値を示す生産計画ができている、ということです。
これが実現できているのならば、実効性の高い生産管理と、改善活動が開始できる状況にあることを示しています。
「生産計画が作れている」状況は、生産管理をする上では第一歩に過ぎませんが、一番大変で、大切な第一歩であることも間違いありません。さらに言えば、工程を可視化する中で同一作業をこなしていく時間の作業者ごとのブレが把握でき、これを平準化するための活動に着手する、などの状況もあることから、既に改善活動が始めていて、二歩目を踏み出している会社もあるのではないかと思います。
さいごに
日本の製造業を取り巻く環境は、バブル崩壊以降、大きく変化してきました。製造業の持続的な成長のためには、事業環境の変化にあわせ適切なテクノロジーを活用し、また、特に生産管理面での属人性を解消することで改善活動をルーティン化させていくことが重要です。
スカイディスクは「最適ワークス」の提供を通して、これを実現するために製造業の皆様が費やす時間と努力を無駄にせず、またできるだけ効率的に進めていけるお手伝いをしています。生産計画を活用して生産管理体制を整備し、業績改善につなげたいと考えている企業様は、まずは一度当社までご相談ください。
最適ワークスの導入で、誰でも均質な生産計画を作成、管理できる!
直感的な入力作業で製造工程をデジタル化する。
最適ワークスでは、特定の社員の勘や経験に依存することなく、製造条件や独自ルールといった制約条件を考慮した、最適な生産計画をAIが立案します。具体的には、「どの製品を・何個・いつまでに」という受注情報(オーダー情報)から、設備・人員の最適な計画作成が可能です。
導入におけるメリット
・納期遅延を30%解消
・計画工数98%削減
・生産量10%アップ
・不良品・事故0件
・残業20%削減
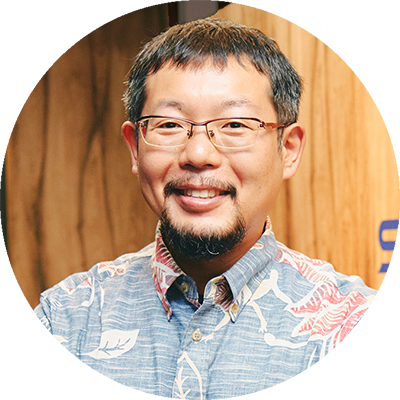
取締役 CSO
投資銀行、コンサルティングファームを経て、経営企画部責任者としてじげんに入社、IPOを主導。IPO完了後はM&A戦略の立案に携わり、その後子会社社長として金融領域の新規事業企画に携わる。INCLUSIVE参画後、組織整備ならびに事業ポートフォリオの再構築に着手し、黒字転換を果たしたのち上場。上場後はCOO/CSOとして、M&A、IRから新規事業企画、子会社PMIと幅広く活動。M&Aを中心とした戦略で2年間で事業規模を上場前の4倍へと成長させた。2022年7月、株式会社スカイディスク 取締役に就任。
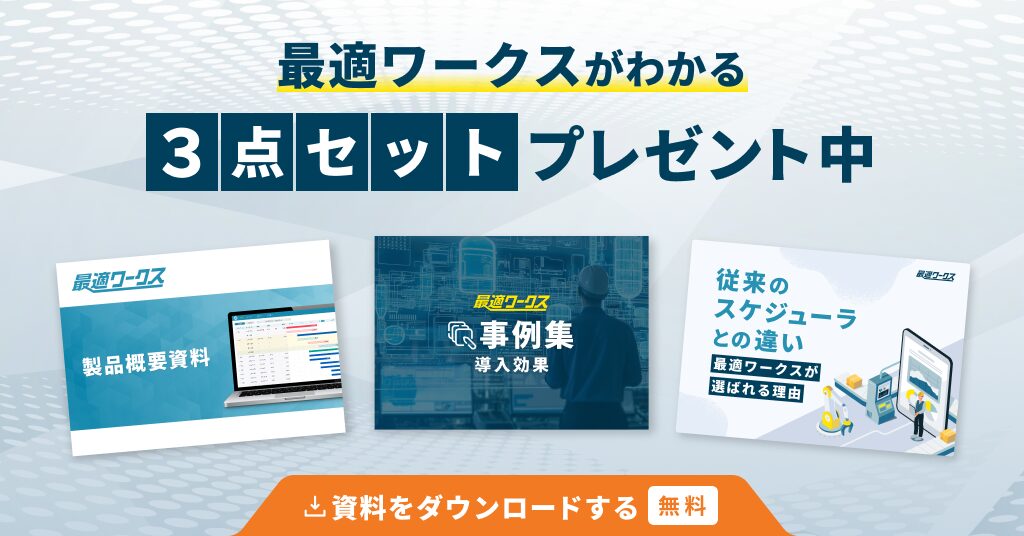