- コラム
MRP(資材所要量計画)とは?生産管理の基本・仕組みから導入メリット、システム選定まで徹底解説
製造業を取り巻く環境が大きく変化する現代において、生産管理の効率化は喫緊の課題です。グローバル競争の激化、原材料価格の高騰、顧客ニーズの多様化といった外部要因に加え、人手不足や働き方改革への対応も求められ、生産現場はより一層の効率性と柔軟性を求められています。
そこで改めて注目されているのが、MRP(資材所要量計画)という考え方です。MRPは、在庫の適正化、資材調達の最適化、生産効率の向上を実現し、企業の競争力強化に貢献します。
本記事では、MRP(資材所要量計画)の基本、仕組み、導入メリット・デメリット、システム選定のポイントまで、生産管理担当者が知っておくべき情報を網羅的に解説します。MRPの導入を検討している方はもちろん、生産管理の基礎知識を深めたい方にも役立つ内容です。ぜひ最後までお読みいただき、貴社の生産管理改革にお役立てください。
1. MRPとは?概要と定義
MRP(資材所要量計画)の概要
ここでは、MRPの基本的な概念と定義について解説します。
MRP(Material Requirements Planning)とは、「資材所要量計画」と訳される生産管理手法の一つです。MRPは、BOM(部品表)、在庫情報、生産計画に基づき、必要な資材を必要なタイミングで必要な量だけ調達するための計画を立てます。
かつての製造業では、過剰在庫を抱えることで欠品リスクを回避する生産管理が主流でした。しかし、過剰在庫は保管コストの増大、キャッシュフローの悪化、陳腐化による廃棄ロスといった問題を引き起こします。
このような背景から、在庫を最適化し、生産効率を向上させるMRPが注目されるようになりました。MRPは、過剰在庫を削減しコストを抑制すると同時に、欠品リスクを最小限に抑え、納期遵守率を向上させることを目指します。
MRPの基本的な目的
MRPがもつ基本的な目的は以下の通りです。
- 在庫の最適化:必要な材料や部品の過不足をできるだけ減らし、在庫コストを削減する。
- 適正コストの維持:材料の発注タイミングをコントロールすることで、無駄な在庫費用や急な手配費用を防ぐ。
- 必要な資材を必要な時に用意:納期遅延の防止や生産の途切れを防ぎ、顧客満足度の向上や生産効率の向上につなげる。
このようにMRPは、企業の生産活動における “資材の最適調達” と “コスト管理” を両立する重要な仕組みとして位置づけられています。
2. MRPの仕組み・機能
MRPの定義と基本プロセス
MRPを機能させるためには、大きく以下の要素が必要です。
- BOM(部品表):製品を構成する部品や原材料、サブアッセンブリの構造を表した表。
- 需要予測(販売計画):どの時期にどれだけの製品が必要になるかの見込み。
- 在庫情報:現在の在庫量だけでなく、すでに発注済みの材料や仕掛かり品の状況も含む。
- リードタイム:発注から納品まで、または生産開始から完成までの時間。
MRPのプロセスを簡単に説明すると、まずは需要予測や受注情報をもとに「製品を何個作る必要があるか」を確定します。そして、BOMを参照し、「製品1個あたり部品Aが何個必要か」といった情報から、合計でどれだけの資材を準備すべきかを逆算します。これにリードタイムや在庫量を考慮し、「いつ、どのくらい発注すればよいか」を割り出すのです。その後、実際に購買・発注指示や生産指示が行われ、手配された材料が納入・生産されることで在庫が補充されます。この一連の流れを、MRPは繰り返し計算して管理していきます。
MRPの仕組みをわかりやすく解説
MRPは、在庫管理システムや生産管理システム上で動いています。そこには各資材の現状在庫数や、すでに発注している材料の納入予定数、そして外注先や自社工場で生産中の仕掛かり在庫数などが含まれます。MRPの計算では、こうした手持ち在庫や発注在庫を反映させながら、「不足分のみを新たに発注する」ようにすることで、過剰在庫を削減し、必要分のみを手配できる仕組みになっているのです。
一方で、MRPは“無限能力”を前提に計画を立てることが多い点も特徴です。つまり、MRPの計算ロジック上は、「生産能力や設備の稼働可能時間」に縛られない形で必要なタイミングを計算します。しかし実際の工場では、人員や設備の能力に制約があるため、最終的には能力計画やスケジューラとの連携が必要となります。
能力計画とMRP / 生産計画とMRP
MRPは資材面にフォーカスした計画システムであり、たとえば工作機械や組立ラインなどの「処理能力」「稼働時間」という制約を直接は扱いません。そこで「能力計画(Capacity Planning)」や「生産スケジューリング」を組み合わせることで、MRPによる資材所要量と、実際の工場稼働の整合性をとります。
具体的には、MRPで資材の手配・納期を算出したあとに、能力計画ツールや生産スケジューラなどで「いつどの設備でどの順番で生産するか」を細かく決める流れです。このようにMRPは、工場の生産指示やスケジュール策定において、非常に重要な役割を担っていますが、単独ですべてを完結させるわけではなく、他のシステムや部門との連携が欠かせません。
3. MRPと関連する用語・システムとの比較
MRPとERPの違い
MRPは資材面に特化した計画手法・システムです。一方、ERP(Enterprise Resource Planning)は企業全体の経営資源を一元管理するシステムであり、人事管理や会計管理、販売管理なども含め、より広範囲の業務を統合的に扱います。
近年のERPパッケージには多くの場合、MRP機能も標準的に組み込まれています。そのため、ERPの導入によって生産管理だけでなく、購買、生産、在庫、販売、会計といった情報がすべて一元化されるため、データ整合性が高まり、業務効率も向上します。ただしERPは包括的なため、導入・運用コストやカスタマイズの負荷が高い場合もあります。企業の規模や業態によっては、まずは単体の生産管理システム(MRP機能搭載)を導入したほうがスムーズな場合もあります。
MRP IIとは何か?
MRPが登場した当初は、あくまで「資材」に焦点を当てていました。しかし工場全体を見渡すと、前述のように設備や人員などの“能力制約”があるため、資材計画だけでは不十分です。そこでMRPに能力計画やシミュレーション機能を組み込んだ拡張版が登場し、これが**MRP II(Manufacturing Resource Planning)**と呼ばれます。MRP IIでは、資材だけでなく、生産工程全般を包括的に管理する仕組みとして発展し、その後さらに経営資源全体を扱うERPへとつながっていく流れがあります。
JIT・制約理論・DDMRPなど関連手法との関係
-
JIT(Just In Time)
トヨタ生産方式で知られる「ジャストインタイム」は、必要なものを必要なときに必要な量だけ供給するという考え方です。MRPと目指す方向は似ていますが、JITは看板方式などを用いて現場主導で在庫を最小化する手法です。一方MRPは、システム計算で発注タイミングを管理します。どちらも在庫最小化を目指しますが、そのアプローチや管理手段が異なります。
-
制約理論(TOC: Theory of Constraints)
制約理論は、工場全体の生産フローの中でボトルネックとなる工程や設備を特定し、その制約を最大限活かすように計画を組む考え方です。MRPで手配した材料があっても、ボトルネック工程で詰まると製品が完成しない場合があります。そこでTOCを活用し、ボトルネックを中心に生産計画を組むといった手法が注目されています。
-
DDMRP(需要駆動型MRP)
従来のMRPは需要予測に依存する面が大きく、需要変動が激しい時代には運用が難しい場合があります。DDMRPはバッファ管理などの新しいアプローチを取り入れ、需要変動に迅速に対応する考え方です。MRPと同じくBOMやリードタイムの情報を活用しますが、より“需要変動が激しい環境”に対応できるよう工夫されています。
4. MRP導入のメリットと課題
MRPシステムのメリット
- 在庫削減・最適化によるコストダウン需要に合わせて資材を調達するため、過剰在庫を抑えられます。また欠品リスクが低減し、納期遅延のペナルティコストや特急手配コストも削減できます。
- 生産スケジュールや購買指示の自動化による効率化MRPによって必要量と必要時期をシステムが計算してくれるため、担当者の手作業を大幅に減らすことができます。手配ミスも減少し、業務品質が向上します。
- 計画変更への柔軟な対応需要予測や受注量が変動した場合、MRPの再計算を行うことで最新の計画を即座に反映可能です。手動での再調整作業が軽減されるだけでなく、誤差を吸収しやすくなります。
MRP導入のデメリット・運用上の課題
- データ管理やマスタ整備の煩雑さMRPには正確なBOM、リードタイム、在庫データなどが必須です。もしこれらのマスタ情報に誤りや抜けがあると、計画結果も大きく乱れます。定期的なメンテナンスやアップデートが欠かせません。
- 需要予測精度への依存MRP計算の根拠となる需要予測が大きく外れると、在庫過多や欠品を招きます。特に変動が激しい市場では、需要予測精度を高めるために他の取り組み(AIの活用や営業部門との連携)も必要です。
- 部門を超えたコミュニケーションの必要性MRPは生産管理部門だけでなく、購買や営業、物流など多くの部門がデータを共有・活用する仕組みです。社内コミュニケーションが取れていないと、データの遅れや二重入力が発生してしまいます。
5. MRP対応の生産管理システム・ソフトウェア
MRP対応システムの新旧比較
-
オンプレミス型
昔ながらのサーバーを自社内に置き、ソフトウェアをインストールして運用する形態です。カスタマイズの自由度は高いものの、初期導入コストや保守費用が大きいという課題があります。
-
クラウド型
インターネット経由でサービスを利用する形態です。初期コストが抑えられ、バージョンアップの手間も少ないメリットがあります。近年はクラウドベースのMRP対応生産管理システムも増えており、特に中小企業でも導入しやすい環境になっています。
-
AI/IoT連携、リアルタイム分析の普及
最新のシステムでは、IoTデバイスでリアルタイムに在庫数量や稼働状態を取得し、AIを用いて需要予測や最適発注タイミングを算出するといった取り組みが進んでいます。リアルタイムの情報更新が可能になり、変化の激しい現場にも柔軟に対応できるようになってきています。
MRPシステムの選び方
-
自社の生産形態を考慮する
多品種少量生産の場合と、少品種多量生産の場合では必要となる機能や操作性が異なります。また、受注生産(受注を受けてから生産開始)か、見込生産(需要予測に基づいてあらかじめ生産)かでもMRPの使い方は違ってきます。
-
生産方式(製番管理、ロット管理など)の対応状況をチェック
MTO(受注生産)やMTS(見込生産)、ETO(個別受注生産)など、自社が採用している生産方式にMRP機能が対応しているかを確認することが重要です。
-
コスト・導入期間・操作性・サポート体制
大規模システムになればなるほど導入期間やコストが膨らみがちです。自社に合ったスモールスタートができるか、導入支援や運用サポートがどの程度充実しているかも比較ポイントとなります。
主要なMRP対応システム例と特徴
- SAP S/4HANA グローバル大手のERPで、MRP機能も強力。大企業向けだが、中堅企業向けの導入支援も充実している。
- Oracle E-Business Suite / Oracle Fusion Cloud ERP こちらも包括的なERP。製造モジュールとしてMRP機能を持ち、サプライチェーン全体を俯瞰できる。
- Microsoft Dynamics 365 マイクロソフトのクラウド型ERP。オフィスソフトとの連携がスムーズで、導入ハードルが比較的低い。
- 国内ベンダーの生産管理システム 日系ベンダー(NEC、富士通、日立など)や中小企業向けのクラウドサービスも多数存在。日本の商慣習や製造現場の事情に合わせて設計されている点が強み。
このほかにも多数の生産管理システムが市場に出ています。ユーザーボイスとしては「BOMの精度が上がり、棚卸のたびに混乱していた状況が改善された」「購買担当とのやり取りが減り、生産管理業務が大幅に効率化できた」などの声があり、運用定着さえできれば大きな効果を得られることが多いようです。
6. 最新技術とMRP
MRPのための新しいテクノロジー
-
AI・機械学習を使った需要予測
変動が激しい昨今の市場で、過去データだけを頼りにした単純な需要予測では精度が限られます。そこでAIや機械学習モデルを活用して、多変量解析や時系列分析を高度化し、需要の振れ幅を予測しようという動きがあります。これにより、MRPでの所要量計算もより正確になりやすいと期待されています。
-
IoTでリアルタイム在庫管理
工場内でセンサーを使い、原材料の残量や仕掛品の数を自動計測する仕組みがあります。このリアルタイム在庫データをMRPにフィードバックすることで、もし途中工程で在庫が想定より減っていれば即座に追加発注を検討する、といったことが可能になります。
-
APS(生産スケジューラ)との連携
APSは、設備の稼働予定や工順を考慮して生産計画を組むシステムです。MRPが算出した材料手配情報を、APSが吸い上げて「どの設備で何時から生産し、いつ材料を使うか」を詳細にスケジュール化します。特に多品種・複雑工程の工場では、MRPとAPSの連携による最適化が注目されています。
今日のMRPと今後の展望
今や製造業ではDX(デジタルトランスフォーメーション)がキーワードとなっています。従来型のMRPは主に月次あるいは週次で回すことが多いですが、近年はリアルタイムで計画を更新できるシステムが求められています。デジタル技術を駆使してサプライチェーン全体をリアルタイムに把握し、需要変動や原材料の供給リスクにもすばやく対応できる動的なMRPが主流になりつつあります。
将来的には、サプライチェーン全体を一元管理するプラットフォームが標準化され、MRPがその中の一機能としてリアルタイムに稼働するようになる可能性があります。これによって生産管理だけでなく、販売や物流、さらには外部サプライヤーともシームレスに情報をやり取りしながら、最適なタイミングで必要な資材を調達する体制が確立していくでしょう。
7. MRPを運用する上でのポイント
MRP導入・運用の基本的な流れ
- 現状の生産・在庫管理方法の把握 まずは自社で今どのように資材を手配しているか、在庫管理の課題は何かを整理します。
- マスタデータや運用ルールの整備 BOM(部品表)を正確に作り、リードタイムや在庫基準を整備することが成功のカギです。
- システム導入と稼働テスト テスト導入の段階で実際の現場データを使い、MRP計算結果と実際の手配状況を比較して問題点を洗い出します。
- 関係部門との情報共有体制づくり 資材担当、購買担当、生産現場、営業・販売など、MRPに関わる部署がデータを共有しやすい環境を作ります。
- 運用後の定期的な見直し・改善 需要予測やBOM、リードタイムは固定ではありません。定期的に見直し、常に最新情報が反映されるようにします。
需要変動や計画変更への対応
近年では短納期化、品種の多様化、外部環境の変化などが激しく、計画通りにいかないことが増えています。MRPはあくまで計画であるため、実際の需要が変わればプログラムを再実行して再計画を立てる必要があります。これはシステム的には再計算ボタンを押すだけで済むケースが多いものの、現場の受け入れ態勢や購買先への連絡など、周辺のオペレーション整備が重要です。頻繁な変更が起こる時代だからこそ、情報をスピーディーに共有できる仕組みづくりやコミュニケーションが大切になります。
情報共有・データ品質の重要性
MRP運用では「現場側で在庫を勝手に動かしてしまい、システム上の在庫数量と乖離が生じる」「購買担当がシステムを通さずに手配を行ってしまう」といった問題が発生することがあります。
こうした運用上のギャップを埋めるには、システムへの入力ルールの徹底と、部門間の情報共有が欠かせません。MRPが正しく動くためには、入力されるデータが正確である必要があるからです。定期的に棚卸を行い、システム上の在庫と実在庫を照合するなど、品質管理を徹底していきましょう。
8. まとめ:自社の生産管理スタイルにあわせてMRPを検討しよう
次のステップ
MRPを導入しようと考える際は、まず自社の課題がどこにあるのかを明確にすることが大切です。在庫管理コストが大きすぎるのか、欠品リスクを抑えたいのか、あるいは生産指示や購買指示をもっと効率化したいのか。目的をはっきりさせることで導入プロジェクトの方向性が定まり、システム要件も決めやすくなります。
また、いきなりフル機能を導入するよりも、小さな範囲でテスト的に運用し、段階的に拡張するのもおすすめです。たとえば特定の製品群だけをMRP管理に切り替えてみたり、在庫管理の一部だけを対象にしたりと、スモールスタートで課題点を洗い出しながら全社展開につなげていく方法です。
まとめ
MRP(資材所要量計画)は、生産管理において「必要な資材を、必要なときに、必要な量だけ」用意するための代表的な仕組みです。正確な在庫情報やBOM、リードタイムなどのデータをもとに計画を立てるため、過剰在庫や欠品リスクを抑え、コスト削減と効率化を同時に実現することが可能です。
一方で、MRPは導入すればすぐに成果が出るわけではありません。BOMや在庫データなど、マスタ情報の整備が十分でないと計画精度が大きく損なわれますし、需要予測の精度が低ければ効果が出にくい側面があります。さらに、工場内部だけでなく、購買先や営業部門とも連携しないと計画と実態が乖離してしまいます。
しかし、こうした課題を乗り越えれば、MRPは製造業にとって非常に強力な武器となります。今後はAIやIoTを組み合わせた高度化が進むことで、リアルタイムに生産計画を最適化する時代がすぐそこまで来ています。競争力を高めるためにも、MRP単体の導入だけでなく、サプライチェーン全体を俯瞰しながら最適化を目指す時代になっていると言えるでしょう。
まずは自社の生産管理現場でどのようにMRPが使われているのか、あるいはまだ導入されていないのかを確認し、必要に応じて生産管理システムやERPベンダーへの相談、部分的なPoC(概念実証)を検討するなど、具体的な一歩を踏み出してみてはいかがでしょうか。そうすることで、在庫コストの大幅削減や生産リードタイム短縮など、MRPの恩恵を体感できるようになるはずです。
以上、MRPの基本から導入メリット、システム連携、今後の展望までを紹介しました。MRPについて理解を深め、競争力ある生産体制を築くためのヒントとして、ぜひ本記事を参考にしていただければ幸いです。
MRPだけでは見えない現場のズレは『最適ワークス』の生産計画DXでカバー
生産管理の起点となるのが「生産計画」です。DX(デジタルトランスフォーメーション)を始めるなら、まずはこの生産計画から取り組むことをおすすめします。
「生産スケジューラの導入費用をもっと抑えたい」「できるだけ早く導入したい」「導入後にきちんと使いこなせるか不安」といったお悩みをお持ちの方には、「最適ワークス」の導入をぜひご検討ください。最適ワークスの魅力は、コストパフォーマンスの高さ、迅速な導入、使いやすいシンプルな画面UI、そして充実したサポート体制にあります。月額15万円という手頃な価格で、AIによる高度な最適化ソリューションをご利用いただけるのは、大きなメリットです。
また、クラウドサービス(SaaS)で提供されているため、初期のハードウェア投資や複雑なシステム構築は不要です。そのため、導入スピードも非常に速く、時間とリソースを節約しながら、迅速に業務改善を始められます。シンプルで直感的な画面UIにより、特別なIT知識がなくても誰でも簡単に操作できます。また、カスタマーサクセスチームが導入後もユーザーに寄り添いながら支援し、最適ワークスを最大限に活用していただけるようサポートします。低コストでありながら高機能、そしてサポートも充実している最適ワークスは、DXや業務改善の第一歩として最適なサービスです。。
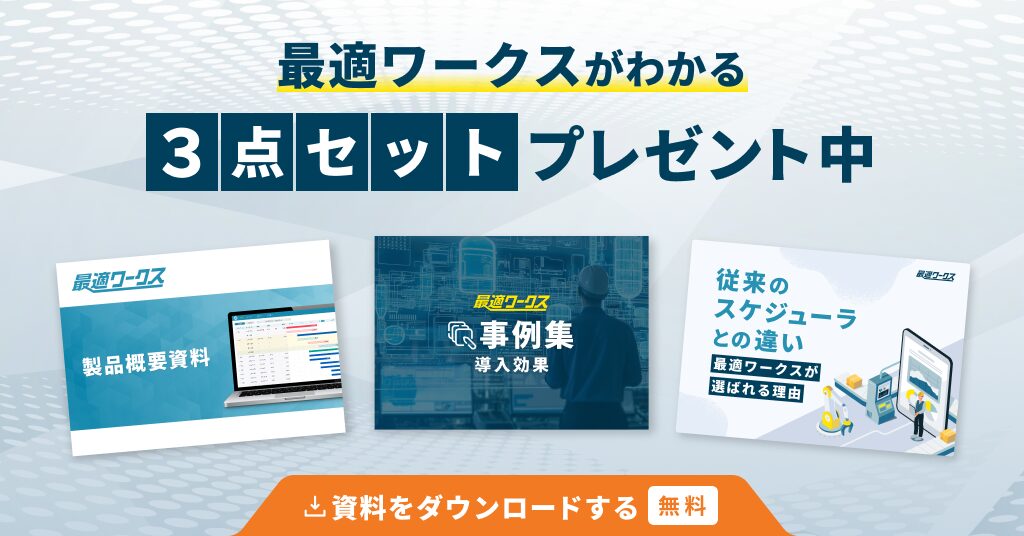