- コラム
APS(生産スケジューリング)とは?導入メリットから活用事例まで徹底解説 – 生産計画最適化で工場を進化
近年の製造業を取り巻く環境は厳しさを増し、多品種少量生産への対応は必須となり、市場のニーズは多様化の一途を辿っています。さらに、需要変動も激しく、「急ぎの注文が入った」「納期が突然早まった」といった事態が日常的に発生し、製造現場は常に納期遵守と効率化の間で板挟みになっています。
このような状況下で、生産管理担当者は、製造ラインの稼働率向上、納期遵守、在庫削減という3つの至上命題を同時に達成しなければならず、その苦労は計り知れません。
しかし、現実の生産現場では、工程間の連携ミス、段取り替えの遅延、設備負荷の偏りなど、様々な問題が複雑に絡み合っています。特に、「計画と実際のギャップ」は深刻です。紙やExcelで作成した計画は、現場の状況変化に即応できず、計画倒れになることが常態化。結果として、リードタイムは長期化し、納期遅延、顧客からの信頼低下、さらには収益悪化といった負のスパイラルに陥ってしまうのです。
このような状況を打破し、製造業の生産管理を革新するために、近年注目を集めているのがAPS(Advanced Planning and Scheduling)、日本語で「生産計画スケジューリング」または「生産スケジューラ」と呼ばれるシステムです。
従来のMRP(資材所要量計画)などの生産管理システムとは異なり、APSは複雑化した生産環境において、高度なスケジューリングを可能にします。短納期対応、多頻度小ロット生産、サプライチェーン全体最適化といった現代の製造業が抱える課題に対し、APSは有効なソリューションとなりえます。
この記事では、APSの基本概念、従来手法との違い、導入メリット、活用ポイントに加え、具体的な導入事例を交えながら、APSが製造業の現場をどのように変革できるのかを詳しく解説していきます。
APS(Advanced Planning and Scheduling)とは
まずはAPSの定義から確認しておきましょう。APSとは「Advanced Planning and Scheduling(生産計画スケジューリング)」の略称であり、生産計画立案と生産スケジューリングを高いレベルで同期させ、最適な生産計画を迅速に立案できる仕組みを指します。一般的には「生産スケジューラ」と呼ばれることもあります。
たとえば従来のMRP(資材所要量計画)は「いつまでに、どの材料を、どれだけ手配すればよいか」を逆算して算出する仕組みですが、実際の現場では設備の負荷状況や人員の有無、段取り替えのタイミングなど、多くの要素によって生産効率が左右されます。MRPはそうした“作業現場の制約”を考慮するのが苦手で、結果として手配の漏れやムダ在庫が発生しやすかったり、また実際の生産スケジュールに落とし込む段階でExcelに頼って手作業で調整する、といったケースがよく見られます。
一方APSでは、生産現場に存在するさまざまな制約条件を同時に加味しながら、最適なスケジュールを作成することが可能です。受注数量、納期要求、人員の配置、設備の負荷、段取り工数、仕掛在庫の数量など――あらゆる情報を入力し、コンピュータが高速に計算を行うことで、最適化された生産計画が立案できるのです。また、スケジュールを立案した後も状況の変化があれば即座に再計算し、常に最新の最適スケジュールを維持することができます。このスピーディな再スケジューリング機能こそが、APSの最大の特長だと言えるでしょう。
APSが生まれた背景
ではなぜAPSという考え方が生まれ、ここまで注目を集めるようになったのでしょうか。背景には大きく分けて次の3つの要因があります。
-
市場環境の変化・複雑化
消費者のニーズが細分化し、多品種少量生産やカスタマイズ製品の需要が高まっています。さらに、グローバル化によって国際的なサプライチェーンが形成され、調達先や生産拠点が多岐にわたるようになりました。結果として、生産現場が扱う情報量や制約条件が飛躍的に増加し、従来の手作業や簡易的なシステムだけでは管理しきれなくなったのです。
-
IT技術の進化
計算機リソースが格段に向上し、大規模な制約条件を高速に計算するアルゴリズムが実用的になりました。また、IoTの発達によって、生産現場の進捗情報や設備稼働状況をリアルタイムに取得しやすくなったことも大きな後押しです。これにより「理論上は最適化できるが、計算に時間がかかりすぎて実用的でない」という問題が徐々に解消されつつあります。
-
短納期化と需要変動への即時対応
インターネット通販の普及や納期に対する顧客要求の高まりにより、少しでもリードタイムを短縮し、受注変動にも柔軟に対応できる生産体制が求められています。現実の工場では、突然の注文変更が発生しても即座にスケジュールを組み直し、人的・設備的リソースを再調整しなければなりません。従来の手法では膨大な時間がかかっていた再調整作業を、APSは自動かつ高速に行うことができます。
こうした要因が重なり合って、「高度なスケジューリング機能」を備えたソリューション。すなわちAPSへの注目が一気に高まってきたのです。
APS導入メリットと導入効果
APSを導入すると、具体的にどのような効果が得られるのでしょうか。ここでは主なメリットを3つに分けて紹介します。
生産計画の最適化
APSの最大の特徴は、大量の制約や需要情報を同時に考慮しながら、最適な生産計画を素早く作成できる点にあります。これにより以下のような成果が期待できます。
-
リードタイムの短縮
生産順序や段取り替えの最適化によって、実質的な生産時間が圧縮されます。計画変更があった場合でも、APSが即座に再計算を行うため、全体としての無駄な待機時間が減り、結果としてリードタイムを短縮できます。
-
在庫削減
必要な材料や部品の量が明確になるため、過剰な在庫を抱えるリスクが低減します。MRPの結果だけを頼りにすると「念のため、余分に発注しておこう」という心理が働きがちですが、APSでは実際の製造スケジュールに即して部品を手配するため、より正確な在庫管理が可能となります。
-
段取り回数の削減
生産順序の組み方次第で段取り替えの回数が増減します。段取り時間を最小化するようにAPSが自動でスケジュールを組めば、設備切り替えによる損失時間を大幅に削減できるでしょう。
リソース管理の効率化
APSによるスケジュール作成のもう一つの強みは、工場全体のリソース(ヒト・設備)の稼働状況を可視化し、ボトルネックを明らかにすることです。
-
ヒトや設備の稼働率向上
無駄な待ち時間や、特定の工程での詰まり(ボトルネック)を解消できれば、全体としての稼働率が向上します。作業者のシフトや休憩時間を考慮する設定もできるため、実運用に近いスケジュールを作成できます。
-
ボトルネックの可視化
「どの工程が一番のネックになっていて、他の工程はどれほど稼働余裕があるのか」を客観的に把握しやすくなります。これによって、どの工程に先行投資をすべきか、どの設備の追加導入が効果的かなど、現場改善のヒントを得ることができます。
納期管理の改善
最後に、製造業の肝である納期管理です。APSではガントチャートなどの視覚的なツールを用いて、計画と実績の差異をリアルタイムで監視できます。
-
ガントチャートによる進捗管理
どの製品がいつ着手され、いつ完了するかが一目瞭然になります。遅延が発生しそうな場合は早期にアラートを出したり、代替ルートの検討が容易になります。
-
コストと納期の両立
納期優先なのか、コスト優先なのか、あるいはバランスをどうとるのかといった方針を設定し、それに合わせたスケジュールを自動で組むこともできます。たとえば「急ぎの大口受注が入ったので、多少コストがかかっても先にそれを生産する」といった調整がスムーズに行えます。
-
根拠に基づいたスピーディな納期回答
製造キャパを考慮した納期のシミュレーションをスピーディに実施することで急なオーダーにも自信をもって納期回答できます。
生産計画とスケジューリングの違い
製造業における「計画」と「スケジュール」はしばしば混同されますが、実際にはそれぞれ明確に違いがあります。大まかにいうと、
- 生産計画 「何をいつまでに、いくつ作るか」を決める大枠の計画(需要予測や在庫目標などを踏まえて決定される上位レベルの計画)
- 生産スケジューリング 「決めた生産計画を、どの設備で、どの順序で、どのタイミングで作るか」を細かく落とし込む実行計画(工程表)
このように、生産計画は上位レベルのプラン、スケジュールはより細部に踏み込んだ実行計画ともいえます。それぞれをもう少し詳しく見てみましょう。
生産計画と負荷計画
生産計画を立てる際には、通常、需要予測や在庫基準、販売計画などを参照しながら「月間何個、週間何個を作るか」といった大枠のプランを策定します。その上で、各設備やラインに対して「これだけ作ればこれだけの負荷がかかる」という負荷計画を行い、リソースが不足しないかをチェックします。
しかし、いくら負荷計画で余裕があると判定されたとしても、現実には設備の段取り時間や運搬時間が発生し、作業者ごとのスキル差や休憩時間も考慮しなければなりません。負荷計画はあくまで概算の指標に過ぎず、日々の実際の生産スケジュールを管理するには不十分なのです。
MRPと生産スケジュール
MRP(Material Requirements Planning)は、どの製品を作るために、いつまでに、どの部品がどれだけ必要かを割り出し、部品や資材を手配する仕組みです。生産計画で「今月はこの製品を1,000個作ろう」と決まれば、その1,000個の生産に必要な部品Aはいつまでに何個、部品Bは何個…といったように展開していきます。
ただし、MRP単体では「人員の空き状況」や「設備の具体的スケジュール」までは考慮しません。そのため、MRPの結果だけでは、実際にどの順序で生産し、どのタイミングで部品を使うかは不透明です。ここで必要になるのが生産スケジューリングであり、APSはまさにこのスケジューリングを高度に行うためのシステムなのです。
APSを活用するためのポイント
APSを導入すればすべてが自動的にうまくいくわけではありません。現場でAPSを有効に活用するためには、いくつかの重要なポイントがあります。
-
実績に基づきデータを磨き込む
APSは多くのデータをもとに計算を行います。各工程の生産能力、段取り時間、作業者スキルなど、入力するデータが不正確だと、どんなに高度な計算を行っても机上の空論に終わってしまいます。登録したデータの正確性を磨くためには計画と実績の対比によるデータのメンテナンスが不可欠です。
-
シミュレーションの活用
APSには、「もしこの注文を優先したら、他の生産にどれほどの影響が出るか」「残業を増やしたら納期に間に合うか」といったシミュレーションが可能なものが多いです。複数のシナリオを即座に試し、その結果を比較検証できるため、意思決定がスピーディになります。ただし、シミュレーションの前提となるデータやパラメータが古いままだと結果が正しくないので注意が必要です。
-
見える化と現場との共有
APSが算出したスケジュールはガントチャートなどで可視化されることが多いですが、これを現場作業者と共有し、相互コミュニケーションを図ることも非常に重要です。「計画で立案された段取り時間は○分だが、実際にはもっとかかる」「休憩時間や交代要員の都合を考慮してほしい」といった声を吸い上げ、データを更新していくサイクルを回すことが、APS導入成功のカギとなります。
生産資源の見える化
APSを導入すると、設備ごとの稼働スケジュールや作業者の配置状況が明確に可視化されます。これにより、これまで見過ごされていた無駄な時間や手待ち時間が浮き彫りになるでしょう。同時に、全工程を俯瞰して最適化を図る「全体最適」の視点が得られます。
たとえば、「この工程は設備Aがフル稼働で手一杯だが、設備Bは余裕がある。だったら工程全体の流れを変えて、Bを活用しよう」といった判断も、APSのデータを見ながらスピーディに行えるわけです。ただし、そのためには各設備の制約条件(加工可能な品目やスキルセットなど)を登録しておく必要がある点は要注意です。
生産スケジューラ機能を備えた生産計画DXソリューション「最適ワークス」
APSや生産スケジューラにはさまざまな製品やソリューションがありますが、その中でも近年注目を集めているのが**「最適ワークス」**です。これは生産計画の自動化を目指すDX(デジタルトランスフォーメーション)ソリューションであり、以下のような特長を備えています。
- 使いやすく導入しやすい直感的な操作性、分かりやすい画面構成。低コストであり、短期間での導入が可能です。
- AIが複雑な生産計画をスピーディに立案受注データ、設備負荷、段取り時間などをもとに、AIが最短リードタイムでの生産スケジュールを自動算出。短納期オーダーにも迅速に対応が可能です。
- ガントチャートによる可視化スケジュール結果はガントチャートで直観的に把握できます。任意の工程をクリックすれば必要な情報を確認できるなど、使い勝手にも配慮されています。
- 自動リスケジューリングによる計画変更突発的なトラブル等も、計画担当者の指示に基づき生産計画をリスケできるため、計画担当者の負担を大幅に軽減します。
- クラウド対応クラウドベースで稼働するため、システム導入コストが抑えられます。
「最適ワークス」をはじめとする先進的な生産計画ソリューションを取り入れることで、工場全体の生産効率を劇的に高め、短納期対応力を強化することが期待できます。
最適ワークスの導入による成功事例
岐阜県のスザキ工業所は岐阜県の自動車部品メーカーとして、金属プレス、溶接、組立加工に40年以上の実績を持っています。近年では多角化を進め、自動車業界以外にも事業を展開。取引先の拡大により、製造品目が多様化。その結果、現場管理が複雑になり、従来は生産計画を立案するために生産管理担当が効率的な計画を毎日4時間残業して組んでいました。
かんばん方式での限界を感じ、2023年3月より最適ワークス(APS)を導入し、生産管理体制を強化した結果、計画立案のための残業はゼロに。効率的な生産計画の立案により生産数量が10%増加、納期遵守率が20%改善、残業時間の20%削減を実現しました。
導入のポイント
スザキ工業所の事例から、最適ワークス(APS )導入を成功 させるための2つのポイントを学ぶことができます。
-
スモールスタート
APS 導入時に最も手間がかかるのはマスターデータの整備です。工程にどれくらいの時間が必要かといった情報を完璧に整理してからマスターを登録しようとすると、いつまで経っても運用を開始できません
スザキ工業所では、最初から完璧を目指さず、オーダーが入る都度「パンチ数が〇〇回だから〇時間」程度の精度でデータを登録し、運用しながら現場の実績と照らし合わせてデータをブラッシュアップ していく方法を採用しました。
3ヶ月で約400品目のマスターを登録し、スモールスタートで着実に効果を上げています。
-
予実比較による改善活動
APSでは計画がデータ化されています。スザキ工業所では従来紙で生産計画を立案していましたが、例えば紙の生産計画は視認性が悪く、膨大な実績から計画との差異を振りかえることはとても困難です。
APSの導入により計画と実績がデータ化され、例えば生産全般の遅れが発生したときに、それが特急オーダーなど差し込み業務の影響なのかが分かるようになる等、遅れの原因を知ることで効果的な対策が打てるようになり、業務改善に結びつけることが容易になりました。
データに基づくPDCAサイクルを回すことで、継続的な改善を実現し、効果を最大化することが可能になります。
まとめ:生産スケジューラとAPSについて
最後に、本記事の要点を振り返りましょう。
-
APS(Advanced Planning and Scheduling)とは?
生産計画とスケジューリングを高度に連携させるシステムであり、従来のMRPなどでは考慮しづらかった複雑な制約をもとに最適化を行う。
-
APSが注目される背景
多品種少量生産や短納期対応の重要性が増し、製造現場が扱う情報量が爆発的に増加した。さらにIT技術が進化し、大規模な最適化計算が現実的に可能になった。
-
導入メリット
- リードタイム短縮、在庫削減、段取り削減などの生産計画の最適化
- 設備や人員の稼働率向上、ボトルネックの解消などのリソース管理の効率化
- ガントチャートによる進捗管理、納期遵守率向上などの納期管理改善
-
生産計画とスケジューリングの違い
大枠の計画(何をいつまでにどれだけ作るか)と、現場レベルでの割り当て(どの設備でどの順序で作るか)は区別されるべき。APSは後者のスケジューリングを高精度で自動化できる。
-
活用のポイント
- データの正確性を確保
- シミュレーション機能を活用
- 見える化と現場とのコミュニケーションが重要
-
具体的なシステム例
「最適ワークス」などのクラウド対応ソリューションでは、高速な最適化機能を備え、既存システムとの連携もしやすい。
-
導入事例と成功の秘訣
スモールスタートと、データに基づく改善活動が業績改善にとって重要
APSの導入は、単なるシステム刷新にとどまらず、生産管理プロセス全体の改革(DX)につながります。競争が激化し、市場の変化スピードが加速している今だからこそ、APSを活用した“最適な生産管理体制”を構築する意義はますます大きくなっています。もし「受注変動に追われてスケジュールが毎日ひっ迫している」「在庫を減らしたいが、どこから手を付ければいいかわからない」といった悩みをお持ちであれば、まずはAPSの検討を始めてみるのはいかがでしょうか。
本記事がAPSについての理解を深めるきっかけになり、読者の皆様の生産管理における一助となれば幸いです。短納期対応や在庫最適化、コスト削減のプレッシャーに立ち向かうためにも、ぜひAPSを活用し、現場と計画を高い次元で融合させる生産管理の未来を切り拓いていきましょう。
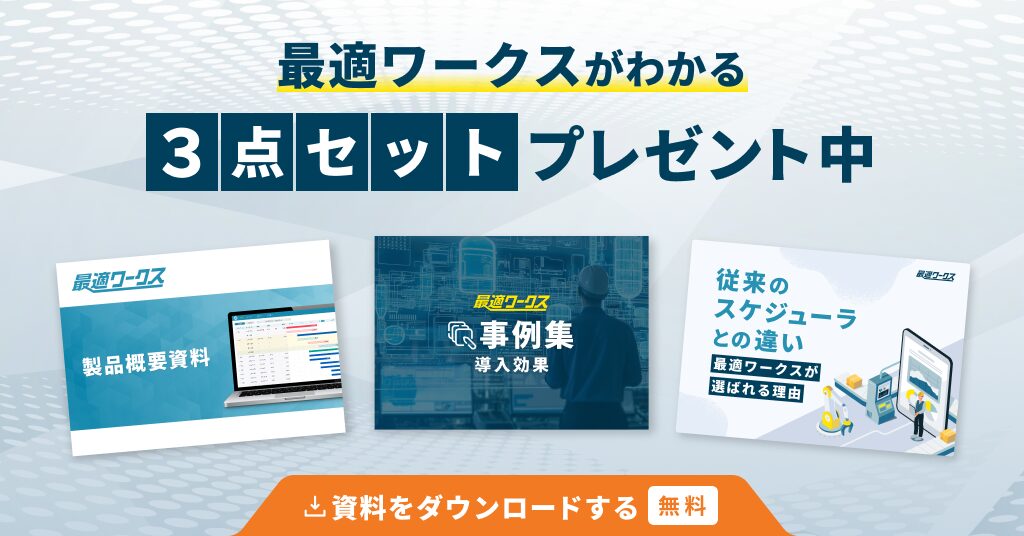