- コラム
中小製造業の利益を最大化する!原価管理のすべて:基本からDX活用まで徹底解説
なぜ原価管理が中小製造業にとって重要なのか
中小製造業を取り巻く環境は、常に変化しています。原材料費の高騰、人手不足、そして競争の激化など、多くの課題が山積しています。このような状況下で、企業が持続的に成長し、利益を確保していくためには、原価管理が欠かせません。
原価管理とは、製品やサービスを生み出すためにかかるコストを把握し、管理・分析する活動全般を指します。単にコストを下げるだけでなく、「どこに、どれだけのコストがかかっているのか」を正確に理解し、無駄を省き、効率的な生産体制を構築するための羅針盤となるのです。
この記事では、原価管理の基本概念から具体的な手法、そして成功事例まで、中小製造業の皆様が明日から実践できる情報を分かりやすく解説していきます。
原価管理とは?その定義と重要性を理解しよう
原価管理とは、「製品の製造に関わる原価を適切に管理し、利益改善を図る活動」です。具体的には製品やサービスを製造・提供する際にかかるコスト(原価)を、計画・把握・分析・改善する一連の活動のことです。
もう少し詳しく言うと、
- 計画段階: 製品を作るために、どれくらいの費用がかかるかを見積もります。
- 実行段階: 実際に製品を作り、どれくらいの費用がかかったかを記録します。
- 分析段階: 計画と実績を比較し、なぜ差が出たのかを分析します。
- 改善段階: 分析結果をもとに、原価を下げるための対策を立て、実行します。
このように、原価管理は単にコストを記録するだけでなく、継続的に改善していくための活動全体を指します。
なぜ原価管理が重要なのでしょうか?それは、企業の利益に直接影響するからです。原価を把握し、無駄をなくすことで、利益を増やすことができます。また、価格設定の根拠となり、競争力を高めることにも繋がります。
原価管理の目的:利益の源泉を明らかにする
原価管理の主な目的は以下の通りです。
- 利益率の改善: 製品の売上から原価を差し引いたものが利益です。原価を抑えることで、同じ売上でも利益を増やすことができます。
- コストの削減: 無駄なコストを洗い出し、削減することで、利益を改善します。例えば、材料の無駄を減らしたり、作業効率を上げたりすることで、コストを削減できます。
- 経営判断の迅速化: 原価情報をもとに、迅速かつ正確な経営判断を行うことができます。例えば、どの製品が利益率が高いのか、どの工程に問題があるのかなどを把握することで、適切な対策を講じることができます。
- 競争力の強化: 正確な原価情報に基づいて適切な価格設定をすることで、競争力を高めることができます。また、コスト削減によって、より安く高品質な製品を提供できるようになります。
適切な原価管理を行うことで、製品の価格設定を適切に行い、利益を確保することができます。また、無駄な支出を削減し、企業の成長に貢献することも可能となります。
原価の種類と役割:製造原価、標準原価、実際原価
原価には様々な種類があります。ここでは、中小製造業で特に重要な3つの原価について解説します。
製造原価: 製品を製造するためにかかる費用全般を指します。
- 直接材料費: 製品の材料となる費用(例:金属、樹脂、電子部品など)
- 直接労務費: 製品の製造に直接関わる人の人件費(例:製造ライン作業者、機械オペレーターなど)
- 製造間接費: 製品の製造に間接的に関わる費用(例:工場賃料、機械の減価償却費、間接部門の人件費など)
製造原価は、製品のコストを把握する上で最も基本となる原価です。
標準原価:製品1個あたりの理想的な原価です。過去のデータや技術的な知見に基づいて設定されます。
- 標準原価は、予算編成や原価管理の基準として使われます。
- 実際の原価と標準原価を比較することで、無駄や改善点を見つけることができます。
実際原価: 実際に製品を製造した際にかかった原価です。
- 実際原価は、日々の生産活動を記録することで計算されます。
- 実際原価と標準原価を比較することで、コスト管理の状況を把握できます。
見積原価:製品を製造する前に、どれくらいの費用がかかるかを見積もった原価です。
標準原価と似ていますが、見積原価はより柔軟に、状況に応じて変化する可能性のある費用も考慮に入れるのが特徴です。例えば、新しい製品を開発する際や、特別な注文を受けた場合などに、見積原価が使われます。
見積原価の計算には、過去のデータや経験だけでなく、市場の状況や技術的な進歩なども考慮に入れる必要があります。これにより、より現実的な価格設定や、効率的な生産計画を立てることが可能になります。
これらの原価を適切に使い分けることで、より効果的な原価管理を行うことができます。
中小製造業における原価管理の課題:見過ごせない現実
中小製造業における原価管理には、以下のような課題がよく見られます。
- 属人化: 特定の担当者しか原価の計算方法や管理方法を把握していないため、担当者が不在になった場合に業務が滞ってしまう。
- データ管理の煩雑さ: エクセルなどの表計算ソフトで原価計算を行っている場合、データの入力や集計に手間がかかり、ミスも発生しやすい。
- リアルタイムな把握の難しさ: 原価情報がリアルタイムに把握できないため、迅速な意思決定が難しく、問題が発生してから気づくことが多い。
- 標準原価の設定が難しい: 多品種少量生産の場合、標準原価の設定が難しく、実際原価との乖離が大きくなりやすい。
- システム導入のコスト: 原価管理システムを導入したいが、コストが高く、導入に踏み切れない。
これらの課題を解決するためには、業務の標準化、データ管理の効率化、そして適切なシステム導入が不可欠です。
原価管理のメリット・重要性:企業成長のエンジン
原価管理をしっかりと行うことには、多くのメリットがあります。
- 利益率の向上: 無駄なコストを削減し、効率的な生産体制を構築することで、利益率を向上させることができます。
- 価格競争力の強化: 正確な原価情報に基づいて適切な価格設定を行うことで、競争力を高めることができます。
- 経営判断の迅速化: リアルタイムな原価情報を把握することで、迅速かつ的確な経営判断を行うことができます。
- 問題点の早期発見: 原価差異を分析することで、問題点を早期に発見し、改善することができます。
- 従業員のコスト意識向上: 原価管理に関わることで、従業員のコスト意識が向上し、改善活動が活発になります。
- 顧客満足度の向上: 高品質な製品をより安く提供できるようになり、顧客満足度が向上します。
このように、原価管理は単にコストを下げるだけでなく、企業の成長を支える重要な要素なのです。
原価管理の具体的な方法:PDCAサイクルで改善を繰り返す
原価管理は、一度行ったら終わりではありません。継続的に改善していくことが重要です。ここでは、PDCAサイクルに沿って、具体的な原価管理の方法を解説します。
- Plan(計画):
- 目標設定: 具体的な原価削減目標を設定します。例えば、「来年度は製造原価を5%削減する」といった目標を立てます。
- 標準原価の設定: 過去のデータや技術的な知見に基づいて、標準原価を設定します。
- 予算編成: 原価削減目標を達成するための予算を編成します。
- Do(実行):
- 製造記録: 実際に製品を製造する際にかかった費用(直接材料費、直接労務費、製造間接費)を正確に記録します。
- 進捗管理: 生産計画に基づき、進捗状況を管理します。遅延や問題が発生した場合は、すぐに対応します。
- Check(評価):
- 実際原価の算出: 記録したデータを基に、実際原価を算出します。
- 原価差異の分析: 標準原価と実際原価を比較し、なぜ差が生じたのかを分析します。
- ボトルネックの特定: 原価が高くなっている原因(ボトルネック)を特定します。
- Action(改善):
- 改善策の立案: ボトルネックを解消するための改善策を立案します。例えば、「材料の調達先を見直す」「作業手順を改善する」といった対策を考えます。
- 改善策の実行: 立案した改善策を実行します。
- 効果測定: 改善策の効果を測定し、目標達成度を評価します。
- 見直し: 効果が不十分な場合は、さらに改善策を見直し、PDCAサイクルを回します。
このPDCAサイクルを繰り返すことで、原価を継続的に改善し、より効率的な生産体制を構築することができます。
原価管理の課題:成功への障壁を乗り越える
原価管理は重要ですが、必ずしもスムーズに進むとは限りません。よくある課題として、以下のようなものが挙げられます。
- 情報の不足: 正確な原価情報を収集するための仕組みが整っていない。
- 分析スキル不足: 収集した情報を分析し、改善につなげるためのスキルが不足している。
- 経営層の理解不足: 原価管理の重要性を経営層が理解していないため、改善活動が進まない。
- 現場の協力不足: 現場の従業員が原価管理の重要性を理解しておらず、非協力的な場合がある。
これらの課題を解決するためには、
- 情報収集体制の整備: 正確な原価情報を収集するためのシステムを導入し、運用体制を構築する。
- 教育・研修の実施: 従業員向けの原価管理に関する教育・研修を実施し、分析スキルを高める。
- 経営層への働きかけ: 経営層に原価管理の重要性を理解してもらい、協力を得る。
- 現場とのコミュニケーション: 現場の従業員とコミュニケーションを取り、原価管理への理解を深めてもらう。
これらの対策を講じることで、原価管理を成功に導くことができます。
生産計画と原価管理の関係と重要性について
なぜ、生産計画と原価管理が重要なのか?
中小製造業において、生産計画と原価管理は、それぞれが単独で重要なだけでなく、互いに密接に連携することで、より大きな効果を発揮します。
- 生産計画: 顧客の需要に基づいて、何を、いつ、どれだけ生産するかを決定する活動であり、効率的な生産体制の基盤となります。
- 原価管理: 製品やサービスを生み出すためにかかるコストを把握し、無駄を省き、効率化を図る活動であり、利益率の向上に不可欠です。
この2つが連携することで、以下のようなメリットが生まれます。
- 無駄の排除: 生産計画に基づき、過剰な生産や過剰な在庫を抑制し、原材料費、保管費、陳腐化による損失などの無駄を排除します。
- コスト削減: 納期遅延による残業代や、緊急輸送費、非効率な人員配置など、生産計画が最適化されていない場合に発生する様々なコストを削減します。
- 利益最大化: 原価を正確に把握し、適切な販売価格を設定することで、利益を最大化できます。
- 生産性の向上: 生産計画に基づき、設備稼働率を向上させ、スムーズな生産体制を構築し、生産性を向上させます。
- 経営判断の迅速化: 生産計画と原価管理の両方のデータに基づき、経営者はより正確かつ迅速な意思決定を行うことができます。
- 顧客満足度の向上: 納期を守り、高品質な製品を安定して提供することで、顧客満足度を高めることができます。
生産計画が原価に与える影響
- 過剰在庫: 不正確な需要予測や、非効率な生産計画は、過剰な在庫を生み出し、保管費や陳腐化のリスクを高めます。
- 納期遅延: 不良品の発生や、工程の遅延は、納期遅延を招き、緊急輸送費や機会損失を生じさせます。
- 非効率な生産: 設備の稼働率が低下したり、人員配置が適切でないと、生産効率が低下し、人件費や設備減価償却費といった固定費が増加します。
- 仕掛品の滞留: 工程間の連携がうまくいかないと、仕掛品が滞留し、無駄な在庫コストが発生します。
原価管理が生産計画に与える影響
- ボトルネックの特定: 原価管理によって、どの工程に無駄があるのか、効率が悪いのかを特定できます。
- 標準時間の見直し: 各工程にかかる時間を把握することで、より正確な生産計画を立てることが可能です。
- 意思決定のサポート: 原価データは、どの製品を優先的に生産すべきか、どの設備を増強すべきかといった、生産計画に関する意思決定をサポートします。
- 改善活動の促進: 原価データに基づいて、生産計画の改善活動を促すことができます。
生産計画と原価管理は、企業の利益を最大化するために、互いに連携しながら最適化を図る必要があり、片方だけを改善しても、もう片方が非効率な状態では、十分な効果は得られません。
この関係性を理解した上で、DXツールを導入することで、生産計画と原価管理を同時に最適化し、より大きな効果を期待できます
DXツール活用で原価管理の課題を解決する方法
中小製造業の原価管理の課題を解決する上で、DX(デジタルトランスフォーメーション)ツールの活用は非常に有効です。ここでは、具体的な事例と併せて、DXツールの活用方法を紹介します。
生産計画DXソリューション「最適ワークス」による原価削減成功事例
上記記事で紹介されているように、最適ワークスは生産計画のDX化により中小製造業の課題解決を支援しています。最適ワークスの活用により以下のような効果が期待できます。
生産計画の精度向上による製造効率の改善と原材料費の削減
AIを活用した生産計画の立案により、製造プロセスの最適化が可能となります。これにより、製造量が増加し、製品あたりの固定原価が減少します。従来の経験則に頼った計画立案から脱却し、数理最適化AIが効率的な計画を立案することで、生産性の向上が期待できます。
計画的な生産と現場の効率化により、生産能力が10%向上。生産計画の精度向上により、不良品発生が減った結果、原材料の無駄な使用が抑えられm原材料比率が2%削減された事例も出てきています。
ムリ・ムダのない計画による残業時間の削減
AIが感情や期待に左右されない客観的な計画を立案することで、作業の遅延や計画の破綻を防ぎます。これにより、無駄な残業が削減され、人件費の圧縮につながります。計画のムリ・ムダ・ムラを排除することで、効率的な生産活動が可能となります。製造順序が整理され、それぞれの作業の見通しが立つことで無駄な残業が削減され、20%以上残業がなくなった、という事例も出てきています。
計画的な休暇取得の促進
生産計画の可視化により、繁忙度合いを把握できるため、スタッフの計画的な有給休暇取得が可能となります。これにより、従業員のモチベーション維持や働き方改革にも寄与します。
その他のDXツール
- クラウド型ERP: 生産管理、販売管理、会計管理などの業務を一元的に管理できる。
- BIツール: データを可視化し、分析を支援する。
- IoTセンサー: 機械の稼働状況や生産量をリアルタイムで把握する。
- RPA: 定型的な業務を自動化する。
これらのDXツールを組み合わせることで、より高度な原価管理を実現できます。
まとめ:原価管理を「攻め」の経営戦略へ!中小製造業の未来を切り拓く
中小製造業を取り巻く環境は厳しさを増していますが、原価管理は単なるコスト削減の手段ではありません。 この記事で解説したように、原価を正確に把握し、効率的な生産体制を構築することは、利益を最大化し、競争優位性を確立するための「攻め」の経営戦略そのものです。
改めて、重要なポイントを振り返りましょう。
- 原価管理は、コストを「守る」だけでなく、利益を「創出する」ための羅針盤となる。
- 正確な原価把握は、価格戦略の基盤となり、競争力を高める。
- PDCAサイクルを回し続けることで、持続的な改善が可能になる。
- DXツールは、原価管理の課題を解決し、変革を加速させる強力な武器。
- 生産計画と原価管理を連携させることで、企業全体の最適化を目指すことができる。
中小製造業の皆様にとって、原価管理は決して簡単な取り組みではありません。しかし、変化を恐れず、積極的にDXツールを活用し、データに基づいた意思決定を行うことで、必ず成果は出ます。
この記事が、皆様の原価管理の取り組みを始めるきっかけとなり、未来を切り拓く一助となれば幸いです。
今こそ原価管理を「攻め」の戦略として捉え、御社の持続的な成長を実現しましょう!
まとめ
在庫管理は、製造業にとって非常に重要な業務であり、企業の競争力を左右する重要な要素です。属人化、情報の分断、需要予測の難しさなど、多くの課題を抱えている企業も少なくありません。
これらの課題を解決するためには、基本的な在庫管理方法を実践するだけでなく、デジタルツールの導入、特に生産計画と連携した在庫管理を行うことが重要です。
「最適ワークス」のような生産計画自動立案SaaSは、貴社の生産計画と在庫管理を最適化し、業務効率の向上、コスト削減、競争力強化に貢献します。
在庫管理の課題でお悩みの企業様は、ぜひ一度お問い合わせください。
生産管理でDXを始めるなら生産スケジューラ「最適ワークス」がおすすめ
生産管理で起点となるのが生産計画です。DXを始めるならまずは生産計画から始めることがおすすめです。生産スケジューラの導入費用をもっと抑えたい、可能な限り早く導入したい、導入後に使いこなせるか不安、といったご不安がある方は、「最適ワークス」も是非ご検討ください。最適ワークスの魅力は、そのコストパフォーマンス、迅速な導入、使いやすいシンプルな画面UI、手厚いサポート体制です。月額15万円という手頃な価格で、AIによる高度な最適化ソリューションを利用できるのは大きなメリットです。クラウドサービス(Saas)であるため、初期のハードウェア投資や複雑なシステム構築が不要で、導入スピードも非常に速いです。これにより、時間とリソースを節約し、迅速に業務改善を開始できます。
シンプルで直感的な画面UIは、特別な技術知識がなくても誰でも簡単に操作でき、誰でもスムーズに利用できます。また、カスタマーサクセスチームがユーザーと伴走し、最適ワークスを最大限に活用できるようサポートします。導入後も手厚いサービスを提供し、ビジネスの課題解決に直結した支援を行います。
低コストでありながら高機能、そしてサポート体制も充実しているため、DXや業務改善の第一歩として優れたサービスとなっています。
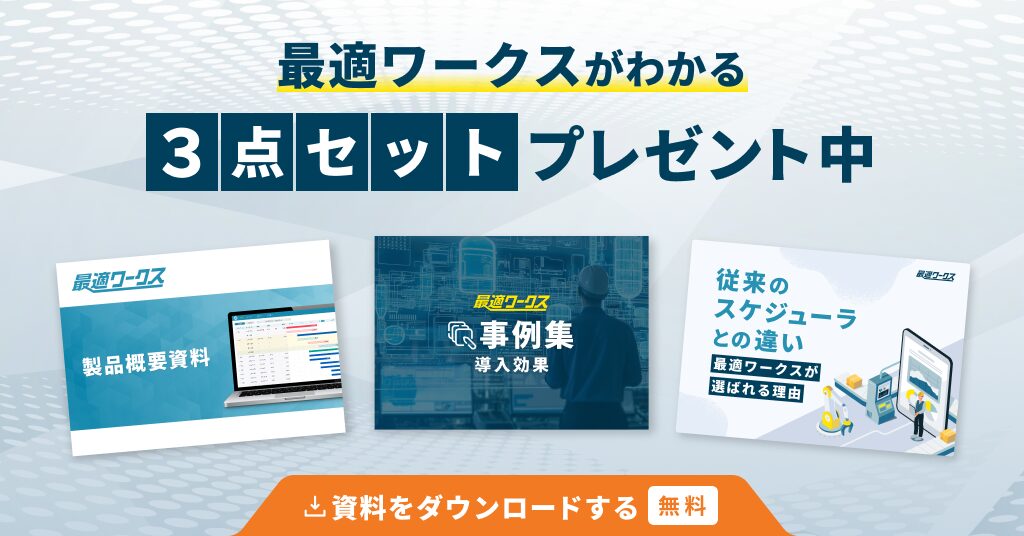