- コラム
儲かる工場のつくり方、経営に効く生産管理と原価管理について考える
目次
- 生産管理とは
- 原価管理とは
- 共通点と相違点
- 生産管理と原価管理の関係性まとめ
- 生産管理がうまく機能した成功事例
- 生産管理と原価管理の視点から見た成功要因
- 生産管理と原価管理の連携不全による失敗事例
- 失敗事例:とある食品メーカーの「原価改善プロジェクト」
- 原価改善の基本はPDCA活動
- 原価改善プロジェクトにおける4つの失敗理由
- まとめ:4つの失敗理由は「コミュニケーション不全」に帰結する
本日は「儲かる工場の作り方 ~経営に効く生産管理と原価管理について考える~」というテーマで講演させていただきます。
ではまず、「生産管理」と「原価管理」の共通点と相違点についてお話ししたいと思います。最初に、この2つの概念を正確に理解するため、定義を確認していきたいと思います。
生産管理とは
生産管理とは、「要求される品質の製品を、要求される時期に、要求量だけを、効率的に生産すること」を目的とする活動です。この定義からもわかるように、生産管理は生産現場における「QCD(品質・コスト・納期)」を達成するための管理を指します。
原価管理とは
原価管理とは、「製品の製造に関わる原価を適切に管理し、利益改善を図る活動」を指します。具体的には、目標とする原価(適正原価)と実際にかかった原価を比較し、その差異を分析することで問題点を特定し、改善活動を行うという流れです。
共通点と相違点
これらの定義を踏まえた上で、生産管理と原価管理は、どちらも製造活動を対象とする管理の活動であるという共通点があります。ただし、異なる点もあります。
生産管理と原価管理の共通点
生産管理と原価管理の両者とも、工場における生産活動が基盤となっており、「受注から製造、納品までの一連の流れ」を管理することを目的としています。つまり、製造プロセスを効率化することで、最終的には顧客満足度の向上や企業利益の改善につながる活動です。
生産管理と原価管理の相違点
生産管理と原価管理の大きな違いは視点です。生産管理は、より現場寄りの視点で、生産プロセスそのものを管理します。一方で、原価管理は経理的な視点で、製造プロセスがPL(損益計算書)上にどのように反映されているかを把握します。
下図のように、生産管理と原価管理の関係は、受注から製造、納品までの一連の流れにおいて表裏一体です。評価の単位ユニット自体は大きく変わらないものの、視点の違いによって捉え方が異なることがわかります。
各フェーズの生産管理の主な活動
- 受注:生産の見通しを立てる際に、生産計画を作成する。
- 購買・設備投資:必要な資材を計画的に調達するために、購買計画を作成する。
- 人材配置:作業員の配置や教育を含めた人員計画を立案する。
- 生産活動:実際の生産工程の活動指示を出し、進捗や効率を管理する。作業内容やコスト、工程の改善を図るように改善活動を進めていく。 …など
各フェーズの原価管理の主な活動
- 受注:製品原価の想定
- 購買・設備投資:仕入価格の管理
- 人材配置:人件費・単価管理
- 生産活動:人月費用管理 …など
目指す方向性は共通している
両者の視点は異なりますが、目指す方向性は同じです。生産管理が「タクトタイム」や「サイクルタイム」「製品のリードタイム」といった現場の指標を管理するのに対し、原価管理では、それらの指標が「コスト」という形で最終的にいくらかかったのかを管理します。
いずれの場合も、視点の違いはありますが、受注から生産、納品までの一連の活動を対象としており、数値や指標として示しつつ、効率化・改善を目的とするものです。
生産管理と原価管理の関係性まとめ
生産管理の目的は、要求される品質の製品を、要求される時期に、要求される量だけ効率的に生産することです。特に重要なのが「効率的に」という点で、これは現場での改善活動を進める上で欠かせない視点となります。
同様に、原価管理においても、単に原価を計算するだけではなく、「適正な原価」と「実際の原価」を比較し、その差異を分析して、あるべき姿に近づけていくアプローチを取ります。
生産管理と原価管理は、一見異なる分野に見えますが、最終的に目指す方向性は同じです。数値や指標を通じて、製造活動の状況を把握し、効率化や改善を目的とするという点で共通しています。
売上・利益への繋がり
ただし、こうした管理や改善活動を進めるにあたり、最終的には売上や利益に繋がらなければ意味がありません。製造業においては、製品が売れ、その売れる製品が製造・納品された段階で初めて売上と利益が生まれるわけです。この点を踏まえると、営業戦略や製造戦略と結びつけながら考える必要があります。
営業戦略の観点
営業戦略の視点では、収益性の高い製品の販売機会をいかに増やし、それを売るための仕組みをどう整えるかが重要です。
製造戦略の観点
製造戦略の視点では、製品の収益性を改善するために、いかに原価率を抑えるかが課題となります。特に収益性の低い製品については、その原価構造を見直し、改善活動を計画的に進めることが多いでしょう。
部署間連携の重要性
このように、製造現場での生産管理と全社レベルでの収支管理(原価管理)が連動していないと、収益性を改善し、業績を向上させることは難しくなります。結局のところ、生産管理と原価管理は、どちらも「業績を改善する」という共通の目標に向かっており、それを現場目線で見るか、全社目線で見るかの違いに過ぎません。
たとえるならば、山の頂上(=業績改善)を目指す際に、異なるルートから登るようなもの。それぞれの部署が異なる役割や視点を持ちながらも、最終的には同じ山頂を目指しているわけです。したがって、各部署が別々の取り組みをしているように見えても、活動や結果は密接に関わってきます。様々な改善活動のきっかけから、会社全体として連携して取り組むことで、業績改善に繋がるのだと考えます。
生産管理がうまく機能した成功事例
では、実際に生産管理がうまく機能した事例をご紹介させていただきます。
この事例は、スザキ工業所様という企業様のケースです。スザキ工業所様は従業員60名規模の会社で、生産管理を改善した結果として、以下のような成果を達成されました。
- 納期遵守率がほぼ100%に向上
- 不良品発生率がゼロに
- 生産数量が10%増加
- 残業時間が20%減少
- 原材料比率が2%削減
こうした成果は、生産管理の徹底と改善活動の実施によって得られたものです。それでは、具体的な背景や課題、解決方法について詳しくご紹介していきます。
課題:多品種化により手作業(人力)での生産管理の限界
スザキ工業所様が直面していた主な課題は、以下の通りです。
- 取引先の多様化
売上を伸ばすために新しい取引先を開拓し、受注を増やす必要がありました。その結果、受注形式が多様化し、製造品目数も大幅に増加しました。 - 現場管理の複雑化
製造品目が増えたことで、現場の生産管理が難しくなりました。紙ベースで作成していた生産計画の粒度が荒く、計画がタイムリーに更新できませんでした。 - 残業の常態化
生産計画が想定通りに進まないことが多く、計画外の対応として残業が常態化していました。特に、生産計画を担当されている個人の負担が増大し、「このままでは計画作業を続けられない」という声も上がるような状況でした。
解決方法:生産計画のデジタル化
こうした課題に対応するため、スザキ工業所様は弊社の「最適ワークス」を導入され、生産計画のデジタル化に取り組みました。その結果は以下の通りです。
- 生産計画の可視化・精度向上
生産計画がデジタル化されたことで、計画の全体像が見えるようになり、納期の管理が可能になりました。また、計画精度の向上に伴い、現場が計画に沿って動けるようになりました。 - 改善活動ができる体制構築
デジタル化によって、生産活動の振り返りがしやすくなり、計画データやマスターデータを基に改善活動を繰り返すサイクルを確立しました。
成果:生産管理の改善に成功
こうした取り組みによって得られた成果を、改めて整理します。
- 納期遵守率がほぼ100%に向上
生産の見通しが管理可能になり、納期回答のスピードと精度が向上しました。 - 不良品発生率がゼロに
生産計画の精度が上がり、現場の作業品質が向上した結果、不良品の発生が抑制されました。 - 生産数量が10%増加
計画的な生産と現場の効率化により、生産能力が向上しました。 - 残業時間が20%削減
計画通りに作業が進むようになり、残業が削減されました。結果として、従業員の負担が軽減され、職場環境が改善されました。 - 原材料比率が2%削減
不良品の発生が抑制されたことにより、無駄が減り、原材料の使用効率が改善されました。
事例詳細はこちら。
生産管理と原価管理の視点から見た成功要因
先の事例では、生産計画の精度向上により、不良品発生が減った結果、原材料の無駄な使用が抑えられて「原材料比率が2%削減」という成果につながりました。
そこで、原材料比率を削減する(原価を改善する)ための具体的なアクションについて、生産管理と原価管理の視点の違いを整理してみます。
原材料比率の削減
原価管理の視点からのアクション
原価管理では「コストを削減する」ことが主眼となります。例えば、次のような活動が挙げられます。
- 購買の効率化:原材料費の削減を目的に、購買ルールの見直しや複数のサプライヤーからの見積もり取得を実施するなど。
- 仕入先の再検討:仕入価格の競争力を高めるため、新たな仕入先の開拓を検討。
生産管理の視点からのアクション
生産管理では「作業効率の向上」を通じて全体のパフォーマンスを向上させることが目的です。例えば、次のような活動が挙げられます。
- 工程の改善:熟練工の動きをビデオ分析し、標準作業手順を策定するなど。設備について、作業時間を短縮するために配置や設定を見直す。
- 不良品の削減:スザキ工業所様の事例では、生産計画を可視化することで現場の焦りを減らし、不良品発生の原因になるミスを防ぐことができた。
成功事例からの示唆
この事例は、生産管理の改善が現場の作業効率や労働環境の改善に直結し、その結果として原価管理や収益性の向上にも貢献した好例です。得られる示唆として、次のようなポイントがあります。
主導者を明確にすることが重要
生産管理と原価管理は、会社の利益に直結します。そのため、誰が主導するかリーダーを明確にし、現場だけの改善活動ではなく全社をまたいだプロジェクトとして推進することが重要です。
製造状況の可視化から始める
生産管理を改善するために、まず製造状況を可視化し、製造の見通しを持つことが必要です。何がどうなっているか、状況を言語化できない中では改善活動は進みません。
生産管理と原価管理の相互影響
先の事例では、生産管理を改善することで、納期回答がスムーズになり、売上を伸ばすきっかけになりました。また、原価管理の視点では、不良品率の削減、残業時間の減少による人件費削減につながりました。
ここからもわかる通り、生産管理と原価管理の方向性は同じく、粗利率を上げ、利益を最大化することです。両者の視点の違いを活かしながら、相互に作用することで改善活動を進めることができます。
生産管理と原価管理の連携不全による失敗事例
冒頭で「生産管理と原価管理は、同じ山を目指しているけれども、登り方が違う」という話をしました。やはり相違点として、担当する部門が異なり、情報の共有の粒度が異なる点があります。ときに、こうした違いが業績改善の活動を進める上での妨げとなることがあります。
ここからは、生産管理と原価管理の連携がとれずに終わった失敗プロジェクトについて、実体験を交えながらお話しします。今回は、私が支援した「原価改善プロジェクト」をご紹介します。
失敗事例:とある食品メーカーの「原価改善プロジェクト」
この会社は食品メーカーであり、「原価改善プロジェクトを始めたい」という依頼を受けて、当時、経営コンサルタントであった私が支援をさせていただきました。
体制と背景
まず、以下の組織図をご覧ください。生産管理と原価管理が異なる部門で担当されている点に注目してください。生産管理は製造部門が主管し、原価管理は経理部門が主管しています。
- 生産管理:製造部門が主管
- 原価管理:経理部門が主管
表面化した課題:コミュニケーション不全
プロジェクト開始前に最初に挙がった大きな課題は、生産管理と原価管理の担当部門が異なることで、コミュニケーション不全が発生しているという点です。例えば、生産管理担当者や原価管理担当者と話を進めていく中で、以下の状況が明らかになりました。
部門間のズレ:経理・製造それぞれの課題
原価データが更新されていない
原価管理に関しては、仕入れ原価や物流コストについて、データが長期間更新されていない状態でした。また最新の製造状況を反映しないまま、実際の発生費用を製品納品数などで按分されており、製品ごとの正確な原価が把握できていませんでした。
データ共有の欠如
「ぼやけた」原価データは、管理部門だけが閲覧しており、現場とは共有されていない状態でした。また正確性の欠けたデータでは、改善活動の具体的な方向性が見えない状況に陥っていました。
製造工数のモニタリング不足
製造現場では製造工数のモニタリングが十分に行われておらず、改善活動に必要な基礎データも不足していました。
部門間のズレ:営業・製造それぞれの課題
さらにプロジェクトを進める中で、営業部門と製造部門の認識のズレも浮き彫りになりました。
営業部門
営業部門からは「どの製品が収益性が高いのか分からない」という声が挙がっていました。
顧客の求める価格で売りやすい商品を優先的に販売していた結果、原価割れの製品までも売上を立てるために販売している状況でした。
製造部門
製造部門では年間計画に基づき見込み生産を行っており、原材料費や製造コストの高騰は考慮されていませんでした。そのため、営業部門と製造部門の連携が取れず、平均販売単価が下がり、収益性が悪化していきました。
収益悪化の悪循環
さらに、コロナ禍の影響も加わり、在庫が残りやすくなったことで、以下のような悪循環が発生しました。
- 在庫を処分するために値引き販売を実施
- 収益性がさらに悪化
- 最終的に会社全体が赤字へと陥る
このような背景から「原価改善を行おう」という動きが始まりました。しかし、プロジェクトを進める中で、改めて生産管理と原価管理の連動の難しさが浮き彫りになりました。
原価改善の基本はPDCA活動
そもそも原価改善を進める際の基本的な流れは、PDCAサイクルを回すことです。このプロセスを繰り返していくのが、PDCA活動の基本的な流れです。
PDCAサイクルの基本ステップ
- 現状の可視化:まず課題の明確化と現状把握を行う。
- 改善活動の実施:具体的な施策を立案し、実行に移す。
- 結果の振り返りと課題抽出:改善の結果を分析し、新たな課題を抽出する。
- 再改善の立案・実行:抽出した課題に対し、次の改善策を実行する。
原価改善プロジェクトで取り組んだこと
最初に行うべきは、現状を把握し、改善計画を明確に立てることです。現状把握の第一歩として、この事例では「製造品目ごとの原価が分からない」という課題がありました。
そこでまず「製品ごとの原価を明確にすること」から着手しました。原価を把握するためには、購買管理や工数の可視化が必要になったので、デジタル化を進めることでデータの可視化にも同時に取り組みました。
加えて、一般的な原価改善の施策としては、一括購買や部材の共通化といった方法が挙げられます。このプロジェクトでも、こうした取り組みを並行して進めていました。こうして、生産管理と原価管理それぞれの側面から、以下のような具体策が実施されました。
生産管理の観点
- 原材料費に関して購買台帳を作成し、製品ごとに管理すること
- 日報から製品ごとに製造工数を正確に把握すること
- 日報から、作業員の稼働時間を正確に把握すること
原価管理の観点
- 原材料費は原料ごとに個別費用計上
- 時間あたりの人件費を計算して計上
- 製造時間あたりの費用の計算と計上し、水道光熱費を稼働時間に基づいて按分する
- 製造数量あたりの費用の計算と計上し、設備費を数量に基づいて按分する
生産管理と原価管理の連動のため
- 製造プロセスの数値(例えば生産効率や稼働率)と原価数値を連動させる
- データの可視化と精緻化を同時に進めていく
- 随時プロジェクトメンバーに進捗を共有し、改善活動を進める
しかし、結果は失敗に終わる
こうして、数値データを連動させ、計画を修正しながら改善活動を進めるという形でプロジェクトが始まりました。しかし、このプロジェクトは結果としてうまくいきませんでした。
原価管理や生産管理そのもののやり方に、大きな誤りがあったわけではありません。どの組織でも、原価管理や生産管理に関してやるべきことは大きく変わらないからです。
このプロジェクトで問題になったのは、互いの思いや部門ごとの目的がズレていたこと、それを調整し、合意形成を図る役割を担う調整役がいなかったことです。ここで重要なのは、問題の本質がコミュニケーション不全にあったという点です。この事例を通じて、その背景を少し深掘りします。
原価改善プロジェクトにおける4つの失敗理由
失敗理由1:期待値のズレ
最初に挙げられる失敗の理由は、経営陣とコンサルタントの間で、期待値がズレていたことです。
原価改善プロジェクトの進行には、現状の可視化や計画策定の準備に約1年を要し、成果が目に見えて現れるのは通常2年目以降です。しかし、経営陣は「早期に成果を出してほしい」と期待し、そのギャップがプロジェクト全体に影響を与えました。こうした問題は、社内にプロジェクトリーダーを立てて進める場合でも十分に起こり得ます。
期待値のズレが招いた問題
- スピード感に対する齟齬。成果を急ぐ経営陣の期待により、「すぐに成果を出せないなら意味がない」と不満が生じ、プロジェクトへの信頼が低下。
- 現状把握が不十分な状態での議論により、感覚論や期待論で判断される。データ未整備の状態で改善案が進行し、非現実的な計画が立てられる。
解決策
- 時間がかかることを事前に合意する
プロジェクトの初期段階で経営陣と共有し、合意形成を図ります。「初年度は現状把握と計画策定がメインであり、目に見える成果は2年目以降になる」という現実を明確に伝えます。 - スケジュール感と成果の検証方法を共有
プロジェクトの進捗をどのように評価するのか、成果が出ているかどうかをどのように検証するのかについて、経営陣と明確に共有します。これにより、現実的な進捗状況に基づいて評価が行われるようになります。 - 中間報告を積極的に行う
たとえ目に見える成果が出ていなくても、現状把握や計画策定の進捗について定期的に経営陣に報告することで、不信感が生じるのを防ぎます。 - 短期的な成果を意識したマイルストーンを設定
最終的な成果が2年目以降でも、初年度内に達成できる小さな成果を設定し、それを共有することで経営陣の期待を満たします。
失敗理由2:DXアレルギーによる現場での抵抗
現場が新しいシステムやツールの導入に抵抗感を示す「DXアレルギー」も失敗の一因です。
このプロジェクトでは、従来の紙やExcelベースの方法からデジタルツールへの移行に対し、現場から「効果が不明なものを今やる余裕はない」「現場は忙しいので、優先度の高い仕事がある」といった反発が見られました。
こうした反発は、現場が「新しい方法に馴染む負担」や「直接製造に関係しない業務」に対して心理的な抵抗を持つことが背景にあります。
解決策
- 経営トップのマネジメント層のコミットメント
プロジェクトの重要性を、全社的に明確に伝える必要があります。トップダウンで意思を伝えることで、現場の後回し体質を防ぐことができます。 - 現場に寄り添った取り組み方
現場の負担を最小限にし、従来の業務フローに近い形で新しい方法を導入するように調整します。
DXアレルギー克服に成功した事例
ここで、現場へのDXアレルギーへの対処が成功した事例として、あるプレス加工企業の例をご紹介します。
この会社では、初期工程がボトルネックとなっていたので、「製品ごとの投入順序」が適切かどうかをチェックする改善活動の取り組みを進めました。この事例では、DXを強く押し出すのではなく、次のような工夫を行いました。
- 現場に馴染む方法で情報を伝える
例えば、新しいシステムを一気に導入するのではなく、普段から現場で使用している看板やExcelの出力物を活用しました。これにより、現場の作業者が普段と同じように業務を進めることができ、違和感なく新しいプロセスを取り入れることができました。 - 本質は変えながら、見た目は変えない
生産計画を最適化するアルゴリズムを導入しつつも、現場が見る情報やツールは従来と同じ形式にしました。これにより、現場の抵抗感を抑えつつ、生産効率の改善を実現することができました。
このように現場のDXアレルギーを克服するためには、次のようなポイントが重要です。
- トップダウンでプロジェクトの重要性を伝え、現場に浸透させる。
- 現場が慣れ親しんだ方法を活用しながら進めることで、抵抗感を軽減する。
- 現場の負担を最小限に抑えながら、結果として改善効果が出るよう工夫する。
失敗理由3:コミットメントの欠如
プロジェクト停滞の大きな要因に、経営層や部門間での責任分担が不明確だったことが挙げられます。具体的には、以下のような状況が生じました。
営業部門の取締役:「これは製造部門がやるべきで、自分は見守る立場。最後に報告をくれればいい。」
製造部門の責任者:「原価効率の問題がきっかけなので、管理部門が主体的に旗を振るべきだ。協力はするが主体にはなれない。」
管理部門:「社長が全社課題として言い出したことなので、社長がリードするべき」
社長:「全社的な課題として認識しているが、製造と管理で協力して進めてほしい。」
結果として、「誰が旗振り役なのか」が曖昧なままプロジェクトが進み、調整が滞る場面が頻発しました。特に利害関係が絡む場面や既存の業務フローを変更する場面で、プロジェクトが何度も停止しました。
解決策
- 責任者の明確化
プロジェクトの責任者(旗振り役)を明確にすることが最優先です。これは単なる「担当者」ではなく、意思決定の権限を持つ責任者を置く必要があります。 - 組織的サポート
責任者をサポートする体制を作り、マネジメント層が一致団結してその人を支える仕組みを整える。
失敗理由4:コミュニケーション不足
最後に、失敗の根本原因として部門間・関係者間のコミュニケーション不足が挙げられます。例えば、現場からは「具体的な改善目標が見えない」「進捗が不明確」といった声が上がる一方、経営陣は現場の状況を正確に把握できていませんでした。
解決策
- 共通言語としての基準や指標の設定
全社で共通の物差しを持つことで、進捗や成果を具体的に議論できるようになります。
例えば、生産計画に基づいて基準を設定することで、生産計画に基づいて「計画通りに作業工程が進んでいるかどうか」を確認し、乖離があれば原因を突き止め、改善を進めることが可能です。 - 途中経過の判断基準を設定する
改善のプロセスで重要なのは、最終成果(原価改善)だけでなく、途中段階で何がどう進んでいるのかを測定することです。
例えば「計画と実績の差分」「各工程の進捗率」「無駄やロスの発生頻度」など
成功例:生産計画を基準にした改善活動
全員が理解できる「共通の言語」として、生産計画を活用することで、プロジェクトの途中経過を適切に把握し、改善活動をスムーズに進めることができます。ある企業では、生産計画を基準にして、次のようにプロジェクトを進めました。
- 計画を立て、実績との差分を分析: 論理的に正しい計画を立て、その計画と実績の差分を見える化。
- 差分の原因を議論: 差分が発生している場合、その原因が「入力データの誤り」なのか「現場の無駄」なのかを議論し、改善ポイントを特定。
- 全社的な改善活動に繋げる: 差分を解消するための具体的なアクションを設定し、部門間で連携して実行。
このように、生産計画を共通言語として使用することで、部門間のコミュニケーションが円滑になり、改善活動が効果的に進みました。生産計画を運用できる状況に改善活動を進めるというのは、効果を実感しながらプロジェクト推進できる方法のひとつです。
まとめ:4つの失敗理由は「コミュニケーション不全」に帰結する
これら4つの失敗理由を総括すると、最終的にはすべてコミュニケーションの問題だと考えられます。
生産管理や原価管理において、やるべきこと自体は明確であり、それを実行すれば本来成果は出るはずです。もし成果が出ないのであれば、その原因は、やるべきことができていない状況にあります。その背景に、次のような問題がある可能性があります。
- プロジェクトの方向性や進め方に対する期待値のずれ
- 現場のDXアレルギーによる取り組みの後回し
- 責任者が不明確なまま進むプロジェクト(コミットメントの欠如)
- 部門間で共通言語が欠けていることによる連携不足
こうした課題を解消するためには、プロジェクトの基盤となるコミュニケーションを見直し、現場と経営陣、部門間の調整をしっかり行うことが重要です。
原価改善プロジェクトが成功するためには、期待値の共有、現場の負担軽減、責任分担の明確化、円滑なコミュニケーションが鍵となります。特に、短期的な成果への過剰な期待を抑えつつ、現場に寄り添った地道な改善を進めることが、プロジェクト全体を成功に導くポイントだと考えます。
お気軽にご相談ください
本日の内容を踏まえ、もし原価改善や生産管理、あるいはDXに関連する取り組みについてご質問やご相談がありましたら、ぜひお問い合わせください。スカイディスクでは「最適ワークス」に限らず、さまざまな課題に対応するソリューションをご提案できます。本日はご清聴いただきありがとうございました。
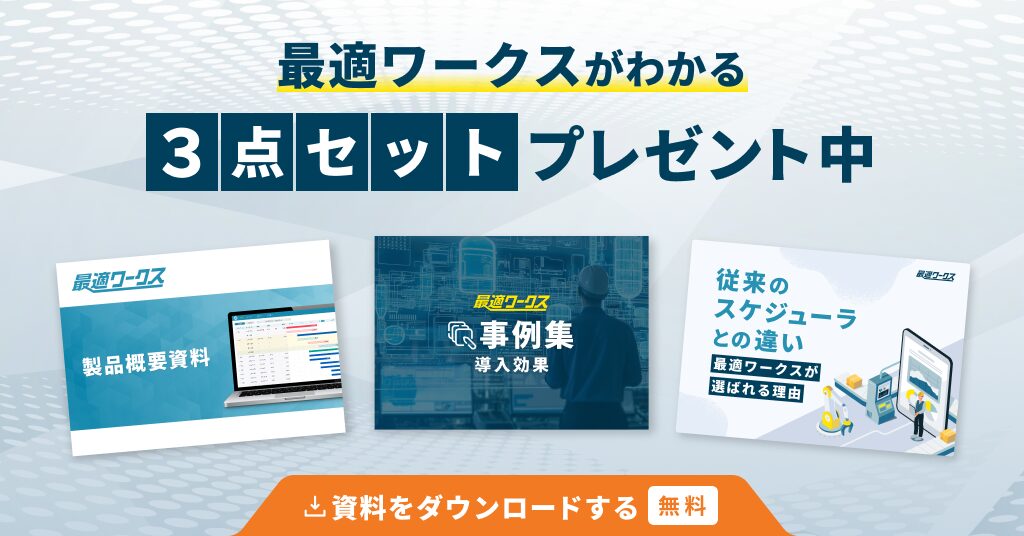