- コラム
製造業における平準化の必要性|平準化する方法やポイント等を解説
多品種少量生産が主流になった製造業では、平準化の重要性が増しています。平準化とは、月ごと、日ごとに生産する量と作る品目を一定にすることです。平準化は多くのメリットがある半面、実現するためにはいくつか注意点やポイントがあります。
そこで今回は平準化の必要性や、実現するための方法、ポイントなどを紹介します。多品種少量生産で過剰在庫や人件費の増大に悩む方は参考にしてください。
製造業における平準化の必要性
受注をもとに生産をする製造業では平準化はとても重要なテーマです。ここでは平準化に取り組む必要性を解説します。
1 人件費削減
平準化に取り組むことで人件費の削減につながります。なぜ平準化をすることで人件費の削減になるかは、平準化を取り入れていない場合と比較してみるとよく分かります。
平準化をしていない場合、生産量が月ごとに変動します。たとえばある月の生産量が100個、その次の月の生産量が200個と倍の数が必要になる場合、1カ月で200個生産できるように人員を確保しておく必要があります。つまり人員を生産のピーク時に合わせて確保しなければなりません。
しかし、生産量が平準化されておらず、変動する状況では、生産量が200個未満の月には人員が余ってしまい、ムダな人件費がかかってしまいます。
そこで月ごとの生産量を一定にする平準化を導入すればどうでしょうか。生産量が変わらなければ、余剰人員もなくなるため、人員計画を改善することができるのです。
2 在庫の適正化
平準化は在庫の適正化にも貢献します。あらかじめ需要を予測できれば、需要に応じた適切な在庫量にできるためです。
平準化に取り組んでいないと、急激な需要の変化に対応できず、受注量が極端に多い繫忙期には、在庫切れを起こす可能性があります。
しかし、平準化によって生産量を一定にできれば在庫が過不足するリスクを抑えることができます。需要を予測できれば計画的に見込み生産ができるため、在庫切れを起こすこともなくなります。
3 品質の確保
平準化は結果的に製品の品質を確保することにつながります。平準化をせずにいると、受注量が多い繫忙期には無理な生産計画を立ててしまいがちです。たとえば残業時間が多くなると作業者の集中力が落ちてしまい、品質にも悪影響を及ぼします。
さらに稼働時間が長くなればなるほど、設備にも過大な負荷がかかります。故障が多くなればなるほど、不良率も高くなり、思わぬ不良品を出すことが考えられます。しかし、平準化によって適切な稼働時間にできれば、作業者は集中して作業ができ、設備もメンテナンスを施せ、結果的に高品質な製品を作ることができるのです。
平準化と標準化の違い
平準化と似たような言葉に標準化があります。では平準化と標準化の違いは何でしょうか。
平準化とは、「生産量や作る品目を一定にすること」です。変動する受注量に合わせて生産量も増減させるのではなく、平準化では月ごと、日ごとの生産量を一定にさせます。また、作る品目を一定にすることも平準化に含まれます。特定の品種だけをまとめて作るのではなく、全ての品目をまんべんなく作るようにするのです。
一方の標準化は「ルールを決めて品質を一定にすること」を指します。ISOのように製品の規格を統一させ、作業のルールを決めることで誰が作業しても常に同じ品質にするといったことが標準化です。
トヨタのジャストインタイム生産方式からみる平準化
トヨタが開発した「ジャストインタイム」は製造業では最も有名な生産方式でしょう。ジャストインタイムとは、「必要なときに、必要なものを、必要なだけ」供給することを意味します。
ジャストインタイムの目的は主に在庫の削減です。顧客が求める製品だけを作るために、トヨタは後工程引き取り式を考え出します。通常の生産順序は前工程から後工程へと順に仕掛品を流していきますが、後工程引き取り式では後工程が必要な部品を前工程へ引き取りにいきます。
前工程は引き取られた部品だけを生産すればよいため、無駄な在庫がなくなるという生産方式です。ただし、後工程引き取り式を実現するためには平準化が必要になります。
仮に後工程引き取り式だけを導入して平準化ができていないとどうでしょうか。生産量が偏っていては、後工程が引き取った分だけを生産するのは困難です。特定の部品だけ不足してしまったり、過剰に作った部品の在庫が作業スペースを圧迫したりするでしょう。
そのため、生産の平準化ができていなければ、トヨタのジャストインタイムという生産方式は導入できないということです。
製造業において平準化を進める方法
では、平準化を導入するためには、どのような方法を選択すればよいでしょうか。その一つの方法が、生産の小ロット化です。小ロット化とは、一つ一つのロットを小分けにして一度に生産する量を少なくすることです。小ロット化の反対は、同一の品種を大量に生産する「まとめ生産」です。
「まとめ生産」は効率化には効果のある方法ですが、同一の品種をまとめて作るため平準化にはなりません。たとえばA製品、B製品、C製品があったとして、一日の生産能力が1200個だとします。A製品を一度に1000個生産するようにまとめ生産を計画したら、B製品とC製品は合わせて200個しか生産できません。これではA製品だけ在庫が増えてしまいます。
一方の小ロット化ではA製品、B製品、C製品も400個ずつ生産するようにします。全ての品種をまんべんなく作るようにするため、平準化に近づくのです。
また、平準化には需要を正確に予測することも必要です。先々の需要量を正確に予測することで、生産量の多い月があれば前倒しで見込み生産ができるためです。企業によっては取引先から内示という形で受注を貰っているものの、正確な需要を予測することは難しいという場合もあるかもしれません。
しかし、平準化のメリットを享受するためにも、取引先になるべく最新の受注見込みをもらうように相談するなど、需要を予測できる体制を整えることが大切になります。
製造業において平準化を進めるポイント
平準化を進めるためにはいくつか注意すべきポイントがあります。ここでは製造業において平準化を導入する時に考えておきたい点を紹介します。
ポイント1 スモールスタートする
一つ目のポイントは平準化に取り組む際はスモールスタートを心掛けることです。多品種を取り扱っている企業であれば、すべての製品に対して平準化を導入するのではなく、まずは一部の製品にだけ適用してみましょう。
平準化の目的の一つは在庫の適正化によるコスト削減です。製品の中には需要がそれほどなく、在庫量に占める割合が少ないものもあるはずです。そのため、在庫量が多い製品にだけ着目して段階的に平準化を進めると成功しやすくなります。
ポイント2 生産計画を見直す期間は柔軟に決定する
平準化に取り組むためには、生産計画を柔軟に変更することも大切です。たとえば前年度の生産実績から生産量を予測している場合には、今年度の生産実績も反映しながら予測していくと生産計画の精度も上がります。
また、一度作成した生産計画を見直すことも必要です。顧客からの注文量は変更されることが多くあります。そのため、生産計画を短いサイクルで作成できるようにして、常に需要に合わせた生産計画を作れるようにしましょう。
ポイント3 「平準化」だけに固執しない
平準化を導入する目的は、在庫の適正化や人員の最適化などによるコスト削減や品質の向上などです。平準化に固執しすぎて、平準化そのものが目的にならないようにしましょう。
企業によって最適な生産計画は異なるものです。平準化を取り入れたことによって逆にコストが増大したり品質が下がったりしないように、自社にとって最適な生産方法は何かを考えることが大切です。
ポイント4 従業員の力量も考慮する
現場で働く従業員の技量に差があると平準化を実現するのは困難になります。平準化を行うためには、すべての従業員が同じ技量を持っており、同じスピードで作業ができることが理想です。
従業員ごとに技量に差が出ないようにするには、標準化や教育が必要です。作業のマニュアル化を図り、一定のルールに従えば同じ作業ができるようにしましょう。
ポイント5 システムも活用する
平準化を実現するためには生産計画を練り上げる必要があります。たとえA製品、B製品、C製品の生産量を一定にしても、その代わりに納期遅れが発生したり、段取り替えが増えてしまい生産効率が下がったりすることもあります。
しかし、納期や効率を考えながら、生産する量と品種を一定にする生産計画を人間が考えるのは簡単ではありません。そこで生産スケジューラと呼ばれるソリューションシステムを活用するのが平準化には効果的です。
生産スケジューラはルールさえ設定すれば、自動的に最適な生産計画を立案します。人間が考える時には何時間もかかっていた難しい生産計画を瞬時に立案できるのです。
生産スケジューラについては、こちらの記事で詳しく解説していますので、ぜひご覧ください。
「生産スケジューラとは?導入メリット・導入の流れを解説」
まとめ
生産する量と品種を一定にする平準化は、これからの製造業で必要になるものです。平準化には小ロットでの生産を計画したり、正確な需要を予測したりといった取り組みも欠かせません。
また、平準化を実現するには生産計画を練り上げる必要があり、エクセルなどで立案するのは難しいものがあります。生産スケジューラは、納期や生産効率などを考えながら平準化を実現した生産計画を立案できます。平準化による在庫適正化や品質向上、人件費削減を実現したい方はぜひ導入をご検討ください。
生産管理を見える化して生産効率を劇的に改善、生産計画DXなら「最適ワークス」
生産管理を見える化して業務効率化を図りたい方は、「最適ワークス」を是非ご検討ください。最適ワークスの魅力は、そのコストパフォーマンス、迅速な導入、使いやすいシンプルな画面UI、手厚いサポート体制です。月額15万円という手頃な価格で、AIによる高度な最適化ソリューションを利用できるのは大きなメリットです。クラウドサービス(Saas)であるため、初期のハードウェア投資や複雑なシステム構築が不要で、導入スピードも非常に速いです。これにより、時間とリソースを節約し、迅速に業務改善を開始できます。
シンプルで直感的な画面UIは、特別な技術知識がなくても誰でも簡単に操作でき、誰でもスムーズに利用できます。また、カスタマーサクセスチームがユーザーと伴走し、最適ワークスを最大限に活用できるようサポートします。導入後も手厚いサービスを提供し、ビジネスの課題解決に直結した支援を行います。
低コストでありながら高機能、そしてサポート体制も充実しているため、DXや業務改善の第一歩として優れたサービスとなっています。
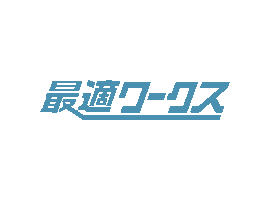
AIが生産計画を自動立案!生産計画・管理のDXを支援する製造業向けSaaS。工場の生産キャパ・製造進捗を可視化。納期回答の精度向上、残業時間を削減など中小・中堅工場での業績改善をサポート。専任エンジニア不要で使える!圧倒的コスパを実現。
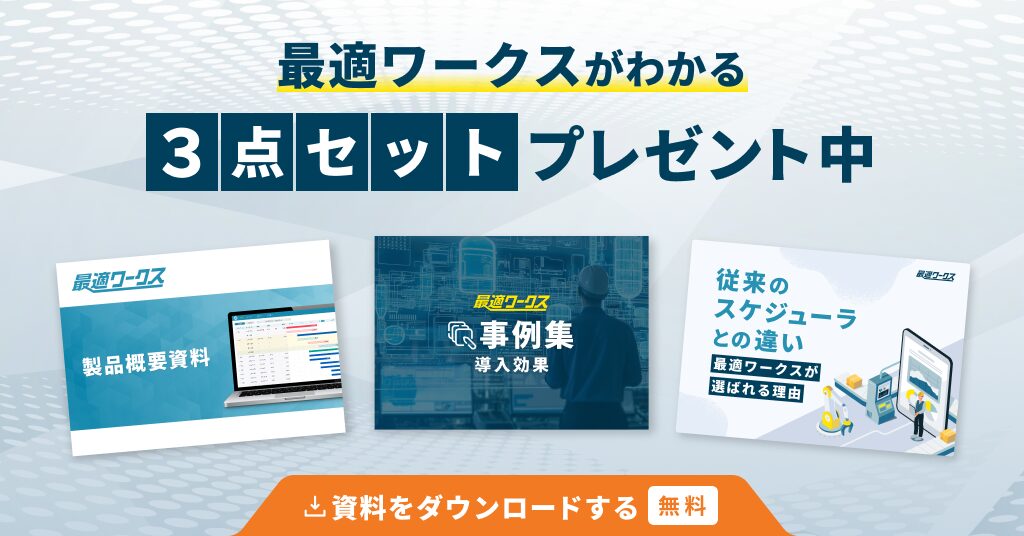