- コラム
製造業の生命線!QCDを制して生産管理のプロになろう!
「生産管理」と聞くと難しそうに感じるかもしれませんが、実は私たちの生活を支える製品がどのように作られ、届けられているのかを知る上で非常に重要な仕事です。
この記事では、生産管理の根幹をなす「QCD」というキーワードに焦点を当て、その重要性から具体的な改善方法までを解説します。この記事を読めば、あなたもQCDを意識した生産管理のプロフェッショナルになれるはずです。ぜひ最後までご覧ください!
1. QCDとは? 3つの要素を分かりやすく解説!
まず、「QCD」とは、製造業において、製品を生産する上で最も重要な3つの要素の頭文字をとった言葉です。
- Q(Quality):品質
- C(Cost):コスト
- D(Delivery):納期
これら3つの要素は、どれか1つでも欠けてしまうと、お客様に満足していただける製品を作ることができません。また、会社の経営にも大きな影響を与えてしまいます。それぞれ具体的に見ていきましょう。
Q(Quality):品質って何?
品質とは、「お客様が製品に求めるもの全て」のことです。それは製品の機能や性能だけでなく、見た目の美しさ、安全性、耐久性、使いやすさ、そして環境への配慮まで、様々な要素が含まれます。
例えば、おもちゃであれば、「安全に遊べるか」「壊れにくいか」「見た目が良いか」などが品質に関わってきます。また、食品であれば、「美味しく安全に食べられるか」「賞味期限は切れていないか」などが品質になります。
製造業では、お客様が「良い」と感じるものを作ることを目指します。品質の高い製品を作ることは、お客様からの信頼を得るために非常に重要です。
品質が低いと、不良品が発生しやすくなったり、製品がすぐに壊れてしまったりします。そうなると、お客様からのクレームが増え、会社の評判を落としてしまうことになります。
C(Cost):コストって何?
コストとは、「製品を作るためにかかるお金」のことです。例えば、製品を作るための材料費、工場で働く人の給料、機械を動かすための電気代などが含まれます。
製造業では、コストを適切に管理することが非常に重要です。なぜなら、コストが高すぎると、製品の値段も高くなり、お客様に買ってもらえなくなってしまいます。また、利益が出にくくなり、会社が成長できなくなってしまう可能性もあります。
コストを下げるためには、無駄な費用をなくしたり、効率的な生産方法を考えたりする必要があります。例えば、材料を無駄にしないように工夫したり、機械を効率よく使えるようにしたりします。
D(Delivery):納期って何?
納期とは、「製品をいつまでに作るか」という約束のことです。お客様は、必要な時に製品を手に入れることを期待しています。納期を守ることは、お客様の信頼を得るために非常に重要です。
納期が遅れると、お客様に迷惑をかけてしまい、信頼を失ってしまう可能性があります。また、最悪の場合、取引を打ち切られてしまうこともあります。
納期を守るためには、生産計画をしっかり立て、計画通りに生産を進める必要があります。
なぜ、製造業でQCDが重要なのか?
製造業において、QCDが重要な理由は、お客様に満足していただける製品を、安定的に、継続的に提供するためです。品質の高い製品を、適正なコストで、約束した納期までに届けることで、お客様からの信頼を得ることができます。また、会社の利益を確保し、成長につなげることができます。
QCDは、製造業の生命線と言っても過言ではありません。
より理解を深めるためにお菓子工場を例に考えてみましょう。
例:お菓子工場でのQCD
- Q(品質): 美味しくて安全なお菓子を作ること。異物混入や賞味期限切れがないように、徹底した品質管理が求められます。
- C(コスト): 材料費、人件費、製造にかかる費用をできるだけ抑えること。無駄なコストを削減し、利益を確保することが大切です。
- D(納期): お店の棚にお菓子が並ぶように、決められた期日までに商品を製造し、出荷すること。クリスマスやお正月など、需要が高い時期に間に合わせることも重要です。
このように、QCDはどの製造現場でも、常に意識する必要がある重要な要素です。
2. 生産管理におけるQCDの重要性:現場で起こる問題と解決策
生産管理とは、QCD(品質・コスト・納期)を最適化しながら、企業の競争力を維持・強化するために、製品の生産活動全体を管理する業務です。かつては「作れば売れる時代」でしたが、今日の成熟市場では、単に生産量を増やすだけでは企業の成長は見込めません。顧客のニーズに合致した高品質な製品を、適正なコストで、適切なタイミングで提供することが求められています。
ここでは、QCDの各要素が生産管理にどのような影響を与えるのかを具体的に見ていきましょう。
品質(Quality)を軽視した場合:クレームとコスト増の悪夢
品質を軽視すると、不良品が増加し、お客様からのクレームが多発します。不良品の再製作や返品対応には、余計なコストがかかります。また、会社の評判を落とし、お客様が離れてしまう可能性もあります。
例えば、ある自動車部品メーカーでは、品質検査を怠ったために、強度不足の部品が市場に出回ってしまいました。その結果、リコールが発生し、莫大な費用がかかりました。また、会社のブランドイメージも大きく損なわれました。これは、**「品質はコストよりも優先される」**という考え方が重要であることを示しています
生産管理部門が直面する現場の課題
- 不良品が頻発する:検査体制が整っていない、作業員の教育不足などが原因で不良品が発生しやすくなります。
- 再作業が増える:不良品を修正するために、余計な時間とコストがかかります。
- クレーム対応に追われる:お客様からのクレーム対応に追われ、本来の業務がおろそかになってしまう可能性があります。
解決策
- 品質管理体制の強化:検査基準を明確化し、作業員への教育を徹底します。
- 原因究明と対策:不良が発生した原因を徹底的に調査し、再発防止策を講じます。
- 品質管理の専門家を活用:外部の専門家を活用して、品質管理体制を改善することも有効です。
コスト(Cost)管理が不十分な場合:利益率低下と競争力喪失の危機
コスト管理を怠ると、利益率が低下し、会社の競争力が失われてしまいます。無駄な費用を削減し、効率的な生産を行うことが重要です。
例えば、あるアパレルメーカーでは、材料費の高騰や生産効率の悪化により、コストが大幅に増加しました。その結果、製品の価格を上げざるを得なくなり、お客様が他のメーカーの商品を買うようになってしまいました。このように、**「利益を最大化するためには、コスト削減が不可欠」**であると言えます
生産管理部門が直面する現場の課題
- 無駄なコストが多い:材料の無駄、エネルギーの無駄、人件費の無駄など、様々な無駄が発生している可能性があります。
- 価格競争に勝てない:コストが高いと、価格競争に勝てず、市場シェアを奪われてしまう可能性があります。
- 利益が出にくい:コストが高いと、どれだけ売っても利益が出にくくなってしまいます。
解決策
- 原価低減活動:材料費の見直し、生産プロセスの改善、エネルギー効率の向上など、様々な角度からコスト削減に取り組みます。
- 標準原価計算:製品ごとの標準原価を設定し、実績原価と比較することで、コスト管理を徹底します。
- IE手法の活用:動作分析やラインバランスなど、IE手法を活用して、生産効率を向上させます。
納期(Delivery)遅延した場合:顧客満足度低下と信頼失墜のピンチ
納期遅延は、お客様の信頼を損ない、会社の評判を落としてしまいます。納期を守ることは、お客様との信頼関係を築く上で非常に重要です。
例えば、ある電子部品メーカーでは、生産計画の甘さから納期が遅れてしまいました。その結果、お客様の生産ラインがストップしてしまい、多大な損害を与えてしまいました。お客様は、そのメーカーとの取引を打ち切ってしまいました。この例からもわかるように、**「納期は守るべき絶対的な約束」**です
生産管理部門が直面する現場の課題
- 生産計画が甘い:正確な生産計画を立てることができず、納期遅延が発生しやすくなります。
- 予期せぬトラブル:機械の故障や材料の遅延など、予期せぬトラブルにより、納期が遅れてしまう可能性があります。
- 進捗管理ができていない:生産進捗を正確に把握できていないため、納期遅延に気づくのが遅れてしまう可能性があります。
解決策
- 正確な生産計画:受注情報に基づいて、実現可能な生産計画を立てます。
- 進捗管理の徹底:生産進捗を常に把握し、遅延が発生しそうな場合は、早めに対策を講じます。
- リスク管理:予期せぬトラブルに備え、リスク管理体制を構築します。
- リードタイムの短縮:生産リードタイムを短縮することで、納期遅延のリスクを減らすことができます。
品質、コスト、納期は、生産管理において重要な3つの要素です。しかし、これらは互いに影響し合い、一つの要素を優先すると他の要素に影響が出る可能性があります。したがって、バランスを考慮した意思決定が不可欠です。
3. 生産計画とQCD:計画から実行までのポイント
生産計画は、QCDを達成するための羅針盤です。生産計画を立てる際には、品質、コスト、納期の3つの観点を考慮する必要があります。
生産計画の各工程とQCDの関係
生産計画は、大きく分けて以下の4つの工程から構成されています。
- 受注情報の確認:お客様からの注文内容(製品の種類、数量、納期など)を正確に把握します。
- 生産スケジュールの策定:受注情報に基づいて、いつまでに、どの製品を、どれだけ作るのかという計画を立てます。
- 負荷計画の作成:生産スケジュールに合わせて、必要な人員、機械、材料を確保する計画を立てます。
- 生産指示:作成した計画に基づいて、現場に生産指示を出します。
各工程で、QCDをどのように考慮するのか見ていきましょう。
- 受注情報の確認: お客様の要望(品質、納期)を正確に把握することは、その後の計画の基礎となります。また、コストを考慮し、採算の取れる注文かどうかを判断する必要があります。
- 生産スケジュールの策定: 納期を守れるように、リードタイムを考慮したスケジュールを立てる必要があります。また、品質を確保するために、無理のない生産スケジュールを立てることが重要です。
- 負荷計画の作成: コストを抑えるために、無駄のない人員配置、機械の使用計画を立てる必要があります。また、品質を確保するために、十分な人員と設備を確保する必要があります。
- 生産指示: 現場に正確な指示を出し、計画通りに生産を進めてもらう必要があります。
スケジューリングや負荷計画のポイント
- リードタイムの設定: 適切なリードタイムを設定することで、納期遅延を防ぐことができます。リードタイムを短縮することも、納期遵守には有効です。
- 在庫管理: 適切な在庫管理を行うことで、材料不足による納期遅延を防ぐことができます。また、過剰な在庫を抱えることはコスト増につながるため、適正な在庫量を維持する必要があります。
- ボトルネックの解消: 生産ライン上のボトルネックとなっている工程を特定し、改善することで、生産効率を向上させることができます。
- 柔軟な計画: 予期せぬトラブルが発生した場合でも、柔軟に対応できるように、予備の計画を立てておくことが重要です。
マイルストーン管理とPDCA
生産計画は、計画を立てたら終わりではありません。計画の進捗を定期的に確認し、遅延や問題が発生した場合は、早めに対策を講じる必要があります。
- マイルストーン管理: 生産計画の各段階で、達成すべき目標を設定し、進捗状況を把握します。
- PDCAサイクル: 計画(Plan)→実行(Do)→評価(Check)→改善(Action)のサイクルを回すことで、生産計画を継続的に改善します。
スザキ工業所の事例:最適ワークスで不良品ゼロを実現!
金属加工メーカーのスザキ工業所では、生産計画に「最適ワークス」を導入したことで、目覚ましい成果を上げています。
最適ワークスを活用することで、ムリ・ムダのない効率的な生産計画を立案できるようになった結果、現場は無理な納期に追われることなく、計画的に作業を進めることが可能になりました。これにより、作業員に余裕が生まれ、焦りによる不良品の発生を抑えることができたのです。
スザキ工業所では、最適ワークス導入後、1年間不良品ゼロを達成しました。不良品の減少は、品質の向上だけでなく、再作業によるコストやムダになる原材料費の削減にもつながり、大きな効果をもたらしました。
最適ワークス導入の効果
- ムリ・ムダのない効率的な生産計画の立案: 無理のないスケジュールで、納期を遵守できるようになりました。
- 不良品発生の抑制: 作業員の焦りがなくなり、1年間不良品をゼロにすることができました。
- コスト削減: 不良品による再作業コストや、ムダになる原材料費が削減されました。
スザキ工業所の事例は、生産計画をしっかり立てることが、QCDを向上させる上で非常に重要であることを示しています。
4. QCDを向上させるための手法:具体策で現場をレベルアップ!
QCDを向上させるためには、様々な手法があります。ここでは、代表的な手法をテーマ別に紹介します。
品質管理
品質管理とは、**「不良品をできるだけ減らし、お客様に喜ばれる質の高い製品を作る」**ための活動です。この目標を達成するために、現場から会社全体まで、様々なレベルで取り組みが行われています。具体的には、以下のような手法が用いられます。
- QCサークル: 現場の従業員がチームを組み、製品の品質に関する問題を解決する活動です。例えば、「最近、この製品の不良品が増えているけど、原因は何だろう?」とチームで話し合い、不良品の原因を探ったり、作業方法を改善したりします。 まるで、学校の部活動でチームが課題を見つけて解決策を考えるように、現場の知恵を活かして品質向上を目指します。
- TQM(総合的品質管理): 経営層から現場の従業員まで、全員が品質向上に取り組むことを目指す、会社全体での取り組みです。例えば、「お客様に最高品質の製品を提供しよう!」という目標を掲げ、社長から新入社員まで、全員がそれぞれの立場で品質向上に貢献します。 これは、会社全体が一つのチームとなり、共通の目標に向かって進むようなものです。
- 5S活動: 「整理、整頓、清掃、清潔、躾」の5つのSを徹底することで、作業環境を改善し、品質向上につなげる活動です。例えば、工具を整理整頓して、必要な時にすぐに見つけられるようにしたり、作業場をきれいに掃除して、製品にゴミやホコリがつかないようにします。 きれいな作業環境は、安全で効率的な作業につながり、結果として製品の品質も向上します。
- 品質検査: 抜き取り検査や全数検査など、適切な検査を行うことで、不良品の流出を防ぐ活動です。例えば、完成した製品をいくつか抜き出して検査し、問題がないか確認したり、重要な部品については、全ての製品を検査して不良品がないかを確認します。 これは、出荷する前に製品をチェックすることで、お客様に安心して製品を使っていただくための重要なプロセスです。
- トレーサビリティ: 製品の製造履歴を追跡できるようにすることで、問題が発生した場合に、原因を特定しやすくする活動です。例えば、製品に使われた材料や、どの機械で製造されたかなどを記録しておけば、もし製品に問題が起きた時に、「このロットの製品に使われた材料に問題があった」といった原因を特定し、再発防止につなげることができます。 これは、製品の品質に責任を持つために、非常に重要な仕組みです。
コスト管理
コスト管理とは、**「無駄な費用を減らし、効率よく製品を作る」**ための活動です。良い製品を、できるだけ安くお客様に提供するためには、コスト管理が欠かせません。具体的には、以下のような手法が用いられます。
- 原価企画: 製品の設計段階から、コストを意識して設計を行う活動です。例えば、製品を設計する段階で、「この部品をもっと簡単に作れる形にできないか?」とか、「この材料はもっと安いもので代用できないか?」といったことを検討し、できるだけ安く作れるように設計します。 これは、製品を開発する段階から、コストを意識することで、無駄な費用を抑えるための活動です。
- 標準原価計算: 製品ごとの標準原価を設定し、実績原価と比較することで、コスト管理を徹底する活動です。例えば、製品1個あたりにかかる材料費や人件費などの標準的なコストをあらかじめ計算しておき、実際に製品を作るのにかかったコストと比較して、「なぜ、標準よりもコストがかかったのか?」を分析し、改善策を見つけます。 これは、無駄なコストを洗い出し、効率的な生産活動を行うための重要な取り組みです。
- IE手法(動作分析・ラインバランス): 作業動作を分析し、無駄な動作を削減したり、生産ラインのバランスを調整したりすることで、生産効率を向上させる活動です。例えば、工場で働く人が、製品を組み立てる際に、無駄な動きをしていないかビデオで分析し、より効率的な作業手順を検討します。また、作業の待ち時間が発生しないように、作業員の配置や作業の順番を調整します。 これは、作業効率を高め、生産性を向上させるための活動です。
- VE(価値分析): 製品の価値を維持しながら、コストを削減するための手法です。例えば、製品の機能を損なうことなく、より安い材料で同じ性能を実現できないか検討したり、製品の製造方法を工夫して、より安く作れるように検討します。 これは、製品の価値を維持しながら、無駄なコストを削減するための活動です。
- 購買管理: 材料の調達コストを削減するために、最適なサプライヤーを選定したり、価格交渉を行ったりする活動です。例えば、複数の材料メーカーに見積もりを依頼し、最も安い価格で、必要な品質の材料を調達できるように交渉します。また、大量に購入することで、割引を受けるなど、より有利な条件で材料を調達するように努めます。 これは、材料費を抑え、製品のコストを下げるための活動です。
納期管理
納期管理とは、**「お客様との約束を守り、期日までに製品を届ける」**ための活動です。具体的には、以下のような手法が用いられます。
- リードタイム短縮のためのMUDA(ムダ)排除: 生産プロセスにおける無駄を徹底的に排除し、リードタイムを短縮します。例えば、製品を作る工程で、作業の待ち時間をできるだけ減らしたり、部品を運ぶ距離を短くしたりします。また、無駄な作業をなくすことで、製品が完成するまでの時間を短くします。 これは、製品をスムーズに、より早くお客様にお届けするために、生産プロセス全体を見直す取り組みです。
- TOC(制約理論)の活用: 生産ライン上のボトルネックとなっている工程を特定し、集中的に改善することで、生産効率を向上させます。例えば、製品を作る工程の中で、一番遅れている工程を見つけて、「なぜ遅れているのだろう?」と原因を分析し、その工程に人員や機械を増やしたり、作業方法を改善したりします。 これは、全体の生産量を増やすために、生産ラインの中で一番ボトルネックになっている部分を重点的に改善する手法です。
- 生産スケジューラー: 生産計画を自動化するためのツールです。例えば、お客様からの注文が入ったら、その情報をシステムに入力すると、自動的に生産スケジュールを立ててくれます。 これにより、人が手作業でスケジュールを立てる手間が省け、より正確で迅速な生産計画を立てることができます。
- 生産管理システム(ERP/MES): 生産計画、在庫管理、進捗管理などを一元的に行うためのシステムです。例えば、システム上で、製品が今どの工程にあるかリアルタイムで把握したり、在庫がどれくらいあるか確認したりできます。 これにより、生産状況を正確に把握し、納期遅れなどの問題を未然に防ぐことができます。
- かんばん方式: 必要な時に、必要なものを、必要なだけ生産する方式です。例えば、次の工程で必要な部品だけを生産することで、作りすぎによる無駄な在庫を減らし、必要な時に必要なものが生産できるようにします。 これは、無駄な在庫を減らし、より効率的に生産を進めるための仕組みです。
ITツールの活用
近年では、生産管理システム(ERP/MES)や在庫管理システム、BIツールなど、ITツールを活用することで、QCDを効果的に向上させることができます。
- 生産管理システム(ERP/MES): 生産計画、在庫管理、進捗管理、品質管理など、生産活動全体をシステムで管理することができます。これにより、業務効率が向上し、生産現場の見える化も進みます。
- 在庫管理システム: 在庫状況を正確に把握し、過剰在庫や在庫切れを防ぐことができます。
- BIツール: 生産データや品質データを分析し、問題点を特定したり、改善策を立案したりするのに役立ちます。
ITツールを活用することで、人手では難しかった大量のデータを分析したり、業務を自動化したりすることが可能になります。これにより、QCDの向上だけでなく、業務効率の向上にもつながります。
まとめ:QCDを制して、生産管理の未来を切り開こう!
今回は、生産管理におけるQCDの重要性や、具体的な改善手法について解説しました。QCDは、製造業にとって、なくてはならない重要な要素です。
QCDを意識した生産管理を行うことで、品質の高い製品を、適正なコストで、約束した納期までに、お客様に提供することができます。
この記事が、皆さんの日々の業務にお役に立てれば幸いです。QCDを制して、生産管理の未来を切り開いていきましょう!
生産管理でDXを始めるなら生産スケジューラ「最適ワークス」がおすすめ
生産管理で起点となるのが生産計画です。DXを始めるならまずは生産計画から始めることがおすすめです。生産スケジューラの導入費用をもっと抑えたい、可能な限り早く導入したい、導入後に使いこなせるか不安、といったご不安がある方は、「最適ワークス」も是非ご検討ください。最適ワークスの魅力は、そのコストパフォーマンス、迅速な導入、使いやすいシンプルな画面UI、手厚いサポート体制です。月額15万円という手頃な価格で、AIによる高度な最適化ソリューションを利用できるのは大きなメリットです。クラウドサービス(Saas)であるため、初期のハードウェア投資や複雑なシステム構築が不要で、導入スピードも非常に速いです。これにより、時間とリソースを節約し、迅速に業務改善を開始できます。
シンプルで直感的な画面UIは、特別な技術知識がなくても誰でも簡単に操作でき、誰でもスムーズに利用できます。また、カスタマーサクセスチームがユーザーと伴走し、最適ワークスを最大限に活用できるようサポートします。導入後も手厚いサービスを提供し、ビジネスの課題解決に直結した支援を行います。
低コストでありながら高機能、そしてサポート体制も充実しているため、DXや業務改善の第一歩として優れたサービスとなっています。
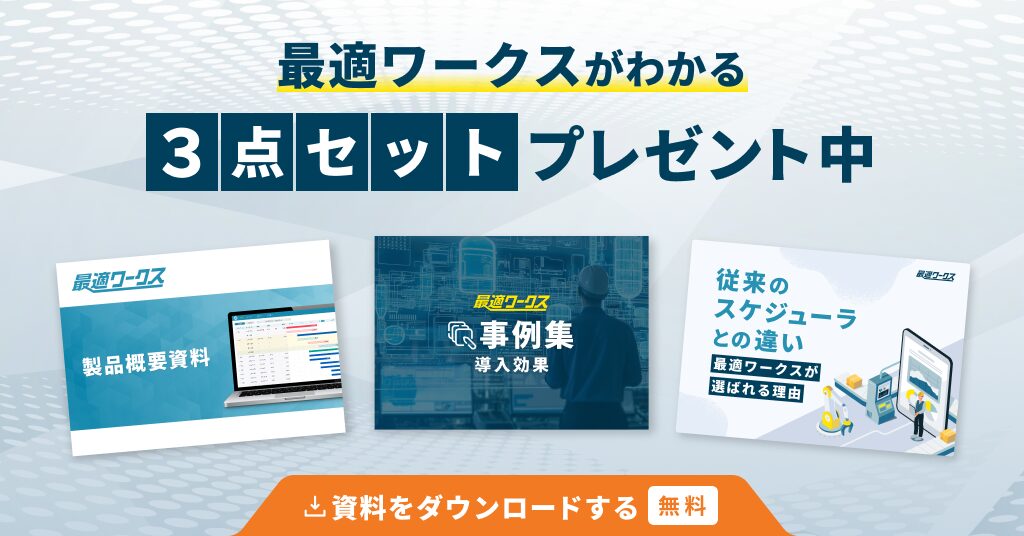