- コラム
生産管理とは?基本から課題・改善手法・DX導入まで徹底解説【製造業向け完全ガイド】
「納期通りに製品が仕上がらない」「在庫が多すぎてコストがかかる」「現場の進捗が見えない」──そんな悩みをお持ちではありませんか? 多くの製造現場で課題となるのが“生産管理”です。本記事では、生産管理の基本から実践的な改善手法、さらにはDXによる革新まで、現場視点でわかりやすく解説します。読み終えたときには、自社の課題を整理し、改善の第一歩を踏み出せる内容になっています。
製造業において、生産管理は「品質」「コスト」「納期」(QCD)を守るために欠かせない業務です。本記事では、生産管理の基本から現場でよくある課題、その解決策、そして生産管理のDX(デジタル変革)まで、わかりやすく丁寧に解説します。
1. 生産管理とは?
生産管理とは、製造現場において製品を「必要なときに、必要な数だけ、適切な品質で」提供するための管理活動のことです。生産管理はQCD(品質・コスト・納期)を最適に保つために、計画・工程・在庫・品質など幅広い領域をカバーします。
その役割は、単なるスケジュール調整だけでなく、原材料の手配、人員の割り当て、設備の稼働状況の把握、納期遵守、さらには品質の安定など、現場全体を最適に動かすための“司令塔”とも言える存在です。
2. 生産管理と他の管理業務との違い
生産管理は製造業における中枢の管理業務ですが、よく似た用語として「工程管理」「品質管理」「在庫管理」などがあります。それぞれの違いを簡潔にまとめると以下の通りです:
- 工程管理:製造工程ごとの進捗や作業順序を管理
- 品質管理:製品の品質基準を守るための検査や分析を行う
- 在庫管理:原材料や部品の適正在庫を保ち、欠品や過剰在庫を防ぐ
生産管理はこれら全体を束ねる立場で、全体の最適化を担う上位概念です。
3. 生産管理の課題とその対策
生産管理にはさまざまな課題がつきものです。代表的な課題とそれに対する対策は以下の通りです。
課題例と対策:
- 計画がズレる → 実績データを活用して予実管理を強化
- 属人化 → 作業手順書を整備し、誰でも判断できる仕組みを作る
- 在庫が過剰/不足 → 適正在庫の基準を設定し、予測精度を上げる
- 納期遅れ → 工程進捗のリアルタイム管理で早期に遅延を察知
ポイントは、まずは“見える化”して問題を把握し、標準化・仕組み化で解決することです。
4. 生産管理システムとは?
生産管理システムとは、手作業やExcelに頼っていた管理業務をシステム上で一元化・効率化するためのツールです。
主な機能:
- 生産計画の立案と自動調整
- 工程ごとの進捗状況のリアルタイム表示
- 資材の在庫状況と発注タイミングの管理
- 作業実績の記録とデータ分析
導入のポイントは「小さく始めて効果を見ながら段階的に拡張する」こと。いきなりすべての工程をシステム化するのではなく、例えば「納期遅れが多い工程」など課題の大きい部分から導入するのがおすすめです。
5. 生産管理のDXとは?
DX(デジタルトランスフォーメーション)とは、デジタル技術を使って業務のやり方自体を変える取り組みです。
生産管理におけるDXでは、以下のような変化が起こります:
- AIによる生産計画の自動最適化
- センサーによる工程の自動モニタリング
- クラウドでのリアルタイムな情報共有
- データ分析による業務改善のPDCA
単なるシステム導入ではなく、現場の判断や働き方を変える仕組みづくりがポイントです。
6. よくある質問(FAQ)
Q1. 生産管理と工程管理の違いは何ですか?
A. 工程管理は製造の各作業ステップの進捗を管理する業務で、いわば“部分最適”です。一方、生産管理は材料調達から納品までの流れ全体を見て、QCDのバランスを取りながら“全体最適”を実現する業務です。
Q2. 生産管理に必要なスキルや資格は何ですか?
A. 必須資格はありませんが、以下の知識・スキルが求められます:
- 生産計画と在庫管理の基礎知識
- Excelなどの基本的なITリテラシー
- コミュニケーション能力(現場・管理部門との調整)
- 品質管理検定(QC検定)やIE(インダストリアルエンジニアリング)の知識があると有利です
Q3. 中小企業でも生産管理のDXは実現できますか?
A. 十分に可能です。まずは紙やExcelから「工程の見える化」「進捗の共有」など、一部の工程をデジタル化するところから始めることで、無理なく導入が進められます。
Q4. システムを導入する場合、どこから始めるべきですか?
A. まずは「どこに一番問題があるか」を洗い出し、そこに絞ってスモールスタートするのが理想です。たとえば「納期遅れが多い」「在庫が合わない」といった具体的な課題から着手しましょう。
Q5. 現場がITに抵抗感を持っている場合、どうすればよいですか?
A. 導入前に現場の声をしっかり聞き、「何に困っているか」「何が面倒か」を把握することが重要です。最初から“全部デジタル化する”のではなく、現場がメリットを実感できる小さな改善から始めるのが成功のカギです。
7. 他社との比較・導入事例
事例1:中堅部品メーカーA社(従業員80名)
- 課題:生産計画は属人化しており、現場が混乱。納期遅れも多発。
- 取り組み:各部門のリーダーと現場ヒアリングを実施し、Excelで工程進捗を見える化。さらに標準作業手順書を整備。
- 成果:納期遵守率が78%→94%に改善。新人でも作業の判断がしやすくなった。
事例2:金属加工B社(従業員30名)
- 課題:在庫が過剰で保管スペースが圧迫。欠品も頻発。
- 取り組み:在庫をクラウドで一元管理し、購買部門とリアルタイム共有。発注基準の見直しも実施。
- 成果:在庫ロスが40%削減。誤発注ゼロを実現。
事例3:大手電機部品メーカーC社(サプライチェーン強化プロジェクト)
- 課題:日次の生産計画調整に毎日2時間以上かかっていた。
- 取り組み:AIによる生産計画自動立案ツールを導入。営業・購買・現場のスケジュールを統合。
- 成果:日次調整時間が月40時間→10時間に短縮。購買計画の精度も大幅に向上。
8. 比較表・フローによる理解の促進
🔄 生産管理と類似業務の違い
管理項目 | 主な目的 | 管理範囲 |
---|---|---|
生産管理 | QCDの最適化 | 工程・人材・設備・在庫全体 |
工程管理 | 工程ごとの進捗把握 | 製造の各工程(切削・組立など) |
品質管理 | 品質維持・改善 | 製品の不良率や基準の管理 |
在庫管理 | 在庫の適正化 | 材料・仕掛品・製品の在庫数 |
🧭 生産管理改善の流れ
- 現状の工程・納期・在庫を見える化
- 問題点を洗い出す(属人化/不明瞭な手順)
- 作業標準化・ルール作成
- システム化(Excelまたはクラウド)
- 継続的な改善とデータ活用
9. まとめ
生産管理は「品質」「コスト」「納期」のQCDすべてに直結する、製造業の土台となる業務です。しかし、見落とされがちなのが“生産計画”の重要性です。どんなに管理体制を整えても、計画が曖昧では改善の成果は得られません。
本記事で紹介したように、生産管理と生産計画は一体で考えるべきです。計画を立て、それを管理し、改善につなげる。その循環こそが、持続可能な現場づくりの鍵です。明日からの一歩を、ここから始めてみませんか? 生産管理は製造業の中核を担う業務です。現場の属人化や混乱を解消し、安定した生産体制を築くためには「見える化」「標準化」「仕組み化」が必要です。
そして、それを支えるのがシステムとDX。大がかりな変革でなくても、小さく始めることで確実な変化を生み出すことができます。
本記事が、みなさまの現場改善の第一歩となれば幸いです。
生産管理でDXを始めるなら生産スケジューラ「最適ワークス」がおすすめ
生産管理で起点となるのが生産計画です。DXを始めるならまずは生産計画から始めることがおすすめです。生産スケジューラの導入費用をもっと抑えたい、可能な限り早く導入したい、導入後に使いこなせるか不安、といったご不安がある方は、「最適ワークス」も是非ご検討ください。最適ワークスの魅力は、そのコストパフォーマンス、迅速な導入、使いやすいシンプルな画面UI、手厚いサポート体制です。月額15万円という手頃な価格で、AIによる高度な最適化ソリューションを利用できるのは大きなメリットです。クラウドサービス(Saas)であるため、初期のハードウェア投資や複雑なシステム構築が不要で、導入スピードも非常に速いです。これにより、時間とリソースを節約し、迅速に業務改善を開始できます。
シンプルで直感的な画面UIは、特別な技術知識がなくても誰でも簡単に操作でき、誰でもスムーズに利用できます。また、カスタマーサクセスチームがユーザーと伴走し、最適ワークスを最大限に活用できるようサポートします。導入後も手厚いサービスを提供し、ビジネスの課題解決に直結した支援を行います。
低コストでありながら高機能、そしてサポート体制も充実しているため、DXや業務改善の第一歩として優れたサービスとなっています。
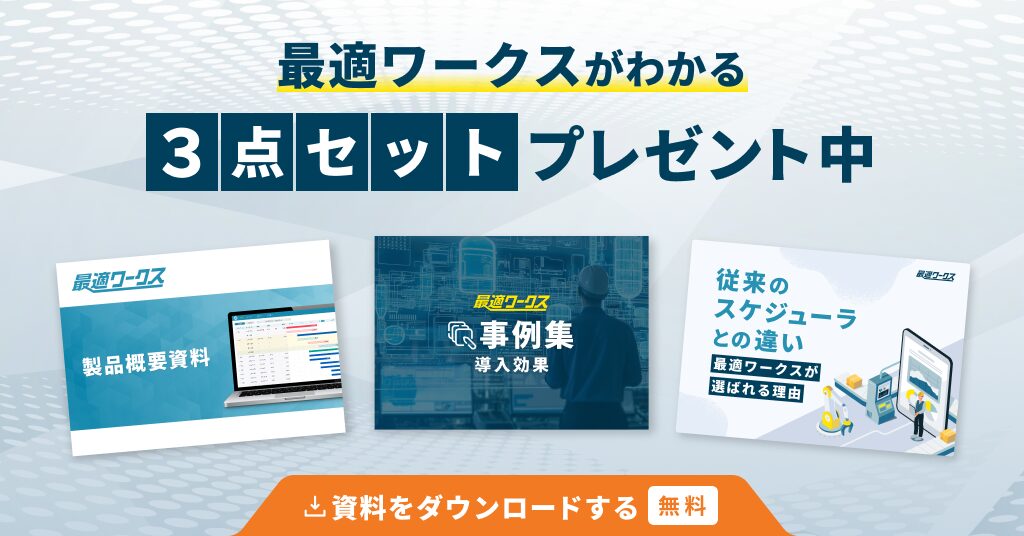