- コラム
部品工場で品質不良・不具合が発生する原因と品質不良を可能な限り防止する対策とは
製造業において粗利率を改善するためにも、品質不良の製品を減らす必要があります。あらゆる対策を色々な工場で実施しているにもかかわらず、なぜ品質不良が発生するのでしょうか。この記事では、発生の原因と不良品率を改善する方法について考えていきたいと思います。
製造業における品質不良・不具合の定義とは
製造業の製品づくりでは、常に品質が求められます。仮に、品質不良・不具合と定義された場合にはその製品は出荷することができません。では、何が品質不良・不具合にあたるのでしょうか。
品質とは
製造業の品質の定義とは、企業内の項目や顧客のニーズなどを満たすためのルールです。そのため、企業内で設定してある基準値や、顧客との間で合意された条件を満たすものでなければ、すべて品質不良にあたるといえるでしょう。
設計品質
製品設計者が想定・規定した品質のことです。作業の内容だけではなく、現存する機器や加工する材料、生産工程なども想定したうえで商品の品質を設定します。
製造品質
商品を製造した際の品質を指すものです。設計品質をクリアしたうえで、製造基準を設け、それを満たしたものが出荷されることになります。また、製造品質は、設計品質・製造基準と乖離しない製品を作ることが重要です。
加えて、製品の不具合や社内規格に沿っているかどうかも製品の品質として評価されることになります。設計品質が製品全体の品質につながることもあるため、製造業における品質は非常に幅広い意味合いをもちます。
品質不良とは
製造業の品質不良の定義とは、品質で定めた規格やニーズから外れることを指します。
例えば、プレス加工部品を組み立てた製品の中で、出荷前から塗料やメッキ加工が一部剥がれている場合などは品質不良に分類されるでしょう。その他にも、製品の一部が破損している、正しい位置にボルトがない、色に違和感があり材質が変化している可能性がある、なども全て品質不良とみなされるでしょう。
品質不良となった製品は利益にはつながらず、原材料が無駄となる為全社的なコストの増加を招きます。管理体制の強化や新製品を作成する度に研修などで製造知識を共有する事がよくありますが、品質不良を防ぐことで利益率の改善を図ることが目的に一つとなっています。
製造業における品質不良の原因とは
製造業で、品質不良が起こる原因は人材や材料不良だけではありません。製造業において品質不良が起こる原因は様々で、一つの理由に絞って考えることは難しいです。
例えば、以下のような要因が品質不良・不良品発生の原因としてよく挙げられます。
- 人材による作業ミス(ヒューマンエラー)
- 基準不備(社内体制や作業手順の共有不足)
- 材料不良
- 計画外作業による段取り時間の不足
実務的には、これらが発生した要因をさらに考える必要があります。例えば、ヒューマンエラーがよく起こるといっても、作業者の技術力を改善すれば、不良品率が必ずしも改善するわけではありません。ヒューマンエラーが発生した理由を客観的に分析し、的確な改善対策を考える必要があるでしょう。
ヒューマンエラーといわれる要因に焦点をあててみると、
- 部品の取り付け間違い→生産管理のミス
- 図面の記載が複雑→設計図のミス
- 図面のデータが古い→管理者のミス
- 計画外作業→生産管理のミス
- 手順の不備→管理者の教育不足
など、人材教育の不備にすべての責任があるとは限らないのが現状です。
完全自動化されていない工場では、ほぼすべての工程で人が関わることが想定されます。そのため、あらゆる事故の要因を“ヒューマンエラー”と結論付けてしまうことは可能です。
しかし、ヒューマンエラーの原因は人材だけにあるわけではなく、社内体制や管理体制にある場合には、問題が改善することありません。この場合、根本的な対策を打つことができないため、同じ間違いや問題がいつまでも改善されないという悪循環に陥ります。
品質不良を可能な限り防止する対策とは
品質不良を防止する方法は、不良とならないための製品作りをする必要があります。
そのため、ルール作り、体制作り、システムの導入、などを実施し、極力ミスが起きない環境をつくりましょう。では、それぞれの項目をみていきます。
ルール作り
不良が起きる原因は、人・設備・材料・方法に分かれます。加えて、設備を使用して生産していたとしても人が管理する必要があります。そのため、人による管理を徹底することからスタートしましょう。例えば、品質管理マニュアルを作り、基準を設定。手順なども定め、設計や製造の品質を比較するなどの対策が必要です。
体制作り
品質不良を防止する場合、維持管理や日常点検によって、異常発見が発生する前に対策しておくことが必要です。ヒューマンエラーの中でも知識や無理解が引き起こすものであれば、対策として
- 正確に伝わっているかを復唱や提示で確認
- 曖昧なことが聞きにくい雰囲気をつくらないよう、近づきやすい雰囲気を作る
- 伝え方に問題が生じることもあるため、図や動画などで正しい形を人材に伝える
などが考えられます。
システムの導入
システムとしてIoTやAIを導入する場合、人材に頼らない品質管理が可能となります。また、ヒューマンエラーも起こりにくいといえるでしょう。IoTやAIを導入した場合、製品不良分析、製品の追跡、可否の判断、などを自動的に行うことが重要です。
システムを導入する場合には、ヒューマンエラーは起きにくくなるものの、AIやIoTの仕組みを管理・理解する必要があります。ルールや体制作りの内容をデータとして共有し、品質不良を防ぎましょう。
生産計画のDXで品質不良の改善に成功した中小製造業の取り組み
熟練社員の持つ技術継承、品質保持や納期対応の安定化など、多くの中小・中堅工場が様々な課題に直面するなか、生産計画のDXを成功させ「残業削減」「納期遵守率」「不良品率」を大幅に改善させた企業もあります。生産計画DXを成功させた中小・中堅工場は、どのような取り組みをおこなったのか。
株式会社スカイディスクはこれまで100社以上の生産計画のDX支援実績をおこない、計画工数の削減や納期遅延の解消などを実現してきました。様々な取り組みの中から、業績改善に成功した中小製造業事例を無料で公開しています。さらに、そのうえで活用される生産スケジューラを選ぶ際のポイントについてもご紹介していますのでぜひご活用ください。
\この資料でわかること/
・生産計画DXによる中小製造業の成功事例集
・AIを活用した生産計画の可視化支援サービス「最適ワークス」とは
・最適ワークスが選ばれる理由、生産スケジューラとの比較資料付き
一般的な品質不良対策とその限界
前述の通り、品質不良対策として、ルール作り、体制作り、システムの導入などがあげられます。ただし、これらの対策をしても限界があるケースもあるでしょう。
例えば、品質管理マニュアルを作り、作業チェックシート、承認フローを新たに設け、システムを活用して人が頭を悩ませる箇所を減らしたとしても、まだ品質不良が発生するという工場は多くあります。
品質不良がなくならない工場の特徴
つまり、これまでの工場運営方法では、いかに現場が工夫しようとも不良品率が下がらない状態が常態化していることになります。では、品質不良がなくならない工場の特徴とは何でしょうか。
製造現場に余裕がない
品質不良がなくならない工場の特徴として、現場に余裕がないことが挙げられるでしょう。ニーズが多様化している現状において、多くの工場が少量多品種の製品体制へと移行してきているのが実情です。そういった工場では、一日に何回も段取り替えを行い、複数の製品を順次製造していくことが一般的です。すると、生産量が変わらないにもかかわらず、日々の業務で要求される作業工数は増える一方となり、現場の作業負荷が増大します。
熟練工の減少
また、働き手の変化も考慮すべき要因です。これまで現場を支えてきた熟練工が定年退職などで減っていく中で、多くの工場において派遣人材の登用、あるいは海外技能実習制度の活用などを通して人材を確保しています。これらの人材は熟練工との比較では相対的にスキルや経験値は低く、効率的な生産活動のためには、より具体的かつ的確な指示が必要です。
ムリのない生産計画で不良品率を削減
こういった状況への対応として、生産計画内のムリを減らしていくことが考えられます。生産計画にムリがあると、不良品率は悪化する傾向にあります。
生産計画のムリによる品質不良
例えば、さまざまな製品を製造しなければならず、「標準的には30分かかる業務を20分で終わらせて次の作業へ移行する」という計画を立てたとします。
作業者は一つ目の作業を完了させた段階で、計画から既に10分遅れてしまいます。すると、焦って遅れを取り戻そうとすることから作業ミスが発生し、不良品が発生する、といった状況となりがちです。
特に現場作業者のスキルが低い状況では、こういった課題が顕在化しやすくなります。
生産計画にムリが生まれる理由
短納期
製品点数が増え、どの製品の納期も短納期であるときに計画を立案すると、どうしてもムリを織込んでしまうのは人の性ではないでしょうか。
楽観バイアス
加えて、繁忙時には、例えば熟練工のAさんはこれくらいでやっているから、他の人でも同じくらいの時間でできるだろう、といった、楽観バイアスも非常に入りやすい状況と言えます。
生産計画立案をシステム化してムリをなくす
こういう状況では生産計画の立案をシステム化し、客観的に実現できる生産計画を作り運用する体制へと移行することも解決策の一つではないでしょうか。
生産計画の立案をシステム化するメリットは多くあげられますが、その一つが生産計画の客観性や妥当性の担保にあるでしょう。
例えば、システム上一つの作業を30分、と入力すれば、それは現場の繁閑に関わらず30分で実行されるタスクとしてシステムには認識され、計画の立案がなされることとなります。こうすることで、人が特に繁忙期に持ちがちな楽観バイアスを計画上から排除することが可能となります。
実際に生産計画のシステム化に成功した企業では、このメリットを挙げる声が多く聞かれます。
まとめ
品質不良が発生することは、売上につながらない製造をしてしまうことでもあり、原材料費が無駄になる事に加え、その製造にかかった人件費も無駄になってしまうことを意味します。利益率を改善していくことを考えても、品質不良は当然減らしていくべきですが、現場任せの努力には限界があるのが実情です。
そういった状況では経営陣が率先して、生産計画という、現場業務の計画書の作成をシステム化することも一案でしょう。システムを活用することで、人が計画を立案することにより入り込んでしまう「ムリ」や「想い」を計画から省いてあげることができます。こういった努力により、不良品率を改善させることができるかもしれません。
業務を効率化して不良品率も削減、生産計画DXなら「最適ワークス」
業務を効率化したい、不良品率を削減したいといったお悩みがある方は、「最適ワークス」を是非ご検討ください。最適ワークスの魅力は、そのコストパフォーマンス、迅速な導入、使いやすいシンプルな画面UI、手厚いサポート体制です。月額15万円という手頃な価格で、AIによる高度な最適化ソリューションを利用できるのは大きなメリットです。クラウドサービス(Saas)であるため、初期のハードウェア投資や複雑なシステム構築が不要で、導入スピードも非常に速いです。これにより、時間とリソースを節約し、迅速に業務改善を開始できます。
シンプルで直感的な画面UIは、特別な技術知識がなくても誰でも簡単に操作でき、誰でもスムーズに利用できます。また、カスタマーサクセスチームがユーザーと伴走し、最適ワークスを最大限に活用できるようサポートします。導入後も手厚いサービスを提供し、ビジネスの課題解決に直結した支援を行います。
低コストでありながら高機能、そしてサポート体制も充実しているため、DXや業務改善の第一歩として優れたサービスとなっています。
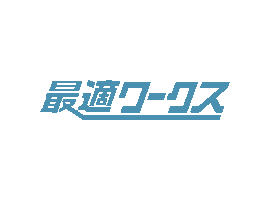
AIが生産計画を自動立案!生産計画・管理のDXを支援する製造業向けSaaS。工場の生産キャパ・製造進捗を可視化。納期回答の精度向上、残業時間を削減など中小・中堅工場での業績改善をサポート。専任エンジニア不要で使える!圧倒的コスパを実現。
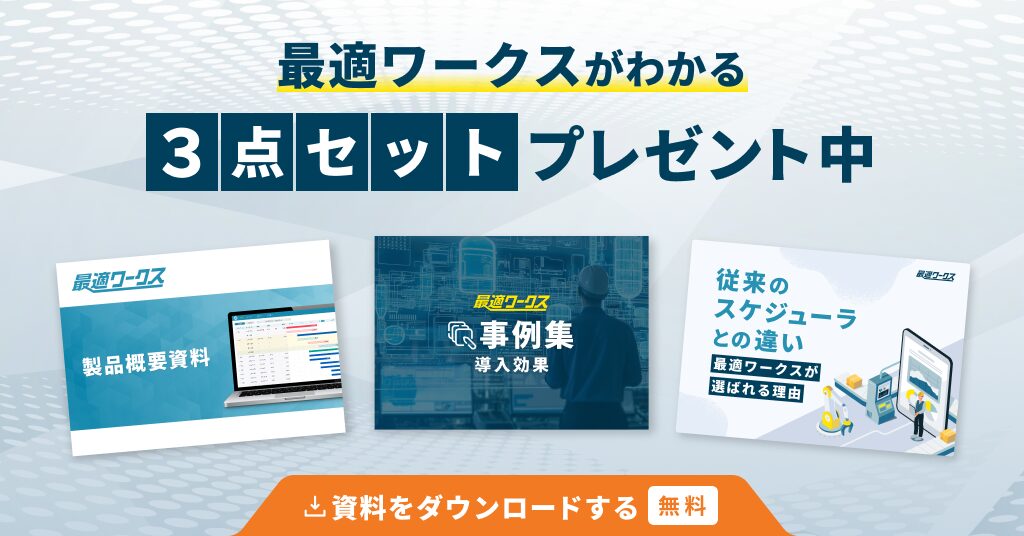