- コラム
製造業におけるPDCAサイクルの重要性と実践方法:変化に強い組織を作るための継続的改善
製造業は、常に品質向上とコスト削減という二つの大きな課題に直面しています。グローバル化の進展、技術革新の加速、そして顧客ニーズの多様化といった変化の激しい市場環境においては、これらの課題を解決し、競争優位性を確立するためには、継続的な改善が不可欠です。
そこで改めて見直したいのが「PDCAサイクル」です。本記事では、製造業におけるPDCAサイクルの重要性と実践方法について、具体的な事例を交えながら詳しく解説します。PDCAサイクルを理解し、実践することで、変化に強い組織を作り上げ、持続的な成長を実現しましょう。
PDCAとは?基本概念と目的
PDCAサイクルは、Plan(計画)、Do(実行)、Check(評価)、Action(改善)という4つのステップを繰り返すことで、業務プロセスを継続的に改善していくためのフレームワークです。
PDCAサイクルは、アメリカの統計学者であるW.エドワーズ・デミング博士によって提唱された製造業における品質管理の手法ですが、その後、経営管理全般に用いられるようになりました。その定義は、以下の4つのステップを繰り返すことで、業務プロセスを継続的に改善していくというものです。
- Plan(計画): 目標を設定し、その目標を達成するための戦略を立案します。
- Do(実行): 計画に基づいて、試験的な取り組みを実行します。
- Check(評価): KPI(重要業績評価指標)を活用して、実行結果をデータに基づいて分析・評価します。
- Action(改善): 評価結果に基づき、改善策を立案し、必要に応じて計画を修正します。改善策を実行し、標準化することで、PDCAサイクルを次の段階に進めます。
PDCAとOODAの違い
近年、変化への対応力を高めるためのフレームワークとして、OODA(ウーダ)ループが注目されています。OODAとは、Observe(観察)、Orient(状況判断)、Decide(意思決定)、Act(行動)の頭文字をとったもので、状況の変化に迅速に対応するための意思決定プロセスです。
OODAは、変化の激しい状況下での迅速な意思決定に強みを発揮しますが、PDCAのように継続的な改善を目的とした体系的なフレームワークではありません。
比較項目 | PDCAサイクル | OODAループ |
目的 | 継続的な改善、品質向上、効率化 | 迅速な意思決定、状況への適応 |
重点 | 計画性、データ分析、標準化 | 状況認識、即応性、柔軟性 |
環境 | 安定した環境、予測可能な状況 | 変化の激しい環境、予測不可能な状況 |
メリット | 着実な改善、品質の安定化、コスト削減 | 迅速な意思決定、競争優位性の確保 |
デメリット | 変化への対応が遅れる可能性、形式主義に陥る可能性 | 計画性に欠ける可能性、経験に依存する可能性 |
製造業においては、PDCAサイクルによる継続的な改善を基本としつつ、状況に応じてOODAループを活用するハイブリッドなアプローチが有効です。例えば、通常時はPDCAサイクルで品質管理や生産効率の改善を行い、突発的なトラブルが発生した場合はOODAループで迅速に対応するといった使い分けが考えられます。
製造業におけるPDCAの活用事例
(1) 生産管理の改善
- Plan: 需要予測を行い、生産計画を立案します
- Do: 製造ラインを最適化し、設備の稼働状況をモニタリングします
- Check: KPI(生産量、不良品率、稼働率など)を分析し、目標達成度を評価します
- Action: ボトルネックとなっている工程を特定し、設備の増強、人員配置の見直しなどの対策を実施します
(2) 品質管理への応用
ISO9001などの品質基準に基づき、PDCAサイクルを回すことで、品質の安定化を図ることができます。
- Plan: 品質目標を設定し、品質管理計画を策定します
- Do: 工程ごとの品質検査を実施し、データを収集します
- Check: 収集したデータを分析し、品質上の問題が発生していないか確認します。問題がある場合には発生原因を特定します
- Action: 品質問題の発生原因を特定し、再発防止策を講じます
(3) コスト削減と効率化
- Plan: コスト削減目標を設定し、具体的な削減計画を立案します
- Do: 省エネ活動の実施、原材料の調達コスト削減、生産工程の効率化など、様々なコスト削減策を実行します
- Check: コスト削減効果を測定し、目標達成度を評価します
- Action: コスト削減効果の低い施策を見直し、新たな削減策を検討します
PDCAを定着させるためのポイント
PDCAサイクルを定着させるためには、組織全体での取り組みが重要です。以下のポイントを押さえ、継続的な改善文化を醸成しましょう。
- 目標設定の明確化(SMARTの法則):具体的に(Specific)、測定可能に(Measurable)、達成可能に(Achievable)、関連性があり(Relevant)、時間制約がある(Time-bound)目標を設定します
- データドリブンなアプローチ(KPI・BIツール活用):KPIを設定し、BI(ビジネスインテリジェンス)ツールなどを活用して、客観的なデータに基づいて評価・分析を行います
- 組織全体での意識改革と教育:PDCAサイクルの重要性を理解させると同時に、目的を共有し、実践的なスキルを習得させるための教育を継続的に行います
- PDCAのスピードと柔軟性の最適化:状況に応じてPDCAのサイクルを速くしたり、遅くしたり、柔軟に対応できる体制を構築します
- 成功事例の共有と標準化:成功事例を組織全体で共有し、ベストプラクティスを標準化することで、改善活動の水平展開を図ります
PDCAの失敗要因とその対策
PDCAサイクルを活用するにあたり、陥りやすい失敗要因とその対策を理解し、PDCAサイクルを効果的に運用しましょう。
Planでの失敗要因:目標設定が曖昧で戦略不明瞭
- 失敗例
- 目標設定が曖昧:「生産性を向上させる」という目標だけを掲げ、具体的な数値目標や達成期限を設定しなかったため、何をもって生産性が向上したのか判断できなかった。
- 戦略不明瞭:「コスト削減に取り組む」という目標に対し、具体的なコスト削減戦略を立案しなかったため、現場は何をすれば良いのか分からず、手当たり次第に削減策を実行し、かえって品質を低下させてしまった。
- 対策
- SMARTの法則に基づいた目標設定:「来年度末までに、A製品の生産性を10%向上させる」というように、具体的な数値目標と達成期限を設定する。
- 具体的な戦略立案:「コスト削減のために、原材料の調達コストを5%削減する」「工程を見直し、無駄な作業を20%削減する」など、具体的な戦略を立てる。
Doでの失敗要因:実行計画が現場(実態)と合っていない
- 失敗例
- 現場の意見を聞かずに、トップダウンで新しい作業手順を導入したため、現場の作業員は反発し、計画通りに実行されなかった
- 新しい設備を導入したが、前後の工程がボトルネックになり、全体の製造量は対して変わらず期待していた効果が得られなかった
- 対策
- 現場への十分な説明と理解:新しい作業手順を導入する前に、現場の作業員と意見交換会を開催し、改善点や懸念点をヒアリングする
- 実態にあった実行計画:新しい設備を導入する前に、現状の状態を可視化し、ボトルネックを把握した上で導入効果をシミュレーションする
Checkでの失敗要因:定量評価なく形骸化
- 失敗例
- 新しい作業手順を導入した後、効果測定を行わなかったため、実際に生産性が向上したのか、作業員の負担が増加したのかを客観的に判断できなかった。
- 定期的な進捗状況の確認を行わず、PDCAサイクルが形骸化してしまい、改善活動が停滞してしまった。
- 対策:
- KPI設定:新しい作業手順導入後、1週間ごとの生産量、不良品率、作業員の残業時間などをKPIとして設定する。
- データ収集・分析:設定したKPIのデータを定期的に収集し、グラフ化するなどして、変化を把握する。
- 客観的な評価:収集したデータに基づき、新しい作業手順の導入によって生産性が向上したのか、作業員の負担が増加したのかを客観的に評価する。
Actionでの失敗要因:改善策が実行されない
- 失敗例
- データ分析の結果、問題点が明らかになったものの、具体的な改善策を実行する担当者が決まっていなかったため、何も改善されなかった。
- 改善策の実行期限を設定していなかったため、先延ばしにされ、結局実行されなかった。
- 対策
- 担当者の明確化:「〇〇工程の作業手順を見直す」という改善策に対し、担当者をAさんと明確に指名する。
- 期限の明確化:「〇〇工程の作業手順の見直しを、〇月〇日までに完了させる」というように、明確な期限を設定する。
- 進捗状況の定期的な確認:定期的に会議を開催し、改善策の進捗状況を確認する。
PDCAを成功させるためのポイント
PDCAサイクルを成功させるためには、以下の4つのポイントを意識しましょう。
- 「見える化」で計画を徹底する:計画内容を関係者全員が理解できるように、共有し、進捗状況を可視化します。
- 「習慣化」で定期的な評価を行う:定期的な評価をルーチンワークに組み込み、PDCAサイクルが形骸化しないようにします。
- 「根拠あり」で意思決定する:勘や経験に頼るのではなく、データに基づいた客観的な根拠に基づいて意思決定を行います。
- 「期限の明確化」で改善策を確実に実行:改善策の実行担当者と期限を明確にし、進捗状況を定期的に確認します。
DXによるPDCAサイクルの加速
PDCAサイクルは、製造業における継続的な改善活動の基盤ですが、DX(デジタルトランスフォーメーション)と組み合わせることで、その効果を加速させることができます。
生産計画システムによるPlan(計画)の精度向上
従来の生産計画は、過去のデータや経験に基づいた予測、いわゆる“熟練の勘”に頼ることが多く、不確実性が高いものでした。しかし、生産計画システムを導入することで、Planの精度が向上します。
DXによるDo(実行)の効率化と可視化
生産現場における様々な業務プロセスをDXにより効率化し、データを可視化することで、Doの質を高めます。例えば、下記のような活用が考えられます。
- IoTによるデータ収集:センサーやカメラなどのIoTデバイスを活用して、設備の稼働状況、作業者の行動、環境データなどを収集し、リアルタイムでモニタリングすることができます。
- RPAによる自動化:定型的な業務をRPAで自動化することで、人的ミスを削減し、生産性を向上させることができます。
データ活用によるCheck(評価)の高度化
DXで収集したデータや生産計画データを活用することで、Checkの精度と効率を大幅に向上させることができます。
- 計画の予実比較:生産計画システムの計画データと、DXで収集した実績データを組み合わせて比較することで、製造トラブルの早期発見と対応を可能にします
- KPIダッシュボードの構築:収集したデータをKPI(重要業績評価指標)として可視化し、目標達成度をリアルタイムでモニタリングできるダッシュボード構築します
Action(改善)の最適化と高速化
Checkで得られた情報に基づき、最適な改善策を立案したり、改善活動を検討したりすることができます。このときDXを進めておくことで、客観的なデータに基づいた改善活動を進めることができます。
- データに基づいた改善策:過去のデータを元に、設備のメンテナンス時期の最適化、作業手順の改善、在庫量などを検討することができます
- 対応の高速化:生産ラインの稼働状況や需要予測に基づき、スムーズに生産計画を調整することで、生産効率を最大化します
具体的な活用例
- 計画変動への迅速な対応:AI搭載の生産計画システムにより、自動的に生産計画を立案します。作業員の配置や設備の稼働状況を最適化することで、環境変化に迅速かつ柔軟に対応することができます。
- 品質不良の早期発見と原因特定:IoTセンサーが設備の異常を検知し、アラートを発します。不良品の発生原因を特定し、改善策を講じることで、品質不良の再発を防止します。
- サプライチェーン全体の最適化:サプライヤー、自社工場、顧客など、サプライチェーン全体のデータを連携させることで、需要予測、生産計画、在庫管理などを最適化し、リードタイムの短縮やコスト削減を実現します。
まとめ
PDCAサイクルは、製造業における継続的な改善の基本ツールです。さらに、生産計画システムなどをはじめ、DX活用を効果的に組み合わせることで、より迅速かつ効果的な改善サイクルを回し、競争力を高めることが可能です。
データを活用しながら、PDCAサイクルを回す文化を定着させることが重要です。まずは小さくPDCAを回し、成功事例を積み重ねることで、組織全体の改善能力を高めていきましょう。
生産管理でDXを始めるなら生産スケジューラ「最適ワークス」がおすすめ
生産管理で起点となるのが生産計画です。DXを始めるならまずは生産計画から始めることがおすすめです。生産スケジューラの導入費用をもっと抑えたい、可能な限り早く導入したい、導入後に使いこなせるか不安、といったご不安がある方は、「最適ワークス」も是非ご検討ください。最適ワークスの魅力は、そのコストパフォーマンス、迅速な導入、使いやすいシンプルな画面UI、手厚いサポート体制です。月額15万円という手頃な価格で、AIによる高度な最適化ソリューションを利用できるのは大きなメリットです。クラウドサービス(Saas)であるため、初期のハードウェア投資や複雑なシステム構築が不要で、導入スピードも非常に速いです。これにより、時間とリソースを節約し、迅速に業務改善を開始できます。
シンプルで直感的な画面UIは、特別な技術知識がなくても誰でも簡単に操作でき、誰でもスムーズに利用できます。また、カスタマーサクセスチームがユーザーと伴走し、最適ワークスを最大限に活用できるようサポートします。導入後も手厚いサービスを提供し、ビジネスの課題解決に直結した支援を行います。
低コストでありながら高機能、そしてサポート体制も充実しているため、DXや業務改善の第一歩として優れたサービスとなっています。
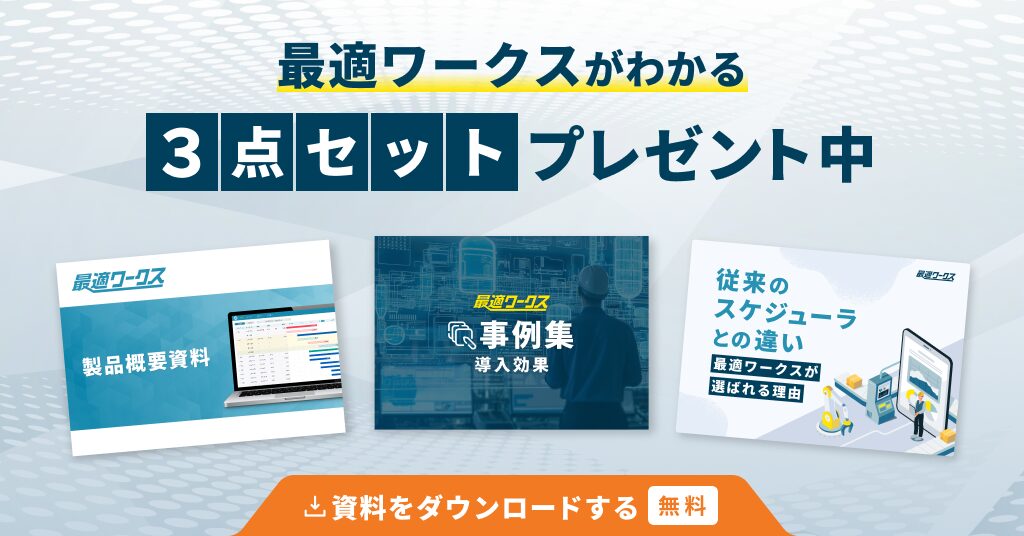