- コラム
かんばん方式とは?製造業で在庫削減・現場改善を実現する仕組みと導入方法
「在庫が多すぎて管理が煩雑」「ベテラン頼みの現場をなんとかしたい」「ムダな工程で生産が止まる」──そんな悩みを持つ製造業の方も多いのではないでしょうか。こうした現場の課題を根本から改善するヒントが、トヨタ生まれの生産方式「かんばん方式」にあります。本記事では、かんばん方式の仕組みや導入ステップ、メリット・デメリット、そしてDXとの連携事例までをわかりやすく解説。自社の生産性向上に役立つ実践知をお届けします。
かんばん方式とは?製造現場のムダを減らす仕組み
かんばん方式の基本概念
かんばん方式は、トヨタ自動車が開発した生産管理手法で、「必要なものを、必要な時に、必要なだけ」生産することを目的としています。大量生産が前提の従来型の押し出し生産(プッシュ型)と異なり、かんばん方式は実際の使用や消費に応じて生産を行う「引き取り方式(プル型)」です。これにより、生産のムダや在庫のムダを徹底的に削減できます。
かんばん方式の仕組み
この方式では、「かんばん」と呼ばれるカードを用いて、部品や製品の生産・供給を管理します。現場では、後工程が部品や資材を使用すると、かんばんを使って前工程に補充を指示します。これにより、生産のタイミングと数量が自動的に制御されるため、無駄な生産や在庫が発生しにくくなります。
かんばん方式のメリット
在庫の最適化
かんばん方式の最大の魅力は、在庫を必要最小限に抑えられる点です。在庫を持ちすぎると、保管スペースの確保や在庫劣化リスクが発生しますが、かんばん方式であれば「今必要な分だけ」補充されるため、これらのリスクが大幅に減少します。特に高価な部品や劣化しやすい素材を扱う業種では、大きな効果を発揮します。
生産効率の向上
工程間の連携がスムーズになることで、作業者の待ち時間が減り、全体のリードタイムが短縮されます。かんばんを用いることで、作業のタイミングが視覚的に分かりやすくなり、工程間の意思疎通がスムーズになります。また、作業手順の標準化が進むため、属人化の解消にもつながります。
製造現場の見える化
かんばんは、現場に「今何が必要か」を明確に伝える役割も持ちます。どの部品が、どの工程で、どれだけ必要かが明示されることで、現場の進捗や課題が可視化されます。結果として、トラブルの予兆も早期に察知しやすくなり、問題解決のスピードが上がります。
かんばん方式のデメリット
欠品リスク
在庫を最小限に抑える反面、部品の納入が遅れたり、急な需要増に対応しきれない場合は、すぐに欠品が発生します。特にサプライヤーとの連携が甘いと、かんばん方式の効果が発揮されません。そのため、安定した供給体制を構築することが前提となります。
柔軟性の欠如
製品のバリエーションが多く、頻繁に生産順序が変わるような現場では、かんばん方式の運用が難しくなります。かんばんの種類や数量の管理も煩雑になりやすく、仕組みが複雑化することで逆に非効率になるリスクもあります。
運用の難しさ
導入初期は現場が混乱することも少なくありません。運用ルールの徹底や教育が不十分なまま導入すると、「かんばんが回らない」「誰が補充するのか分からない」といったトラブルが頻発します。従業員の理解と協力を得るための丁寧な準備と教育が欠かせません。
かんばん方式の導入ステップ
現状分析
まずは、自社の生産フローや在庫管理の現状を可視化し、どこにムダや課題があるのかを把握します。現状のリードタイム、工程ごとの作業量、在庫の回転率などを数値化することで、かんばん方式の導入効果を明確にすることができます。また、属人化している業務の洗い出しも同時に行うことで、スムーズな導入の準備になります。
試験導入
いきなり全体に展開するのではなく、一つのラインや一部の製品で小規模に試験導入するのが一般的です。これにより、運用上の課題や不具合を早期に発見でき、改善につなげることができます。現場スタッフの声を取り入れながら柔軟に制度設計を進めることが、成功への近道です。
全社展開
試験導入で効果と運用ノウハウが蓄積された後、徐々に対象範囲を広げていきます。あわせて、管理ルールの明文化や教育資料の整備も行い、誰でも同じ基準でかんばんを使える状態を目指します。紙のかんばんからスタートし、段階的に電子化するというステップも効果的です。
かんばん方式の成功事例
椅子メーカーの事例
ある中堅の椅子メーカーでは、組立と塗装工程にかんばん方式を導入した結果、約30%の在庫削減に成功しました。以前は担当者の勘と経験に頼っていた生産計画が、かんばんで明確化され、作業ミスや手戻りも減少。結果的に月間生産数も15%増加しました。
金属部品メーカーの事例
別の金属部品メーカーでは、かんばんとAIによる生産スケジューラを連携させたハイブリッド運用を実施。過去の生産データをAIが分析し、需要予測に基づいてかんばん数を最適化することで、リードタイム短縮と在庫圧縮を同時に実現しました。属人化も解消され、新人でもスムーズに業務を回せるようになっています。
かんばん方式と他の生産方式との違い
JIT(ジャスト・イン・タイム)との関係
かんばん方式は、JITの一部を構成する手法です。JITはより広い概念で、生産や納品のすべてを「必要な時に必要な量だけ」行う考え方であり、かんばん方式はそれを実現するための具体的なツールといえます。
MRP(資材所要量計画)との違い
MRPは、将来の需要を予測して生産・発注を管理する「プッシュ型」の手法です。一方、かんばん方式は「プル型」であり、現場の実需に応じて生産を行う点が大きく異なります。安定生産が前提のMRPに対し、変動に強いのがかんばん方式の特長です。
かんばん方式のデジタル化とDXの可能性
紙から電子へ進化するかんばん
従来のかんばんは、紙やカードを使用して運用されてきましたが、最近では「電子かんばん」への移行が進んでいます。これは、バーコードやQRコード、RFIDタグ、タブレットなどを活用し、リアルタイムで情報の更新・共有ができる仕組みです。電子化によって、かんばんの紛失や記載ミスといった課題も解消され、より正確で効率的な運用が可能となります。
AIと連携した需要予測の高度化
AIを活用すれば、過去の出荷履歴や生産実績から今後の需要を予測し、かんばんの枚数や補充タイミングを自動で最適化することができます。これにより、急な注文変更や繁忙期にも柔軟に対応できるようになり、欠品リスクをさらに低減することが可能です。特に多品種少量生産に対応する現場では、高精度な予測が大きな武器になります。
クラウド連携で工場間連携も強化
クラウドと連携したかんばん管理システムを導入すれば、本社、各工場、外注先との間で情報を即時に共有できるようになります。これにより、工場間の部品移動や在庫状況の把握がリアルタイムで可能になり、拠点をまたいだ生産最適化にもつながります。製造業全体のスマートファクトリー化に向けた重要な一歩と言えるでしょう。
まとめ
かんばん方式は、在庫のムダを省き、現場の流れを効率化するための有効な生産管理手法です。導入により、製造現場の見える化や属人化の解消が進み、全体の生産性向上が期待できます。ただし、かんばん方式は万能ではありません。安定した運用には、日々の生産計画の見直しや、AI・DXを活用した仕組みとの連携も欠かせません。現場改革の第一歩として、かんばん方式を導入し、自社に合った最適な生産体制を築いていきましょう。
生産計画の見直しなら、生産計画DX『最適ワークス』がおすすめ
生産管理の起点となるのが「生産計画」です。DX(デジタルトランスフォーメーション)を始めるなら、まずはこの生産計画から取り組むことをおすすめします。
「生産スケジューラの導入費用をもっと抑えたい」「できるだけ早く導入したい」「導入後にきちんと使いこなせるか不安」といったお悩みをお持ちの方には、「最適ワークス」の導入をぜひご検討ください。最適ワークスの魅力は、コストパフォーマンスの高さ、迅速な導入、使いやすいシンプルな画面UI、そして充実したサポート体制にあります。月額15万円という手頃な価格で、AIによる高度な最適化ソリューションをご利用いただけるのは、大きなメリットです。
また、クラウドサービス(SaaS)で提供されているため、初期のハードウェア投資や複雑なシステム構築は不要です。そのため、導入スピードも非常に速く、時間とリソースを節約しながら、迅速に業務改善を始められます。シンプルで直感的な画面UIにより、特別なIT知識がなくても誰でも簡単に操作できます。また、カスタマーサクセスチームが導入後もユーザーに寄り添いながら支援し、最適ワークスを最大限に活用していただけるようサポートします。低コストでありながら高機能、そしてサポートも充実している最適ワークスは、DXや業務改善の第一歩として最適なサービスです。。
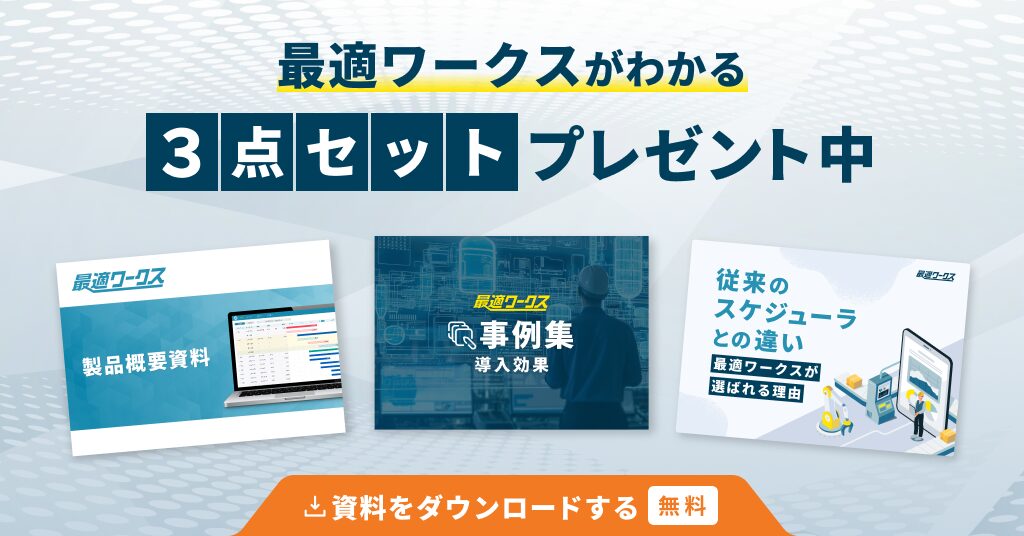