- コラム
製造業の「5S」と生産管理——生産性向上の基本とDXによる発展
製造業において、生産性向上は重要な課題です。その解決策として、長年にわたり支持され続けているのが「5S」活動です。製造現場の改善活動の基本であり、生産管理の根幹を支える重要な要素でもあります。本記事では、5Sの基本概念から具体的な取り組み、生産管理への効果、そしてDX(デジタルトランスフォーメーション)による発展について解説します。
5Sとは? 製造業が取り組むべき理由
5Sとは、製造業における職場環境の改善活動を表す標語で、「整理・整頓・清掃・清潔・躾」の5つの言葉の頭文字をとったものです。特に、「整理・整頓・清掃」を「3S」と呼びます。
- 整理(Seiri): 不要なものを処分し、必要なものだけを残す。
- 整頓(Seiton): 必要なものを使いやすいように配置する。
- 清掃(Seiso): 作業場を清潔に保つ。
- 清潔(Seiketsu): 整理・整頓・清掃の状態を維持する。
- 躾(Shitsuke): ルールを守り、自然と行動できるように習慣化すること。
5Sと生産管理の関係(生産計画・在庫管理・工程管理への影響)
5Sは、単なる清掃活動ではなく、生産管理と密接に関わっています。5S活動を通じて、生産計画、在庫管理、工程管理など、生産管理の各プロセスを最適化することができます。
- 生産計画への影響:整理・整頓により、不要な在庫や作業の可視化が進み、正確な生産計画の策定が可能になります。
- 在庫管理への影響:不要な在庫の削減、定位置管理の徹底により、在庫管理コストの削減、保管スペースの有効活用につながります。
- 工程管理への影響:作業場の整理・整頓、作業手順の標準化により、ムダな動きを排除し、工程全体の効率化を図ることができます。
5Sの導入で得られるメリット
5Sを導入することで、製造現場は様々なメリットを享受できます。
- 生産性の向上:ムダの排除、作業効率の改善、不良品の削減など、生産性向上に直結する効果が期待できます。
- 品質の向上:作業環境の改善、異常の早期発見により、品質不良の発生を抑制できます。
- 安全性の確保:危険箇所の改善、通路の確保などにより、労働災害の防止につながります。
- コストの削減:ムダな在庫の削減、不良品の減少、設備の長寿命化など、コスト削減効果も期待できます。
- 従業員のモチベーション向上:清潔で快適な職場環境は、従業員のモチベーション向上に貢献します。
- システム導入が円滑になる:整理整頓された環境は、データ収集を容易にし、例えば、生産管理システム(MESやERP)との連携もスムーズにします。
- 企業イメージの向上:整理整頓された工場は、顧客や取引先からの信頼を得やすく、企業イメージ向上につながります。
5Sの基本概念と具体的な取り組み
5S活動は、以下の5つの段階に分けられます。それぞれの段階における基本的な概念と具体的な取り組みについて解説します。
①整理(Seiri)
必要なものと不要なものを区別し、ムダを削減
整理とは、作業場所にあるものを「必要なもの」と「不要なもの」に分け、不要なものを処分することです。判断基準は、一定期間使用していないもの、今後使用する見込みのないものを不要と判断します。
具体的な取り組み
- 赤タグ作戦:作業場所にある不要と考えられる工具、部品類に赤タグを付け、使ったときに赤タグを外す。一定期間使用されなかったものは処分する手法
- 在庫の棚卸し:在庫を徹底的に棚卸しし、滞留在庫や不良在庫を洗い出す。
- 保管場所の整理: 保管場所にある不要なものを処分し、スペースを確保する。
不要な在庫や作業の可視化が生産計画の精度向上につながる
整理を徹底することで、不要な在庫や作業が可視化され、生産計画の精度向上につながります。例えば、滞留在庫が明らかになれば、過剰な生産を抑制し、在庫コストを削減することができます。
②整頓(Seiton)
物の定位置管理と標準化
整頓とは、必要なものを使いやすいように配置することです。物の定位置や置き方を決め、誰でもすぐに取り出せるように、表示や色分けなどの工夫を施します。
具体的な取り組み
- 物の定位置を決める:工具、部品、書類など、すべてのものに定位置・定量を決め、表示を明確にする。
- 物の配置を改善する:作業動線を考慮し、必要なものがすぐ手に届くように配置を改善する。
- 標準化:工具や部品の置き方、作業手順などを標準化し、誰でも同じように作業できるようにする。
生産ラインや倉庫の整備が作業の流れをスムーズにする
整頓された生産ラインや倉庫は、作業の流れをスムーズにし、作業効率を向上させます。例えば、工具が定位置に置かれていれば、探す手間が省け、作業時間を短縮することができます。
③清掃(Seiso)
作業場を清潔に保ち、異常を早期発見
清掃とは、作業場を常に清潔に保つことです。清掃は、単にゴミを取り除くことだけでなく、設備の点検やメンテナンスも兼ねています。
具体的な取り組み
- 清掃分担を決める:作業場所ごとに清掃担当者を決め、責任を明確にする。
- 清掃用具を準備する:必要な清掃用具を準備し、すぐに清掃できるようにする。
- 清掃チェックリストを作成する:清掃項目を明確にしたチェックリストを作成し、定期的に清掃状況を確認する。
設備の異常検知が生産ラインのトラブル防止につながる
清掃を徹底することで、設備の異常を早期に発見し、生産ラインのトラブルを未然に防ぐことができます。例えば、油漏れや異音などを早期に発見し、修理することで、設備の故障による生産停止を防ぐことができます。
④清潔(Seiketsu)
3Sを維持するための標準化とルールづくり
清潔とは、整理・整頓・清掃の状態を維持するための活動です。そのための仕組みをつくり徹底することで、職場を正常な状態に維持することができます。
具体的な取り組み
- ルールを作る:整理・整頓・清掃に関するルールを明確に定め、周知徹底する。
- チェックリストを作成する:状態を定期的に確認するためのチェックリストを作成し、運用する。
- 定期的なパトロールを実施する: 5Sの状態を定期的にパトロールし、改善点を見つける。
仕組み化により、生産管理の安定化が実現
清潔を徹底することで、作業環境が常に一定の状態に保たれ、生産管理の安定化につながります。例えば、工具が常に同じ場所に置かれていることで、作業者は迷うことなく作業に取りかかることができ、作業効率が向上します。
⑤躾(Shitsuke)
5Sの定着を促すための教育・訓練
躾とは、決められたルールを守り、習慣化することです。5Sを継続的に実践するためには、従業員への教育・訓練が不可欠です。
具体的な取り組み
- 5Sに関する教育・訓練を実施する:5Sの目的や方法を従業員に理解させ、実践できるように教育・訓練を行う。
- 5S活動の成果を評価する:5S活動の成果を定期的に評価し、従業員のモチベーションを高める。
- 5S優秀事例を表彰する:5S活動で優れた成果を上げた事例を表彰し、他の従業員の模範とする。
生産管理のKPI(重要業績指標)と結びつけることで、継続しやすくなる
5S活動を生産管理のKPIと結びつけることで、5Sの重要性を従業員に認識させ、継続的な実践を促すことができます。例えば、5S活動の成果を不良率の低下や生産性の向上といったKPIで評価することで、5S活動のモチベーションを高めることができます。
5Sがもたらす生産管理への効果
5Sは、生産計画の精度向上、工程管理の最適化、設備管理の強化、トレーサビリティの向上など、生産管理の様々な側面に効果をもたらします。
生産計画の精度向上(不要な在庫の削減、作業効率の向上)
整理・整頓により、不要な在庫の削減、作業効率の向上につながり、生産計画の精度が向上します。不要な在庫が減ることで、保管スペースの有効活用、在庫管理コストの削減が可能になります。また、作業効率が向上することで、リードタイムの短縮、納期遵守率の向上につながります。
工程管理の最適化(ムリ・ムダ・ムラの削減)
5Sは、工程管理における「ムリ・ムダ・ムラ」を削減し、工程全体の最適化に貢献します。整理・整頓により、作業場所のスペースが確保され、作業者の移動距離が短縮されます。また、標準化により、作業手順が明確になり、作業時間の短縮、品質の安定化につながります。
設備管理の強化(異常検知によるダウンタイム削減)
清掃を徹底することで、設備の異常を早期に発見し、ダウンタイムを削減することができます。設備の異常を早期に発見することで、故障を未然に防ぎ、設備の寿命を延ばすことができます。また、定期的なメンテナンスを実施することで、設備の性能を維持し、安定した生産を可能にします。
トレーサビリティの向上(整頓された環境で記録が明確に)
整頓された環境では、書類や記録が整理されており、トレーサビリティが向上します。製品の製造履歴や検査記録などが容易に追跡できるようになり、品質問題が発生した場合の原因究明を迅速に行うことができます。
間違った5S活動によるデメリット
間違った5S活動は、効果が得られないどころか職場に悪影響を及ぼすことがあります。
- 形式主義・表面的な活動:目的を理解せずに「掃除する」「物を揃える」といった形式的な活動に終始すると、効果が薄く、モチベーションが低下しやすくなります。すると、一時的な改善にとどまり、すぐに元の状態に戻ってしまいます。
- 過剰な整理・整頓:「とにかく物を減らす」ことに固執すると、必要なものまで処分してしまったり、細かすぎる整理整頓の管理により、作業効率が悪化することもあります。
- 清掃活動の負担増加:清掃活動に時間をかけすぎると業務を圧迫し、負担の偏りが不公平感を生むこともあります。
- ルール遵守の強制による弊害:ルールを厳格にしすぎると柔軟性を失い、改善提案が出にくくなり、職場の雰囲気が悪化する原因になります。
こうした問題を防ぐには、目的を明確にし、従業員と共有することが重要です。ルールは柔軟に運用し、PDCAサイクルを回して継続的に改善することで、5Sを効果的に活用できます。
5Sを成功させるためのポイント
5Sを成功させるためには、以下のポイントを押さえることが重要です。
- 5Sの目的を明確にし、従業員と共有する:5Sの目的を明確にし、従業員全員が理解し、共感することが重要です。
- 業務の可視化を徹底する(チェックリストやデジタルツールの活用): チェックリストやデジタルツールを活用し、業務の可視化を徹底することで、問題点や改善点を見つけやすくなります。
- 生産管理と連携し、5Sを「単なる清掃活動」に終わらせない:5Sを生産管理と連携させることで、5S活動が生産性向上にどのように貢献しているかを可視化し、継続的な改善を促します。
5S×DX(デジタル技術)の活用
DX(デジタルトランスフォーメーション)とは、IT技術を用いて業務プロセスを改革し、新たな価値を生み出すことを指します。近年では、デジタル技術を活用することで、5S活動をより効率的に、効果的に進めることができます。
在庫・物品管理のデジタル化(整理のDX)
製品、部品、工具などにRFIDタグやバーコードを付与し、在庫状況をリアルタイムで把握します。これにより、過剰在庫や滞留在庫を可視化し、不要なものを効率的に処分できます。また、各部署が保有する物品をデジタル台帳で一元管理することで、物品の所在や利用状況を把握し、重複購入や無駄な物品の保管を防止できます。
さらに、在庫・物品管理システムのロケーション管理機能を活用し、工場内のレイアウトをデジタルマップで視覚化することで、物品の配置場所を明確にすることができます。
作業手順のデジタル化(整頓のDX)
例えば、AR(拡張現実)技術を活用し、備品の配置場所をスマートグラスやタブレットの画面上にリアルタイムで表示することで、必要な工具を素早く見つけ、使用後に元の場所に戻すことを徹底します。
さらに、AR/VRを活用した作業支援では、作業手順を視覚的に表示し、作業者の習熟度向上を支援するとともに、使用した備品の正しい配置を自動でチェックし、配置ミスがあった場合はリアルタイムでアラートを表示し修正を促します。
作業者は指示された場所に誘導されるため、迷うことなく迅速に備品を配置・回収でき、探し物の時間を大幅に削減し、整頓作業全体の効率を向上させます。
ペーパーレス化(整理・整頓のDX)
書類を電子化し、クラウド上に保存することで、物理的なスペースを削減し、必要な情報を迅速に検索できるようにします。
5S活動のデジタルチェック(清掃・清潔のDX)
IoTセンサーを活用し、清掃や点検を自動化することで人的コストを削減し、より効率的な5S活動を実現できます。また、5Sチェックリストをモバイルアプリで運用し、監査結果をリアルタイムで共有することで、監査業務を効率化し、改善活動を迅速に進めることが可能です。
動画マニュアル(躾のDX)
作業手順やルールをデジタル化することで標準化を促進できます。例えば、作業手順を動画マニュアルとして作成し、タブレットなどで閲覧できるようにすることで、作業者の習熟度向上とともに、5S活動の徹底を支援します。
これらのデジタル技術を活用することで、備品の整頓は単なる清掃活動ではなく、データに基づいた効率的な業務プロセスへと進化します。従業員の負担を軽減し、安全性を向上させながら、より生産性の高い職場環境を実現できます。
生産計画が5S活動による生産性向上につながった事例
事例:計画データの可視化により、保管スペースの見直しと生産効率を改善
ある電器メーカーにおける、生産計画システム導入を起点とした5S活動の成功事例をご紹介します。この企業では、生産計画のシステム化によって可視化されたデータを分析した結果、特定の工程で計画よりも時間がかかっていることが判明しました。
担当者が原因究明のため、現場にヒアリングを行ったところ、意外な事実が明らかになりました。 その工程によって発生する仕掛かり在庫の保管スペースが不足しており、一日に実施できる回数に制限がある状況だったのです。作業者は保管スペースがない状態で次の工程を進められず、結果として工程の遅延を引き起こしていました。
そこで、工場内のレイアウトを見直し、整理・整頓を徹底することで保管場所を広げることができました。その結果、生産性が向上しました。
生産計画システムは、単なる計画ツールではなく改善の起点になる
この事例からわかること
- 生産計画データは改善の起点となる:システム化によって可視化されたデータは、潜在的な問題を発見し、改善活動につなげるための重要な情報源となります。また、現場の声に耳を傾けることの重要性も示唆しています。システムのデータだけでは見えない現場の状況を把握することが、問題解決の鍵となります。
- 5Sは問題解決のための有効な手段:本事例では、整理・整頓を見直すことで、ボトルネックとなっていた保管スペースの問題を解決し、生産性向上を実現しました。
- システム化と5S活動の相乗効果:このように、生産計画システムの導入と5S活動を組み合わせることで、より効果的な改善活動を実現できます。
この電器メーカーの事例は、生産計画のシステム化をきっかけに、製造工程の中でボトルネックになっている部分を発見し、5S活動を通じて適切に解決できた好例と言えるでしょう。
まとめ
5Sは、製造業における生産性向上のための基本であり、生産管理と組み合わせることで最大限の効果を発揮します。DXを活用することで、5Sをより実践しやすく、効果的に進められるようになります。5Sの継続的な実践が、企業の競争力向上につながることを忘れてはなりません。
今後は、AIやIoTなどのデジタル技術の進化により、5S活動はさらに高度化していくことが予想されます。例えば、AIが作業者の行動を分析し、最適な作業手順を提案したり、IoTセンサーが設備の異常を自動的に検知したりすることで、より効率的で安全な作業環境を実現することができます。製造業は、常に変化する市場ニーズに対応し、競争力を維持・向上させるために、5S活動を継続的に実践し、改善していく必要があります。
生産管理でDXを始めるなら生産スケジューラ「最適ワークス」がおすすめ
生産管理で起点となるのが生産計画です。DXを始めるならまずは生産計画から始めることがおすすめです。生産スケジューラの導入費用をもっと抑えたい、可能な限り早く導入したい、導入後に使いこなせるか不安、といったご不安がある方は、「最適ワークス」も是非ご検討ください。最適ワークスの魅力は、そのコストパフォーマンス、迅速な導入、使いやすいシンプルな画面UI、手厚いサポート体制です。月額15万円という手頃な価格で、AIによる高度な最適化ソリューションを利用できるのは大きなメリットです。クラウドサービス(Saas)であるため、初期のハードウェア投資や複雑なシステム構築が不要で、導入スピードも非常に速いです。これにより、時間とリソースを節約し、迅速に業務改善を開始できます。
シンプルで直感的な画面UIは、特別な技術知識がなくても誰でも簡単に操作でき、誰でもスムーズに利用できます。また、カスタマーサクセスチームがユーザーと伴走し、最適ワークスを最大限に活用できるようサポートします。導入後も手厚いサービスを提供し、ビジネスの課題解決に直結した支援を行います。
低コストでありながら高機能、そしてサポート体制も充実しているため、DXや業務改善の第一歩として優れたサービスとなっています。
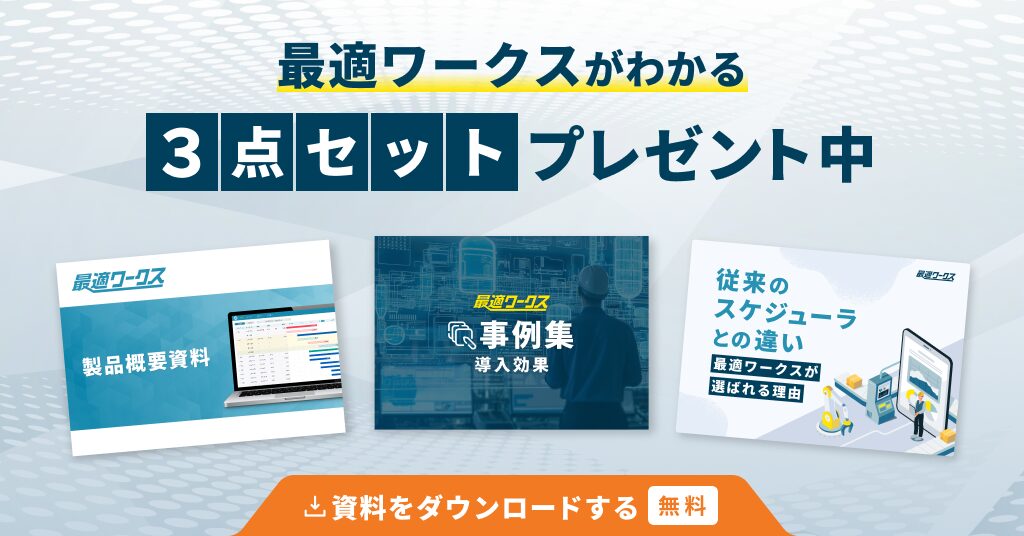