- コラム
見える化で実現する生産計画の効率化と稼働率向上~生産計画DXによる設備稼働カイゼン事例~
目次
- 成功事例:生産計画の効率化と稼働率向上
- 導入前の状況
- 最適ワークス導入の経緯
- 最適ワークス導入プロジェクトの全体像
- 導入後の成果
- (1)生産計画の対象範囲拡大と設備稼働率の向上
- (2)複雑な組み合わせをAIが自動計算
- (3)生産可能設備の明確化と仕掛かり在庫の減少
- (4)スタッフ稼働の最適化
- (5)計画と実績の比較により、改善活動の土台が構築
- まとめ
本セミナーでは、生産計画の立案を一度諦めた会社が、生産計画を再び立案できるようになり、さらに設備稼働率を向上させ、継続的な改善活動を行えるようになったのか、事例について詳しくご説明いたします。
ではまず、会社様の基本情報を先にお伝えさせていただきます。
成功事例:生産計画の効率化と稼働率向上
紹介する会社の基本情報
- 業種: 金属加工品製造
- 規模: 50名~100名
導入前の課題
この会社様は、生産計画において、以下の3つの課題を抱えていました。
(1)初工程のみの計画で全体の稼働状況が不明
全体で8工程あるにもかかわらず、最初の工程(初工程)しか計画立案ができておらず、他の工程では、投入順序のみを決めて作業をしていました。
全体の稼働状況が不明確なので、特定の設備が稼働していない場合でも「なぜ稼働していないのか」理由がわからないという問題がありました。また、設備負荷を考慮した計画はできていませんでした。
(2)計画は担当者の頭の中、生産プロセスの改善余地が不明
計画が見える化されていないことで、どの工程がボトルネックになっているのか、またはどの部分に効率化の余地があるのかといった情報を把握できませんでした。このため、「次に何をすれば生産量がアップするのか」「稼働率をどのように上げるべきか」といった具体的な改善活動が行えませんでした。
(3)稼働率が低い設備にも無駄なスタッフ待機が発生
先の予定が不明で、当日にならないと設備の稼働状況がわからない状況でした。そのため、稼働率の低い設備にも人員を待機させており、スタッフの人件費が無駄に発生することでコスト効率が悪化していました。
これらの3つの課題の根本原因は、「初工程だけに注目して計画を立てており、全ての工程を計画立案・可視化できていない」 ことにありました。
そもそも、全工程を計画作成できなかった理由
このお客様は、そもそもなぜ全工程での計画立案・可視化ができなかったのか。それは、次の特徴により「考慮すべき組み合わせが膨大で、人間の頭ではとても対応できない」状況になっていたことがわかりました。
- 設備の膨大な組み合わせ
汎用機が多く存在し、オーダーごとに「どの設備で」「どの順番で」作業を行うべきかの組み合わせが無数に存在することで、組み合わせを人の頭で考えるのが限界でした。 - 製品ごとの工程数の違い
製品群ごとに工程数が異なっており、計画の複雑性を増大させていました。 - 多品種少量生産
注文数が非常に多いため、一つ一つの注文に対して組み合わせを考慮する必要がありました。
これらの要因により、組み合わせの数が膨大になり、人間の手ではとても対応できない状況になっていたのです。
導入前の状況
導入前、このお客様の状況は非常にシンプルかつ課題が多いものでした。当初は、「計画も実績も収集していない」状態でした。注文が入るたびに材料を投入し、流れ作業で対応する「場当たり的」な運用が行われていました。
場当たり的な対応から抜け出すべく、まずは手作業での計画立案にトライしました。しかし、基準となる作業時間が不明だったので、まずは実績を記録する運用を開始。日報として「オーダーごとにどの設備で製造し、開始時間と終了時間が何時であったか」を記録しました。
この記録データを工場長がExcelで集計することにより、おおよその製品ごとの作業時間が見えるようになりました。しかし、それでも組み合わせの問題が残り、「人間の頭ではとても考慮できない」課題が解決できないままでした。
最適ワークス導入の経緯
こうした課題を解決するため、生産計画のシステム化を検討することになり、複数のシステムを比較検討。その結果、最適ワークスの導入を決定しました。導入の決め手は、主に以下の3点でした。
- 直感的な操作性
お客様はシステムを導入した経験がなかったため、製品画面を見た際の「操作が直感的でわかりやすい」と感じられた点が選定の決め手の一つでした。 - 安価で始めやすい費用体系
最適ワークスはSaaS型で月額料金制のため、初期費用を抑えられます。数千万円の投資が不要で、導入ハードルが低い点が評価されました。 - トライアンドエラーの容易さ
工程情報や作業時間のデータ設定を簡単に行え、計画と実績の差を検証しやすい点が評価されました。検証のサイクルをスムーズに繰り返すことで「計画作成の精度を高めやすい」というメリットを感じていただきました。
最適ワークス導入プロジェクトの全体像
ここからは、課題であった「全ての工程の計画を立案・可視化できなかった」という状況から、どのように解決したかの流れを紹介します。導入プロジェクトは、以下の4つのステップで進められました。
- ステップ1:基本操作習得
- ステップ2:計画立案と検証準備
- ステップ3:テスト運用
- ステップ4:本運用
最終的に、ステップ4では最適ワークスで立案した計画をもとに生産活動を行い、継続的に運用できる状態を実現しました。では、各ステップでの具体的な取り組みをご説明します。
ステップ1:基本操作習得
最初のステップでは、基本的な操作方法の習得にフォーカスしました。実施内容は以下の通りです。
- データ設定の練習
工場内の設備を1つ登録し、代表的な製品を1つ選んで登録。その製品に関わる工程を登録してデータを設定しました。 - 自動立案機能の使用
最小限のデータを設定した後、最適ワークスの「自動立案」ボタンを押すことで、計画を可視化。これにより、計画立案から可視化までの一連の操作を体験しました。
このプロセスは、カスタマーサクセス担当者とのウェブミーティングで画面を共有しながら進行。実際の操作を通して、基本的な使い方を習得していただきました。
ステップ2:工場内の設備・製品・工程のデジタル化
次のステップでは、工場全体の設備・製品・工程を最適ワークスに登録し、デジタル化を進めました。
- 全ての設備と製品の登録
ステップ1で登録した単一の設備・製品から拡張し、工場内の全ての設備と製品を登録しました。 - 工程の登録
各製品に対して、以下の情報を登録しました。- 工程名:どの工程かを明確化
- 使用する設備:工程がどの設備で生産できるかを指定
- 作業時間:各工程に必要な作業時間を設定
これらのデータは、導入前に収集していた実績データを基に登録されました。また、登録したデータを用いて試験的に計画を立案し、実績と比較を行いました。
課題の発生
この段階で、最適ワークス上の計画に「納期遅延が頻発している」ことが判明しました。しかし実際には納期遅延は発生していない状況であり、この差異の原因をステップ3で詳しく調査・解決していきました。
ステップ3:テスト運用
テスト運用のフェーズでは、実際に注文データを最適ワークスに登録し、計画と実績の差異を把握しました。
データ比較
最適ワークスで生成された計画の「生産数」「納期遵守率」と、実績データを比較したところ、次のことが判明しました。
- 生産数量は計画と実績で一致。
- 納期遵守率は、計画では90%に留まる一方、実際の現場では100%を達成している。
原因調査と改善
納期遅延が計画上で発生していた原因を調査したところ、一部の製品について登録した「作業時間」が実際の作業時間よりも長く設定されていたことが判明しました。そこで、最適ワークス上のマスターデータを修正します。修正後には、計画精度が向上し、実績と計画の差異が解消されました。
ステップ4:本運用
最終ステップでは、最適ワークスを基に生産活動を実際に運用し、継続的な改善が可能な状態を構築しました。
- 業務フローの確立
ステップ3で整理した業務フローを採用し、現場を巻き込みながら最適ワークスで作成した計画を運用しました。 - 全ての工程の計画立案・可視化の実現
設備、製品、工程をすべて登録したデータを基に、全工程の計画立案・可視化を達成しました。これにより、現場での生産活動が最適ワークスの計画に基づいて実施され、効率的な運用が可能となりました。
導入後の成果
このお客様では、様々な導入効果を実感いただいております。この「実感いただいた成果」について、いくつかご紹介します。最適ワークスの導入により、次の成果が得られました。
- 生産計画の対象範囲拡大と設備稼働率の向上
- 複雑な組み合わせをAIが自動計算
- 生産可能設備の明確化と仕掛かり在庫の減少
- スタッフ稼働の最適化
- 計画と実績の比較により、改善活動の土台が構築
(1)生産計画の対象範囲拡大と設備稼働率の向上
導入後の成果として、「生産計画の対象範囲拡大」が挙げられます。これまで初工程のみの計画しか立てられなかったのが、全工程の計画立案が可能となり、設備稼働率が向上しました。
導入前
導入前は、初工程以降の計画がなく、作業者は流れてくる「モノ」を見ながら、段取り回数を減らす方法を考えて作業していました。この「脳内での考慮」には限界があり、トラブルが発生していました。
導入後
全工程の計画を最適ワークスで立案できるようになり、作業者は事前に計画を確認できるようになりました。自分の担当する段取りを把握し、指示通りに準備を整えることで、設備稼働時間の無駄を減らし、稼働率が向上しました。
(2)複雑な組み合わせをAIが自動計算
この成果として、最適ワークスが組み合わせを考慮した全工程の計画を立案できるようになった点が挙げられます。
導入前
膨大な組み合わせを人が考慮するのは不可能でした。
導入後
製品と工程に関する全てのデータを設定することで、最適ワークスを活用し、AIに組み合わせの検討を任せられるようになりました。その結果、計画立案が可能となり、効率的な運用が実現しました。
(3)生産可能設備の明確化と仕掛かり在庫の減少
各製品の「生産可能な設備」を改めて言語化することで得られた成果です。この取り組みを通じて、従来「特定の設備でしか生産できない」とされていた製品が、実際には複数の設備で生産可能であることが判明しました。
導入前
最適ワークス導入前は、製造が行き当たりばったりで、設備稼働に偏りが生じており、それによって、仕掛かり在庫(中間在庫)が発生していました。
導入後
自社リソースを明確化したことで、設備稼働の偏りが解消され、仕掛かり在庫が減少。結果として、設備稼働率が向上しました。
(4)スタッフ稼働の最適化
計画の可視化により稼働状況が把握でき、従業員に「休んでも大丈夫」といった具体的な休暇指示が可能となりました。これにより、原価低減とともにスタッフのモチベーション向上にもつながりました。
導入前
計画が見えなかったため、「とりあえず出勤してもらう」運用が行われており、設備が稼働していない場合、担当者は作業がない状態になることもありました。この運用では余分な人件費や間接費が発生していました。
導入後
計画は約2週間ごとに立てられ、設備の稼働状況が事前に把握できるようになりました。稼働が少ない日は従業員に休暇を取ってもらう仕組みが構築され、人件費を含むコストの削減が実現しました。さらに、「メリハリのある働き方」により、スタッフのモチベーション向上にもつながりました。
(5)計画と実績の比較により、改善活動の土台が構築
計画と実績を比較できるようになり、改善活動の土台が整いました。これにより、課題を明確化し、改善策を講じる運用が可能となり、PDCAサイクルを継続的に回せるようになりました。
導入前
最適ワークス導入前は、計画自体が存在せず、実績だけがある状態でした。そのため、計画と実績を比較できず、改善活動も進められませんでした。
導入後
最適ワークスにより生産計画を立て、実績と比較する仕組みが整ったことで、改善活動のPDCAサイクルが回せるようになりました。また、設備や運用による改善策を講じることが可能になりました。
具体的には、このお客様は設備の老朽化に注目し、月単位で設備ごとの稼働時間を計画と比較しています。計画より進捗が遅れている場合、その原因が設備の老朽化によるものと推測されると、翌日以降に設備のメンテナンスを検討します。直近で設備メンテナンスの実施が難しい場合には、計画の作業時間を延ばすことで、計画の精度向上に対応しています。
まとめ
実施した内容
当初は、「初工程の計画しかない状態」から、最適ワークスの活用により全ての工程の計画立案が可能に。従来、人が対応できなかった複雑な組み合わせも、AIが自動で計画立案できるようになりました。
得られた成果
- 計画による生産性向上:事前準備が可能になり、設備稼働率がアップ
- 製品と設備の適正化:設備稼働の偏りや中間在庫が減少
- スタッフ稼働の最適化:休暇取得を促進し、人件費を抑制、従業員のモチベーション向上
- 計画と実績の比較による改善活動: 継続的な改善サイクルを確立
お気軽にお問い合わせください
導入企業様の事例を通して、多くの製造業企業様と共通する課題や近い状況があったのではないでしょうか。本日ご紹介した事例で使用されているのは、スカイディスクが提供する 「最適ワークス」です。これは、生産計画をシステム化し、AIが自動立案するサービスです。お客様が現場で実運用できる状態まで、弊社のカスタマーサクセスチームが伴走型でサポートさせていただいています。
もし「自社の課題も解決できるのか?」とご興味をお持ちいただけましたら、お気軽にお問い合わせください。本事例が、皆様の会社における課題解決のヒントになれば幸いです。
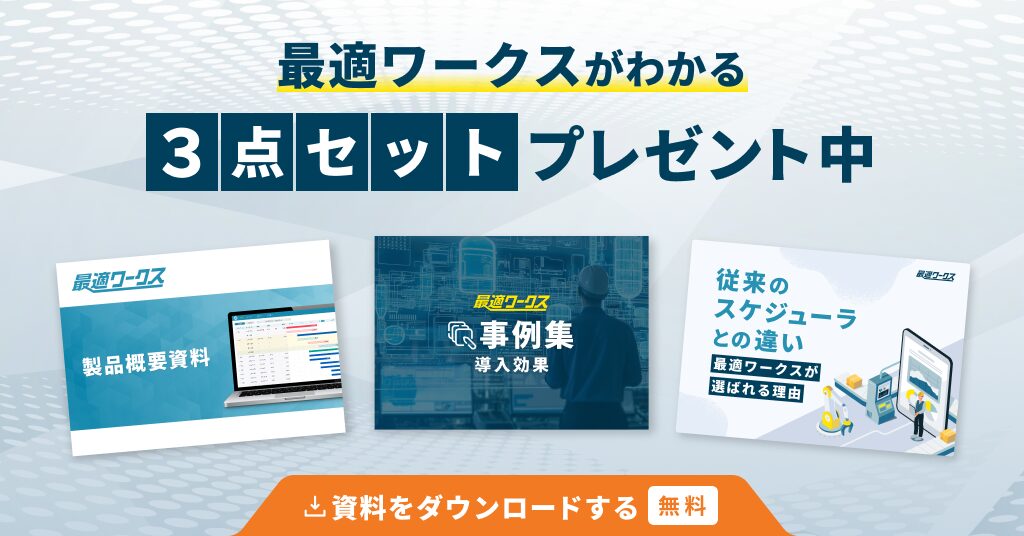