- コラム
属人化の課題ってなんだろう?属人化危機の本質と課題解消について考えてみた
製造業の現場において必須となる生産計画。その作成業務において近年多くの企業で課題となっているのが、「属人化」です。業務が1人もしくは数人の社員のみに属人化している状況はもちろん課題ですが、それによって引き起こされる本質的な問題とは何でしょうか。
本記事では、生産計画作成の属人化の本当の課題とは何か、その解決策とは何かを解説します。ぜひ最後までご覧ください。
属人化は本当に課題なのか
生産計画立案の属人化の現状
突然ですが、自社において以下のような状況に心当たりはありませんか?
- 特定の生産計画担当者が毎日生産計画の立案を行っている
- 生産計画担当者が休暇を取ると、計画自体が機能せず生産性が落ちる
- 製造工程の詳細は計画立案担当者しか把握していない状況だ
このような課題は、すべて生産計画立案業務の属人化が原因です。実際にこのような課題は多くの会社で見られ、近年製造業が直面している課題でもあります。
では、属人化はなぜ課題なのでしょうか。
多く聞かれる理由としては、「計画が実態にはまらないから」「ノウハウが属人化しているから」などがあります。
これらは確かに生産計画立案における課題です。
しかし、本当にそれだけでしょうか?
属人化の本当の課題とは
そもそも生産計画立案の目的は?
属人化の本当の課題を考える前に、そもそも生産計画立案の目的を再確認してみます。
それは、「業務改善・事業成長のため生産の見通しを持つこと」です。
生産計画があると、いつまでにどのくらいの製品が作られるかがわかり、業務の改善や事業成長に活かすことができます。逆に生産計画がなければ、このような改善活動をすることができず、事業の成長が見込めなくなってしまいます。
生産計画が活用されずに起きた問題
例えば、以下のような問題が発生したとします。
(1)取引先から製品Aの納期回答を求められ、先方ニーズ通り回答。
すでに入っている受注を確認し、直近の製造予定にも余裕があると思って受注した
↓
(2)今日納品予定の製品Bが完成していない。
残業してどうにか終わらせたが、製品Aの製造には入れなかった
↓
(3)結果として製品Aの製造も納期ギリギリに残業しつつ対応した……。
急いで作業したこともあり、不良品が一定存在してしまい、残業代の発生も考えると、そんなに粗利が取れなかった。
この問題は、生産計画が活用されていないことで発生したものです。
なぜ、問題が起きたのか?
(1)においては、生産計画立案者でさえ感覚的にしか状況把握ができておらず、「感覚的にいけるだろう」という見込みで営業担当に回答してしまっています。
(2)では、計画上では終わっているはずの製品Bの作業がまだ終わっていなかっただけでなく、その状況を把握できていなかったことで、予定通りに製品Aの製造を始めることができていません。
(3)も同様に、製品Bの遅延の影響を製品Aも受け、納期にギリギリ間に合わせるという事態になってしまいました。
これら(1)(2)(3)の問題は、すべて生産計画が機能していれば回避できた問題です。
生産計画で生産の見通しを持ち、状況把握ができていれば、これらの問題は避けることができ、余裕を持った無理のない生産を行うことができます。
このように、生産計画を立案する目的は、「業務改善・事業成長のため生産の見通しを持つこと」であると言えます。
属人化の本当の課題とは?
実際の製造・営業・経営の各現場ごとに見ていくと、以下のような課題に心当たりはありませんか?
製造現場での課題
まずは製造現場について見ていきます。
予実管理ができておらず、生産計画が着手の順番を決めるためだけに使われ、実際その通りに作業が進んでいるかはわからないという状況は、多くの方に心当たりがあるのではないでしょうか。
それ以外にも、納期遵守のために毎回残業が発生したり、現場の改善活動に着手できていなかったりといった課題も多くの企業で見られます。
営業現場での課題
続いて、営業面でも見ていきましょう。
生産計画が活用できていないと、納期想定がわからず、顧客に自信を持った提案ができなくなってしまいます。
これにより新規受注が止まってしまったり、納期遅延の原因がわからなかったりと、営業現場でも多くの課題が起こってしまいます。
経営目線での課題
最後に、経営目線での課題も見てみましょう。
生産計画は売上を立てるためのコアになるものですが、これが正確でないと、事業計画で想定している製造量が担保できないことがあります。
また、残業が増えることによって人件費がかさみ、適切な原価構成が維持・把握できないという課題や、生産計画が改善活動に利用できないことで、3M(ムリ・ムダ・ムラ)が解消できず、業務改善の見通しが立たないという課題などがよく起こっています。
これらはすべて、生産計画が活用できていないことに起因します。
これらの課題を解決するには、生産計画に対する意識を変えることが重要です。生産計画は、単に立案すればいいというものではありません。それを上手く活用することで、業務改善や事業成長に活かすことができます。
生産計画立案業務が属人化していると、妥当な生産計画を立案することができず、上手く業務改善に活用することができません。
生産計画立案業務の属人化の課題は、生産計画を「作る」上での課題だとされがちです。しかし本当の課題は、生産計画を「使う」上での課題が大きいと言えます。
生産計画は「作る」ではなく「使う」という意識を持ち、適切な生産計画を立案できるようにしていきましょう。
最適ワークスで実現する「使える」生産計画
AI×SaaS 生産計画ツール「最適ワークス」
では、実際に「使える」生産計画を立案するにはどうすればいいのでしょうか。スカイディスクでは、AIで最適な生産計画を立案するサービスとして、「最適ワークス」を提供しています。
最適ワークスは、独自のAIエンジンを活用したSaaS型の生産計画DXツールです。登録したマスターデータをもとに、最適な生産計画を自動で立案します。
最適ワークスで「使える生産計画」を
最適ワークスが提供する価値は、
製造工程の現状の可視化により、「使える」生産計画の作成ができることです。
現場の感覚値でしか認識されていないものが、最適ワークスを使うと、誰にでも見える形で言語化することができます。改善の基盤となる計画を持つことができるようになり、そうして出来上がった生産計画を上手く活用することで、以下のような業務改善や事業成長に着手できます。
- 【見込める改善】
- ボトルネックの改善が図れる
- 残業時間の削減・製造人件費の最適化が図れる
- 見通しが持てるので、トラブル発生時の対応ができる
- 製造に無理がかからず、品質向上・納期遵守に貢献する
まずは現状業務の可視化
実際に、最適ワークスを活用したPDCAサイクルの例を見てみましょう。まずは、最適ワークスで現状業務を正しく把握できた事例をご紹介します。
【事例 現状の把握(Pre-P)】
ある部品メーカーでは、製品Aの製造にかかる時間は、管理会計上で4時間を想定していました。
最適ワークス導入にあたって、製造現場にヒアリングしたところ、実際は前段取りに1時間、製造に3時間、後段取りに1時間の、計5時間かかることがわかりました。そのため、製造にかかる時間はトータル5時間としてマスターデータを設定しました。
しかし、後々に調べてみると、実態は毎回1時間の残業が発生しており、製品Aの製造にはトータル6時間かかっていることがわかりました。
そこで原因を探ると、ヒアリングした内容とは異なり、前段取りに毎回2時間がかかっていたことが判明しました。そのため、業務の改善余地があることは把握しつつ、製品Aの製造にかかる時間は、ひとまず6時間として設定しました。
このように、最適ワークスの導入により、まず現状業務の可視化をすることができます。管理会計上の数値や現場の感覚値が実態と合っているかを検証することで、そのあとの改善活動が可能になります。
計画と実績の差分から改善活動を進める
次に、最適ワークスの生産計画を使って改善活動をどう進めるかについて、別の事例でご紹介します。
【事例 改善活動の進め方(PDCA)】
ある金属加工メーカーでは、計画上では8時間想定の作業に対して、実態は10時間かかっており、残業が発生していました。この課題について、最適ワークスの活用により、現状を正しく把握し、製造工程ごとに振り返ることができます。
この事例では、製造工程ごとに調査したところ、第4工程の業務について遅延しがちであることが、全体の遅れの原因であることがわかりました。これを改善するために、工程内で要求される業務を分解して研修を行ったり、チェックシートを更新してリーダーに共有するなどの改善施策を取ることができました。
最適ワークスの計画を活用することで(P)、計画通りに製造が進まない課題や要因が可視化(D)し、これを振り返ることで、業務を改善していくための活動(C・A)を行うことが可能になった事例です。
このように、最適ワークスで基準となる計画情報を持つことで、より効果的な改善活動を進めることができます。
最適ワークスによる業務改善の事例
実際に最適ワークスを導入したことで、生産計画を活用し業務改善につなげている企業様も多くいらっしゃいます。ここでは、サイダ・UMS様、スザキ工業所様の2社の事例を紹介します。
サイダ・UMS様での事例
サイダ・UMS様は、従業員数約40名の工作機械メーカーです。会社の若返りのため20代を中心に採用を強化していく中で、残業ありきで業務を回していく業務体制を改善する必要がありました。
そこで最適ワークスに出会い、生産計画が立案される⇒実際に活動した成果を把握する⇒予実管理を行うことで製造活動を改善していくという流れをシームレスに行うことを目標に、導入していただきました。
斎田社長は、「一気に大きな成果を得るのではなく、小さな成功体験を積み重ねて徐々に成果を得ていきたい」と、スモールスタートの進め方に共感いただいています。今後も少しずつ運用を進めていき、業務改善に繋げていく考えです。
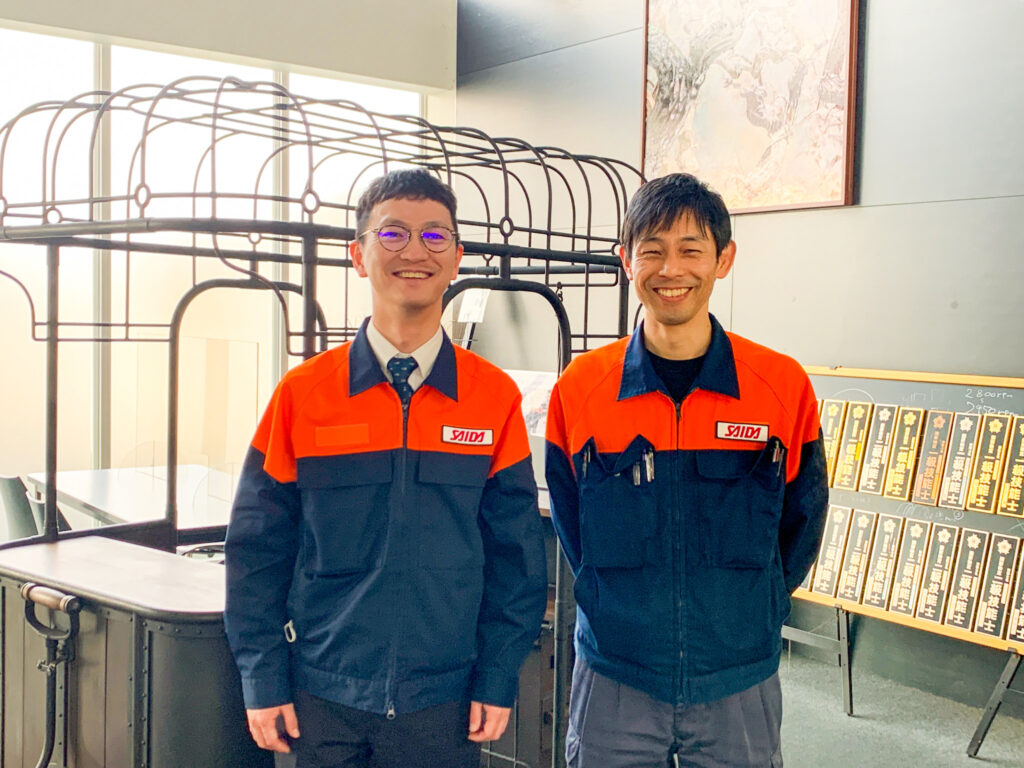
左から、代表取締役社長 斎田さま、 製造部部長 情報システム・企画開発部部長 藤浪さま
事例詳細はこちら。
スザキ工業所様での事例
スザキ工業所様は、従業員数約60名の自動車部品メーカーです。自動車部品以外の製造に踏み出し、事業が多角化していく中で、生産計画も複雑に。それに伴ってトラブルが多発するようになり、その対応のため残業が常態化していました。生産計画担当者も疲弊してしまい、業務改善のために最適ワークスを導入していただきました。
導入の結果、「無理のない計画」が立案できるようになり、残業を削減することができました。段取り替えなどの効率も最適化され、生産量も向上。また、特急対応などのイレギュラー対応が明確になり、生産管理と製造現場の不信感も払拭できました。
計画立案業務自体もシンプルになり、海外技能実習生であっても生産計画立案に携われるように。今後は「誰でも計画が作れる」という状態を目指しています。
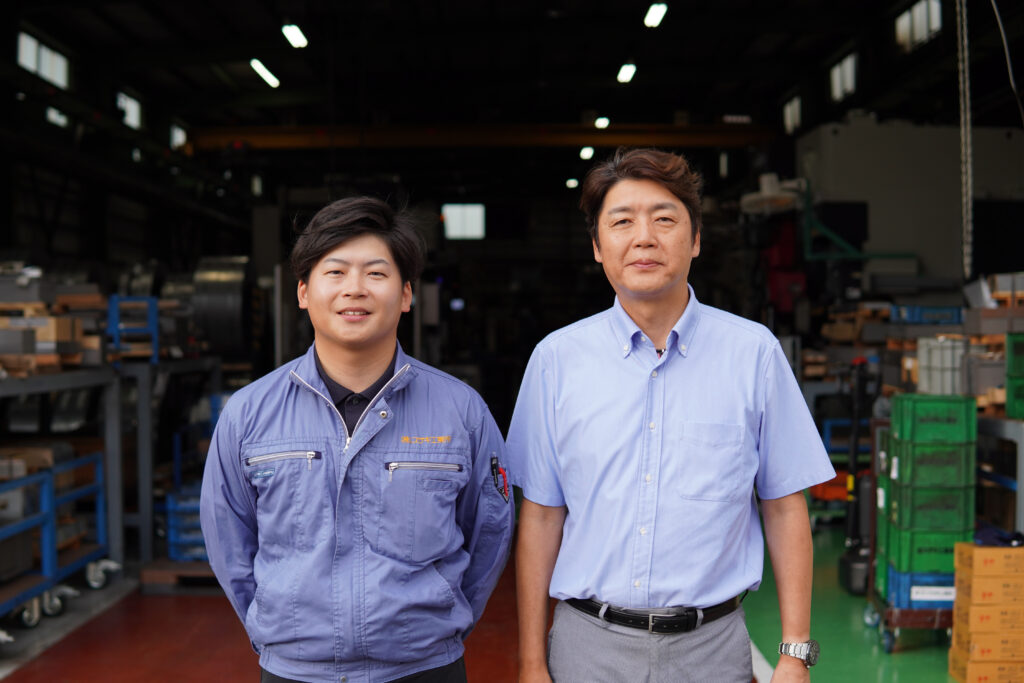
株式会社スザキ工業所
左から、 生産管理課 主査 兼 企画開発室 室長 兼 人事課 課長 鷲﨑 圭一朗さま、 代表取締役 鷲﨑 純一さま
事例詳細はこちら。
改善活動には、まず現状の可視化
事業成長のために、PDCAを回して改善活動をすることは重要です。しかしそのためには、PDCAのPにあたる「現状の可視化」が欠かせません。最適ワークスは、このP=「現状の可視化」を支援するサービスです。「使える」生産計画を作成し、それをもとに改善活動をサポートします。
最適ワークスに興味をお持ちいただけましたか?
AI×SaaSの生産スケジューラ「最適ワークス」は、「使える」生産計画を作成し、改善活動へとつなげることができるプロダクトです。少しでも興味を持っていただけましたら、オンラインデモ会も行っているので、ぜひご相談ください。
現状の課題のヒアリングや「最適ワークスを利用して目指す理想の状態とは何か」という点から、一緒に検討させていただきます。
生産計画サービスの導入なら最適ワークス!導入効果と、導入のしやすさが特徴です
最適ワークスの特徴と導入効果
最適ワークスとはAIを活用した生産計画の可視化・カイゼン支援サービスです。
最適ワークスは、スモールスタートによる導入のしやすさで、高い評価をいただいています。
まずは小さな範囲から導入可能。徐々に計画精度を上げ、リスクを抑えながら段階的な改善を進めることができます。
この過程において、生産計画のDXに経験のある専門スタッフが、失敗しないシステム導入を支援します。
導入事例
・株式会社スザキ工業所様様
適切な生産の見通しにより、残業時間を20%削減。納期遅延30%を解消しました。
・株式会社ミツワケミカル様
海外2工場の生産計画DXを実現。計画ミスによる過剰・過小製造ゼロにしました。
・旭電器工業株式会社様
カン・コツが必要な計画立案から脱却。生産計画業務の負担も月20時間軽減しました。
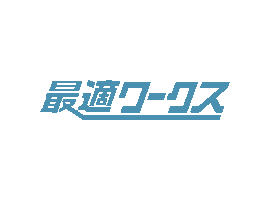
AIが生産計画を自動立案!生産計画・管理のDXを支援する製造業向けSaaS。工場の生産キャパ・製造進捗を可視化。納期回答の精度向上、残業時間を削減など中小・中堅工場での業績改善をサポート。専任エンジニア不要で使える!圧倒的コスパを実現。
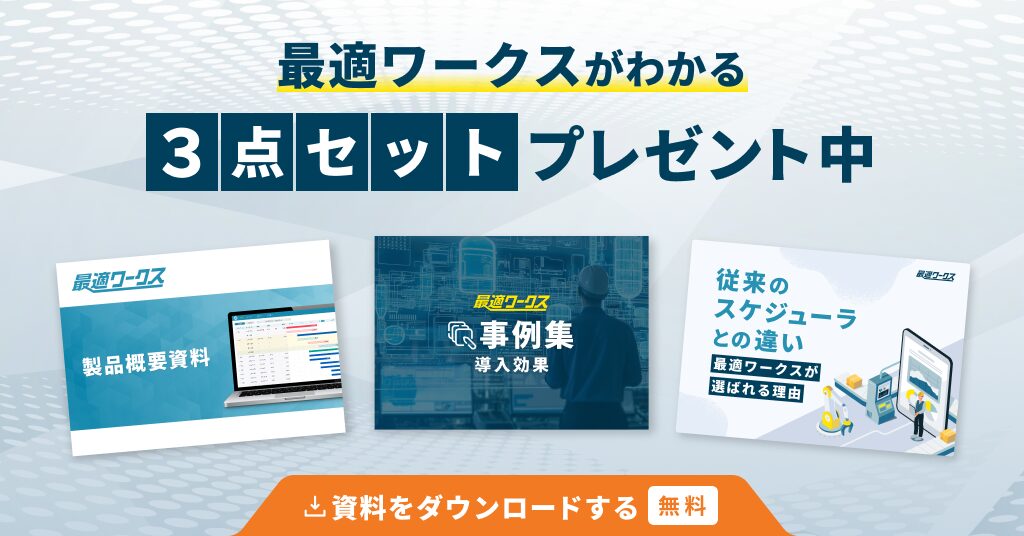