- コラム
失敗事例から学ぶ!生産スケジューラの導入を挫折した企業が再挑戦して大成功できた理由とは?
目次
- なぜ生産スケジューラが必要なのか
- 生産スケジューラ導入で陥りやすい3つの落とし穴
- 代表的な失敗要因
- 生産スケジューラ導入成功の鍵
- 具体的な導入事例
- 生産スケジューラ導入時に直面した障壁
- 障壁1:課題が多すぎて優先度を決められない
- 障壁2:計画立案の考慮点が、担当者以外に共有されていない
- 障壁3:ツールを既存業務に合わせようとする
なぜ生産スケジューラが必要なのか
本日は「生産スケジューラの導入を挫折した企業が再挑戦して大成功できた理由」について、解説させていただきます。
製造業の現場では、生産計画に関して、以下のような課題が頻繁に発生します。
「紙やExcelで生産計画を作成している。計画作成に4時間かかり、定時後に毎日22時過ぎになってしまう」
「時間をかけた計画だが、急ぎの納品変更で作り直しになった」
「自分しか生産計画を作成できないので、休みを取ることができない。責任が大きく、精神的にもつらい」
「そもそも生産計画を作成していないので、予実管理ができず、生産活動でPDCAを回すことができない」
こういった課題に対して、生産スケジューラの導入が検討されるわけですが、弊社の調査によると、352名の製造業従事者のうち、問題なく生産スケジューラを導入・運用できている企業はわずか1%という結果が出ました。まずは、なぜこれほど導入が難しいのか、その要因を探ります。
生産スケジューラ導入で陥りやすい3つの落とし穴
落とし穴1:制約条件が暗黙知になっている
生産スケジューラの導入には、工場ごとに異なる制約条件のカスタマイズが必要です。
しかし、製造条件や優先順位がベテランの担当者の頭の中にしかなく、言語化されていない、したがって、生産スケジューラに設定する際に適切な条件を定義できない、というケースがかなり多いのです。
皆様の中にも、経験や勘で生産計画を作っているという方もいらっしゃるのではないでしょうか。
落とし穴2:導入期間の長期化とコスト増加
2つ目は、その制約条件が複雑なため、導入期間の長期化や導入費用の高騰が発生する点です。例えば、よくある話として、次のようなケースを耳にします。
- 全工場を対象とした大規模プロジェクトになったが、数年が経っても導入ができない
- 導入できたとしても、開発に時間がかかり、数年前の要件で作られたシステムが現場に合わなくなる
- すべての制約条件をシステムに実装しようとして、費用が数千万円に膨らみ頓挫する
生産スケジューラに限らず、基幹システムの開発においても、開発プロジェクトがスタートしてから10年経っても導入できない等の話はあります。
ある企業様では、多額の追加費用を投下して何とか導入までたどり着いたのですが、10年以上前の仕様で作られているため、現場の運用に合わなくなっている部分も多く、導入後も現場の負荷は何も変わらない、むしろ負荷が増えてしまっている……といった事例もありました。
落とし穴3:パッケージ製品の使いこなし問題
3つ目は、パッケージ製品を導入したものの、機能が複雑で使いこなせないケースです。
導入時の初期設定をベンダーに任せると手間は省けますが、その後、制約条件を簡単に変更できず、都度、何かある度に追加開発が必要になります。さらに、カスタマイズを加えると、システムのアップデートが難しくなったり、時間や費用がかさみがちになったりします。
また、標準機能に独自のカスタマイズが加わることで、システムの仕様が複雑になり、理解しにくくなります。その結果、メンテナンスやアップデートが困難になり、最終的には誰も使わない、または限られた人しか使えず、再び属人化が進んでしまうことも少なくありません。
代表的な失敗要因
ここからは、導入プロジェクトにおける代表的な失敗要因について考えていきたいと思います。
失敗要因1:導入が目的化する
「生産スケジューラを導入すればすべての問題が解決する」と考え、具体的な運用計画を立てずに進めると、結果的に「負荷が増えただけ」という状況になりやすいです。
よくある話として、「社長による鶴の一声で生産スケジューラの導入が決まった」「DXが流行っているから、とりあえず導入してみた」といった動機で始めると、導入後に改善効果が不明瞭となります。現場もなぜ導入したのかを理解できず、結果的に「負荷が増えただけ」という状況になってしまいます。
失敗要因2:過剰な期待を持つ
2つ目の失敗要因は、期待過剰な目標設定をしてしまうことです。生産スケジューラの導入によって、すべての課題を一度に解決しようとすると、導入期間が長期化し、完成時には時代遅れの仕様で誰も使わないシステムになったり、数千万円もの開発費用が高騰し、プロジェクトが頓挫することもあります。
改善策としては、無理のない現実的な目標設定から始めることです。最近では、スモールスタートによるDX推進によって成功している企業様が増えています。
失敗要因3:現場の定着不足
「導入して終わり」ではなく、導入後の現場での活用こそが重要です。
システムを導入しただけで満足してしまい、現場での活用や習熟が軽視されると失敗要因になります。導入以上に重要なのは、しっかりと使いこなせるかどうか。現場で操作方法を学び、システムに慣れる期間が必要です。
生産スケジューラ導入成功の鍵
続いて、生産スケジューラの成功の鍵について考えていきます。
成功の鍵1:スモールスタート
初期投資やリスクを最小化しながら、段階的にスケジューラを現場に浸透させていくことができます。成功のポイントとしては、現場の負担を軽減できる点が挙げられます。
はじめから工場全体に導入するのではなく、特定のラインや工程でテスト運用を行うことで、混乱を最小限に抑えることができます。さらに、成功体験を積み重ねることで、小さな成功事例を作り、それを他のラインや工程に広げていくことで、現場のモチベーションも維持できます。
また、スモールスタートによって課題の早期発見と改善が可能になります。実運用を通じて想定外の問題点を把握し、解決策を講じてからスケールアップしていくことができます。
導入されたお客様の声として、「たとえ失敗しても影響が少なく改善点が把握しやすいので、スモールスタートの考え方はとても重要」とおっしゃる方が非常に多いです。
成功の鍵2:現場の運用をシステムに適応させる
導入する生産スケジューラの機能や仕様に、現場の運用を適応させることで、ツールのポテンシャルを最大限に引き出すことができます。成功のポイントとしては、システム標準機能を活用することが挙げられます。
スケジューラの基本機能を活用し、その範囲内で業務フローを見直すことで、導入時のトラブルを回避できます。また、現場の意識改革を行い、従来のやり方にツールを合わせるのではなく、ツールに業務を合わせることで、シンプルかつ効率的な運用を実現します。
さらに、長期的な保守性を向上させることも重要です。カスタマイズを最小限に抑えることで、将来のバージョンアップや運用変更時のコストと手間を削減できます。
導入されたお客様からは「カスタマイズをすると絶対にうまくいかないと思っていたため、カスタマイズなしで運用できる生産スケジューラを選んだ(結果、成功した)」という声を多くいただいています。
成功の鍵3:カスタマーサポートの活用
導入直後の運用安定化や、利用者のスキル向上において、現場に伴走してくれるカスタマーサポートが重要な役割を果たします。成功のポイントとしては、次の点が挙げられます。
- 迅速なトラブル解決
システムエラーや運用上の不明点に対して、専門的なサポートを受けられることで、現場の混乱を防ぎます。 - 現場スタッフの教育
運用トレーニングや、実際の業務に基づいたアドバイスが、現場スタッフのスキル向上を助けます。 - 信頼関係の構築
運用上の課題を共有し、ともに解決を図ることで、長期的なパートナーシップが生まれます。
お客様の声として「現場にしっかり伴走してくれるカスタマーサポートがいたからこそ、導入に成功した」と評価いただくことが多いです。
このように、生産スケジューラの導入を成功させるためには、スモールスタートで始めること、システムに現場を適応させること、そしてカスタマーサポートの手厚い支援を受けることが重要な鍵となります。
具体的な導入事例
ここからは、課題の解決策として、AI搭載の生産スケジューラ「最適ワークス」をご活用いただいた事例をご紹介します。
導入企業の基本情報
- 業種:電子部品製造業
- 従業員規模:500名〜1000名
- 製造方式:組み立て加工
システム導入前の課題
この企業では、最適ワークス導入前に以下のような課題を抱えていました。
- 生産計画立案業務の負担
限られた時間内で複雑な条件を考慮しながら計画を立案する必要があり、精神的にも肉体的にも大きな負担となっていました。 - 品質維持・納期遵守と計画立案体制の安定化
計画立案には現場を熟知した担当者が必要であり、属人化が進んでいました。この状況にリスクを感じ、計画精度を維持しつつ、対応できる人員を増やす必要がありました。 - 過去の生産スケジューラ導入の失敗経験
以前、生産スケジューラの導入を試みたものの、設定の複雑さが原因で頓挫。そのため、新たな導入に対して不安を抱えていました。
最適ワークス導入を決めた理由
- 直感的に分かりやすい操作性
実際に画面を見た際に、従来のスケジューラよりも分かりやすいと感じたことが決め手となりました。 - 導入しやすい価格設定
コスト面でも魅力的で、「効率化・最適化のための投資」として前向きに捉えられました。 - 導入プロセスを学びと考えていた
「運用が安定することが理想だが、導入プロセス自体にも学びがある」と積極的に取り組まれました。
生産スケジューラ導入時に直面した障壁
とはいえ、生産スケジューラの導入は一筋縄ではいきませんでした。ここからは導入プロセスにおいて発生した障壁と、それを乗り越えた方法についてご紹介します。
- 課題が多すぎて優先度を決められない
- 計画立案の考慮点が、担当者以外に共有されていない
- ツールを既存業務に合わせようとする
障壁1:課題が多すぎて優先度を決められない
計画の可視化により、様々な課題が見えるようになりました。その結果、「やりたいことがたくさん出てきて、優先度を決めきれない」という状態に。課題が明確化することは喜ばしい一方で、解決すべき課題が増え、プロジェクトの長期化リスクが発生しました。
「やりたいことが多すぎる」障壁の乗り越え方
この障壁を乗り越えるために重要なことは、導入目的を明確にし、常に振り返ることです。
例えば、「計画精度を維持しつつ、工数削減と属人化解消を実現する」が導入目的であったとき、導入の過程で発生する様々な問題を、この目的と照らし合わせ、優先度を決定していきました。
例えば、次の3つの問題を考えます。
- 時間単位で立案していた計画を、分単位で立案できるようにしたい
- ガントチャートの見え方を、エクセルの計画と揃えたい
- 工程間のリードタイムを設定したい
これらを導入目的と照らし合わせると、1つ目の問題は精度向上を目指したものですが、従来できていなかったことを最初から優先すると、導入が進まずプロジェクトが長期化する恐れがあります。
2つ目の問題は、既存業務の再現が目的となっており、導入の本来の目的を考えると優先度は低くなります。
一方、3つ目の問題は、本来の目的である計画精度の維持に直結するため、最も優先すべき課題といえます。
障壁2:計画立案の考慮点が、担当者以外に共有されていない
導入前、計画立案の際に考慮している事項はデータとして整理されておらず、特定のスタッフの頭の中にしか情報がない状態でした。また、当たり前になりすぎて、何が制約条件なのか自覚できていないことも多くありました。
計画立案の考慮点が暗黙知となっており、情報を整理・共有する必要がありました。
「計画立案時の考慮点が、共有されていない」障壁の乗り越え方
この障壁に対し、重要なのは条件を言語化し、データとして整理することです。対策はいくつかありますが、今回は2つの方法を紹介します。
工程を図示する方法
1つは、「工程ごとの条件や工程間の制約を図示する」方法です。例えば、製造工程を図にすることで、考慮すべき条件を明確にできます。
- 完成品の製造には部品Cと部品Dが必要
- 完成品の着手条件は、部品D完成の2営業日後、かつ、部品C完成の3営業日後
- 部品Dの製造は、部品A・部品Bの完成後に開始 など
このように、ひとつずつ整理していくことで、担当者の頭の中にある条件を言語化・データ化できます。
設定条件によるアウトプットを確認する方法
もう1つの方法は、最適ワークスの出力と実際の計画を比較し、乖離をチェックする方法です。
例えば、最適ワークスにある製品群の製造フローと、それぞれの段取り時間を設定した状態で計画を出力しました。出力されたガントチャートでは、段取り時間の後に、水色の製品の製造が割り当てられ、さらに段取り時間を挟んで再び同じ製品を製造しているとします。
一方、現状の生産計画では、同じ製品を連続製造する場合には、段取り時間は不要というルールが存在しているかもしれません。こうした違いを見つけることで、考慮すべき条件を洗い出せるという方法です。
障壁3:ツールを既存業務に合わせようとする
システム導入の過程では、既存業務に引っ張られ、ツールを自分たちに合わせようとしてしまい、「今までの業務をそのまま再現すること」が目的になってしまうことがありました。
既存業務をそのまま再現することで、本来の目的である業務全体の改善が損なわれる可能性があります。
「ツールを既存業務に合わせようとする」障壁の乗り越え方
この障壁はもっとも陥りやすい問題です。重要なのは既存業務をそのままシステム化するのではなく、見直せるポイントを見つけることです。
例えば、従来の計画では「1日に生産できるのは1,000個まで」という条件で製造していた企業様で、最適ワークスでは1日2,500個の生産計画が立案され、実態とシステムの間に1,500個の乖離が生じた、というようなことがありました。
改めて業務を見直すと、この「1日1,000個」という制約は在庫の置き場所が原因であることが判明しました。つまり、保管スペースを確保すれば、最適ワークスの計画通りに生産できるとわかったのです。
システム導入では、どうしても実態との乖離が発生します。それを完全になくすのは難しいですが、重要なのは柔軟な視点で課題を捉え、システムを変える以外の解決策も考えることです。
システム導入後の成果
この導入企業様が得られた成果は、以下の通りです。
- 生産計画業務の負担軽減 → 月あたり約20時間の工数削減を実現
- 属人化の解消 → エクセルなどの専門スキルがなくても計画立案が可能に
- 品質や製造現場に悪影響を与えずシステム導入完了 → 計画と実績の乖離がなく、高精度な計画立案が可能に
実際にお客様からは「少しずつ形になっていくのが楽しくて仕方なかった」「最適ワークスのファンになった」といった嬉しいお声をいただいています。
最適ワークスの特徴
最後に、スカイディスクが提供しているAI搭載の生産スケジューラ「最適ワークス」について簡単に紹介させてください。最適ワークスは、AIが効率的な生産計画を自動で立案するシステムです。
主な特徴は3つあります。
- 導入期間が短い
最短で2ヶ月で導入できたという実績があります - コストが低い
SaaS提供のため月額利用料金となります。他社の生産スケジューラと比べて安く、スモールスタートしやすい価格帯です - シンプルで使いやすい
視認性が高く、直感的に操作できるため、導入後の現場定着もスムーズに進みます
さらに、専任担当者による手厚いサポートも好評をいただいております。お客様と伴走しながらDX推進を支援します。
まとめ
生産スケジューラの導入は、製造現場の効率化に大きく貢献する一方で、多くの企業が導入時に挫折を経験しています。しかし、成功を収めた企業には、いくつかの共通点がありました。それは、スモールスタートの実施、システムへの業務適応、そして充実したサポートの活用です。特に、導入目的を明確にし、小さな成功体験を積み重ねることで、現場の負担を最小限に抑えつつ定着を促進できた点が大きなポイントでした。また、カスタマイズを最小限にし、システム標準機能を活用することで、長期的な運用のしやすさも確保できました。
生産スケジューラ導入に成功するためには、「導入すること」ではなく、「活用すること」をゴールに据え、適切なステップを踏むことが重要です。本記事を通じて、導入のヒントや成功の鍵をつかんでいただければ幸いです。
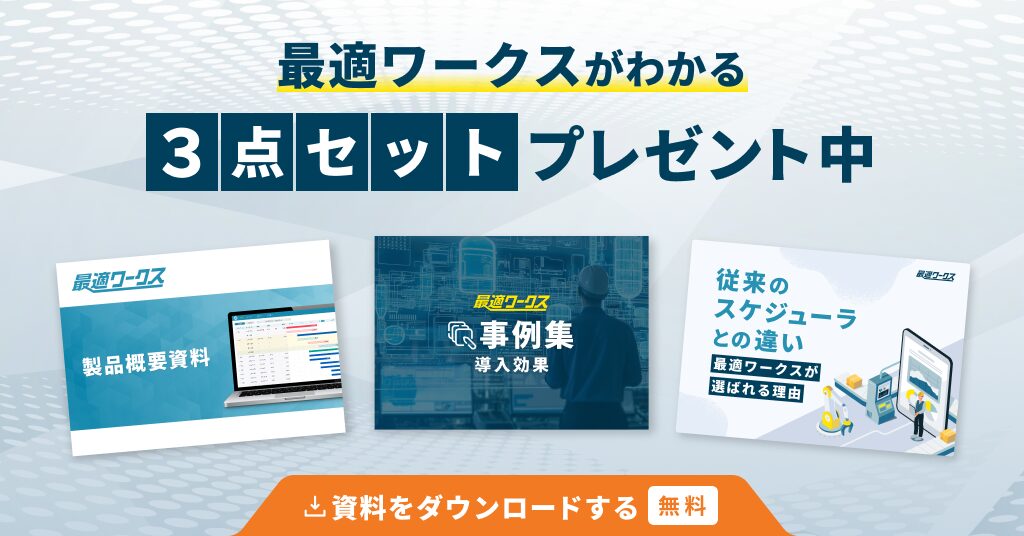