品質を守るための生産計画。複雑な最終工程での計画負荷を軽減
- 旭電器工業株式会社様
- 電子部品
- (会社規模:500名以上1000名未満)
- 組立
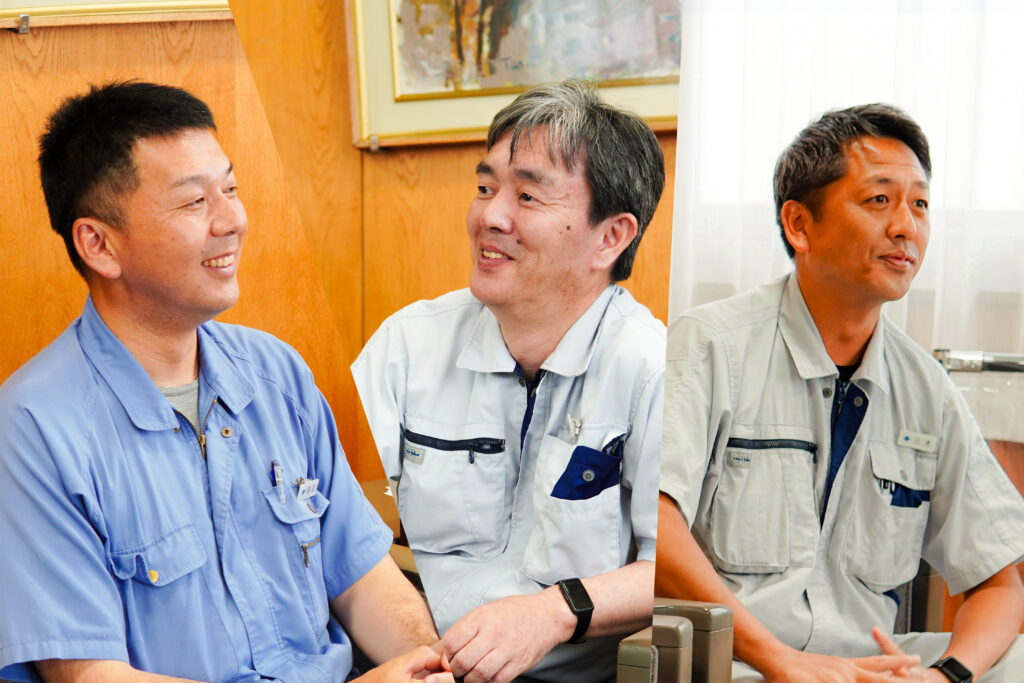
旭電器工業株式会社
左から、 管理部 情報システム課 課長 沼江さま、 取締役 製造部長 濵口さま、 製造部 商品製造課 課長 三木さま
-
課題
- 生産計画作成業務の負担増大
- 品質保持・納期対応に対し、さらに安定した計画立案の体制構築
-
解決策
- 最適ワークスを利用して計画作成
-
効果
- 生産計画業務の負担軽減(月あたり約20時間削減)
- 生産計画業務の属人化解消(エクセル等に専門スキルがなくても計画作成できる体制)
- 品質や製造現場に悪影響を与えることなく、計画精度が保たれた
1949年の創業以来、配線器具、情報通信機器、防災機器、制御機器など多彩な製品を手掛けてきた旭電器工業。パナソニックグループとのパートナーシップのもと、設計開発から製造までを一貫して自社で行い、品質にこだわった商品を生産してきました。
同社はより良い製造体制を目指し、2022年9月より最適ワークスを導入しました。導入に至った経緯、期待する効果について、取締役部長の濵口氏、製造部の三木氏、管理部 情報システム課の沼江氏のお三方にお話を伺いました(以下、敬称略)。
背景と課題
生産計画は「品質」のために重視
濵口:我々はものづくりの会社として『モノの品質』を大切にしています。そのために安定した製造ラインでモノづくり(さらさら流れるラインにすること)が行われなければなりません。その阻害になっていることが製造不良です。製造不良は時間が足りなかったり、焦っているときに発生しがちです。品質にこだわるのであれば、作業者にイレギュラー作業をさせないことが原則であり、そのためには最適な生産計画を立案し、運用することがとても重要になってきます。
もし『部品が足りない』といったイレギュラーが発生すれば、そこで作業が止まってしまう。作業者の焦りやミスを誘発し、品質に影響を及ぼします。生産ラインは必要な数、適切なスピードで動かすことが非常に重要です。計画は早すぎてもダメですし、遅すぎてもよくない。生産計画にこだわる理由は、それが品質に直結するからです。
きっかけは業務負担軽減
三木:最初にテーマが挙がったのは、月に1回開催している『全体最適改善会』です。これは全体を見たときに何がベストか、部署を越えて意見交換する取り組みの場です。
私が担当するEV車の充電ケーブル製造は、工程が長くて諸条件が複雑です。品種も多く、現場のことを熟知しないと計画が立てられません。品質管理のために計画は重要な要素ですが、限られた時間で特定の人が計画作成している状況で。業務負荷を改善したいと考え、常に何か解決する方法を探していました。
そんな中、改善会で沼江から紹介があったのが『最適ワークス』でした。
導入の決め手
「失敗しても知見が得られる」コスト感
沼江:以前、他社のスケジューラ導入を検証したことがありますが、そのときはパラメータ設定が非常に多くて挫折しました。どれくらい時間や手間がかかるか想像できなくて、「やる価値はあるのだろうか」と……。正直スケジューラは導入できないと思っていました。継続的に調査をしていましたが、従来サービスはあまり変わり映えがない印象だったところに、現れたのが「最適ワークス」です。
最適ワークスは、導入までのハードルが下がっていると感じました。直感的なところも大きかったですが(笑)。AI、という言葉がキャッチーでしたし、SaaSならではの導入しやすい価格設定だったことも魅力に感じました。「これなら試せそう」と、改善会で情報を共有しました。
三木:そこで、私が食い気味にやりたい!と(笑)
濵口:会社として「効率化」「最適化」を重点目標と掲げていることもあり、周囲からネガティブな反応はなかったです。
特に、これまで生産スケジューラを実際に導入したことはなかったということもあり、「仮に失敗したとしても知見が得られるのであれば、この投資は高くない」と判断しました。
導入効果
無理のない計画立案。製造現場にもポジティブな影響
三木:月末の稼働日6日前ほどにメーカーから届く内示情報を元に、翌月の計画を立てます。
最適ワークスの導入前は、まず私が最終工程の計画をエクセルで作成し、できた計画を踏まえて、別の計画担当者Aさんが計画を作成し、またそれを踏まえて計画担当者Bさんが作業し……という、まるでリレー形式で計画を作成していました。
完成品を構成するブロックごとに、1日の生産数量を考える必要があり、各ブロックにも部品がたくさん紐づいていて、それぞれのセクションに計画担当がおります。
翌月までの限られた時間で、複雑な条件を考慮しながら計画作成するのは、大きな負担になっていました。それぞれのエクセルが3〜4個存在しており、工程によっては複雑なものもあり、計画立案時のカンやコツが言語化できておらず、属人化している点にも課題感を持っていました。
濵口:三木が担当している商品の工程は、工程が長くて計画業務に複数人が関わっていること、また製品サイズの大きさから在庫を持つことが望ましくないので、スムーズな生産が求められるという背景もありました。弊社で一番、計画が複雑な工程です。
三木:導入後は、進め方がガラッと変わりました。最適ワークスで大体のスケジュール(完成品)を出力し、CSVで出力して、これまでの手作業と置き換えました。その上で、エクセルのフォーマットに落として活用しています。最適ワークスの画面はわかりやすいですが、エクセルの方が現場には馴染みがあります。現場では最適ワークスから出力されたデータを基に、確認・手作業で最終調整して活用をしています。
数字で見ても、月20時間ほどの計画作業を削減できており、時間に追われて取り組んでいた状況から、業務負担を大きく軽減できました。
ツールを使うことで把握できた知見を活用
三木:生産の見通しを精緻に持てるようになることが一番の目的だったので、計画業務の負荷がゼロになる画期的な変化でなくとも、まずは業務の質が上がり、少しでも楽になればと思い、運用を目指しました。
当初、従来の生産計画と最適ワークスのアウトプットには差がありました。人が作った計画と違いはあるものの、今まで人が考えていた計画の無駄さにも気付かされた次第です。そして、計画立案要件が整理されたことで、もっとシンプルに考えていいんじゃないかと思い、製造工程の要件を変えたりなど、チャレンジもしています。
最適ワークスで表現できない製造条件には、ひょっとして無理や無駄があるのではないかと、要件を見直すことで現実との乖離が埋まった部分もありました。現状のやり方を変えることについても、改善会をはじめ部門間の垣根なく相談できて、やりやすい環境で進めることができています。
今後の展望
改善への「ワガママ」な姿勢
三木:自分たちがやりたいことについては、システムがわかる沼江に意見をもらいつつ、積極的にスカイディスクの担当者に要望をあげています。もちろんすべてが叶う訳ではありませんが、カスタマイズではなく、『こういう運用方法ではどうだろう?』と目線を合わせて提案してくれ、一緒に課題に取り組めていると感じます。スモールスタートで始めた最適ワークスの導入ですが、当初13工程で開始したものが今では22工程での運用まで広がっています。
濵口:我々はある意味「ワガママ」だと思います。弊社は、商品設計から製造まで一貫生産を行っていて、改善点があればすぐに変更するような組織になっています。よって、下流工程(部門)の要望“ワガママ”も打ち上げ、議論します。それと同じように最適ワークスの運用に関しても、要望があれば些細なことでも共有するようにしています。
スカイディスクは柔軟に前向きに話を聞いてくれるので、非常に助かっています。最適ワークスをより良い形で活用できるように、今後もスカイディスクと二人三脚で進めていきたいと考えています。
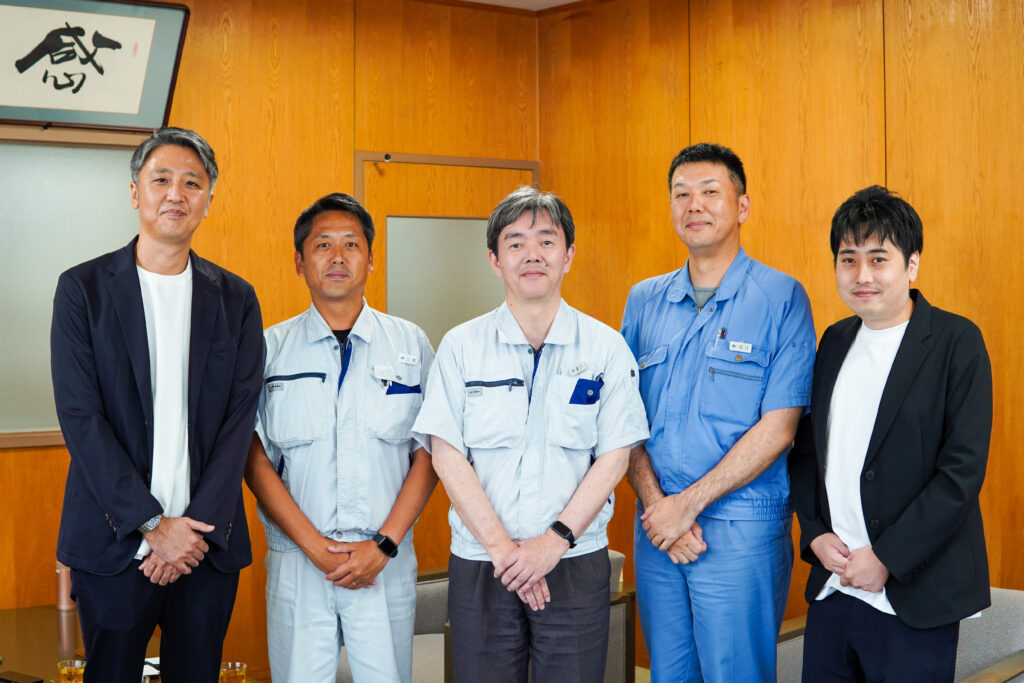
左から、スカイディスク代表 内村、三木さま、濵口さま、沼江さま、担当 河野
ユーザーインタビュー動画、YouTube公開中!
企業情報

旭電器工業株式会社
代表者:代表取締役 橋本幸司/ 設立:1949年7月/ 事業内容: 配線器具、情報通信機器、防災機器、制御機器等の企画・設計開発・製造/ 従業員数: 641名/