かんばん方式で生産指示がくる製造現場において、生産変更にあわせ日次計画を修正したい
- 金属加工製品・金属部品メーカー様
- 金属製品・加工
- (会社規模:500名以上1000名未満)
- 金属加工(切削、プレス、溶接)
-
課題- かんばん方式で生産指示がくる製品について、短納期かつ生産変更が多く、日次計画策定・修正が大変
- 計画ノウハウが属人化しており、生産効率にバラツキがある
-
解決策- 生産スケジューラ導入により、計画を自動立案する
- 計画ノウハウを制約条件として設定し、計画立案を標準化する
-
効果- 毎日の計画立案にかかっていた業務負荷が軽減
- 計画立案の標準化により、生産効率も標準化(属人化リスクの解消)
- 副次効果として見える化が進み、前後工程とのコミュニケーションが楽に
背景と経緯
ある金属部品メーカーの機械加工の工程では、毎日、ホワイトボード上で日次計画を策定しています。
この現場では、生産指示がかんばん方式で届きます。指定枚数になった段階でかんばんが外れてロット生産指示となり、在庫が無くなるタイミングと製品のリードタイムを見比べながら、翌日以降の日次計画に反映しています。
これまでは、品番ごとの所要時間に対応するマグネットを、ホワイトボード上に配置する運用で日次計画を策定していました。業務終了間際の夜21時から翌日分(朝6時から16時間稼働)の計画策定を行なっており、月に数回は緊急オーダーによる当日の計画変更があり、都度、計画修正に対応します。
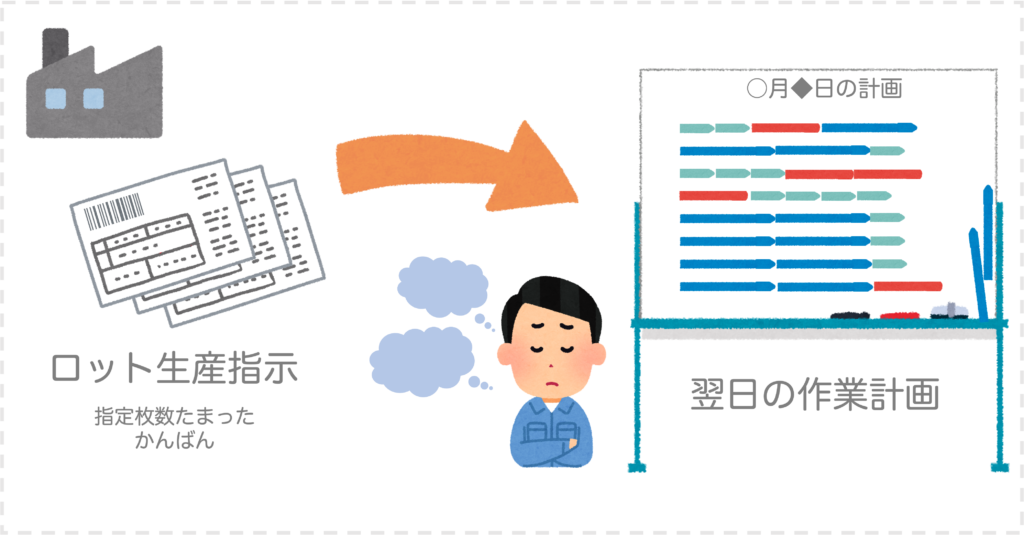
かんばん形式の生産指示をもとに、ホワイトボードで計画立案
工場長は、日次計画について業務負荷の大きさに頭を悩ませていました。また、段取り替え時間を短縮する計画ノウハウが属人化しており、作業者によって生産効率にバラツキがある問題も認識していました。
さらに近年、原料調達や在庫数量の確保について状況が変動する中で、生産順序の入れ替わりが発生するなど、日次計画を人の頭で考える限界を感じました。そこで、計画業務の業務負荷軽減と、作業員による生産効率のバラツキを解消することを目指し、生産スケジューラ導入を検討することになりました。
これまでアナログな運用で計画ノウハウの暗黙知が多いことから、現場主導でのマスターデータ登録ができ、制約条件を柔軟に設定できる最適ワークスの導入を決めました。
段取り替え時間を削減したい
特に、機械加工の工程において、設備稼働率を保持するために、調整しなくてはいけないのが段取り替えの時間とタイミングです。
この現場では、前後の製品の組み合わせが段取り替え時間に影響するため、生産順序も考慮する必要があります。また、段取り替え作業が重複してしまうと、作業員の対応待ちが発生してしまうため、段取り替えのタイミングが重ならないようにします。これまでは、段取り替え時間を削減するために、1日あたりの段取り替えの回数に上限を設けていました。
製品ごとに対応できる生産ラインに制限がある上で、これらの諸条件を考慮して、数十ある生産ラインに対して日次計画策定が求められます。
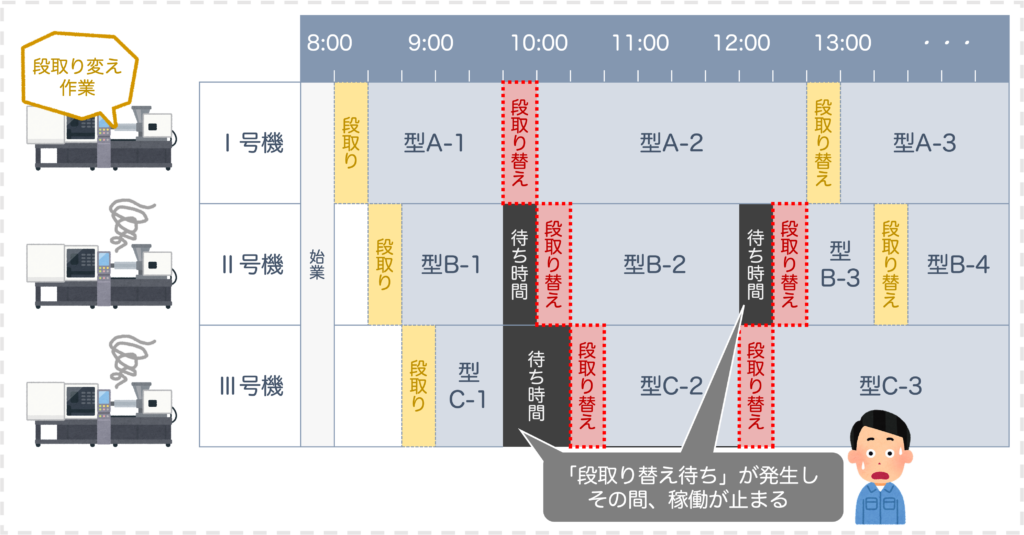
段取り替えの待ち時間により、設備稼働がストップする
かんばんの情報をマスターデータに設定
生産スケジューラ導入にあたっては、品番ごとの所要時間など、かんばんに記載されている情報をマスターデータとして設定する必要があります。また、前後の組み合わせによる段取り時間の違いは、制約条件として入力します。
これまでの計画ノウハウには暗黙知も多く、後任への引き継ぎは難しい状況でした。しかし、最適ワークスでは、まずは最低限の条件設定によりアウトプット(生産計画)を確認し、制約条件を付け外しながら、立案された生産計画について高速にPDCAサイクルを回す、という形で導入を進めます。アウトプットを確認しながら制約条件を検討できるので、結果として、暗黙知の言語化を補助します。
導入後の運用では、かんばんが外れロット生産指示となったタイミングで、ロット単位をオーダーとして最適ワークスに入力。すると、日次計画が自動立案されます。
また副次効果として、これまで日次生産計画は現場のホワイトボードで確認するしか方法がありませんでした。クラウド上に見える化されたことで、前後工程の現場とのコミュニケーションが楽になりました。
一方で、これまでホワイトボードでの運用を続けていた弊害として、一部製品では、所要時間について計画と実績にずれが発生していることが指摘されています。まずは効率の良い生産順序を自動立案するのに最適ワークスを利用していますが、今後は計画と実績の乖離を減らしていく方針です。
まずは実績の可視化に着手。最適ワークスでは、自社で簡単にマスターデータを修正することができるので、実績をもとにマスターデータを更新していくことで、より生産効率のいい計画立案を目指す方針です。
結果まとめ
- 生産計画の自動立案により、毎日の計画立案にかかっていた業務負荷が軽減。
- 作業員ごとの生産効率が標準化
- 副次効果として、ホワイトボード運用を脱したことで、前後工程とのコミュニケーションが楽になりました。また、実績データを集積後にはデータ活用できる基盤ができました。