自動車部品の組立工場で、安定した製造のため生産計画の属人化を脱却したい
- 自動車部品・電子機器メーカー様
- 電子部品
- (会社規模:500名以上1000名未満)
- 組立
-
課題- 生産計画作成の属人化が経営上のリスクになっている
- 計画担当者の業務負担が大きい
-
解決策- 専門スキルを必要とせず、誰でも操作可能な生産スケジューラを導入する
-
効果- 生産計画作成の属人化解消が実現
- 丸1日手間がかかっていた生産計画作成が、必要情報の入力とAIによる自動立案(数分程度)で可能に。担当者は負荷の大きい業務から解放された
- 生産計画のアウトプットを基に、生産効率アップを検討できるようになった
背景と経緯
とある電子部品メーカーでは、製品の生産計画を作成する業務が、計画担当者に属人化していました。生産計画とは、「受注した製品を納期までに製造・出荷する」ために、工場をどのように運営するかの計画であり、納期の遵守や工場の生産性向上など、会社全体にとって大きな意味を持つものです。
そのため、工場の担当部長や課長から、計画業務を一人で行っている現状では、「担当者が休職や退職した場合、安定的に製品を製造できなくなる恐れがある」という懸念が上がりました。
これを受け、この会社では属人化解消を深刻な経営リスクにつながる課題として取り上げ、生産スケジューラの導入を検討することに。シンプルで見やすい画面や直感的な操作性などの、一般的なシステムと比較した利用へのハードルの低さが導入の目的にマッチしていたため、最適ワークスの導入を決定しました。
自動車部品特有の複雑な製造工程にも対応
今回、生産スケジューラを導入したのは、主に車載機器の生産・組立工程です。
一般的に、自動車やその車載機器は非常に多くの部品から構成され、その性質から完成品を組み立てるまでに多くの枝分かれした生産ラインが設定されます。そのため、工程の計画作成時に考慮すべき制約条件が多岐にわたり、他業種よりも生産計画作成が難しいという特徴があります。
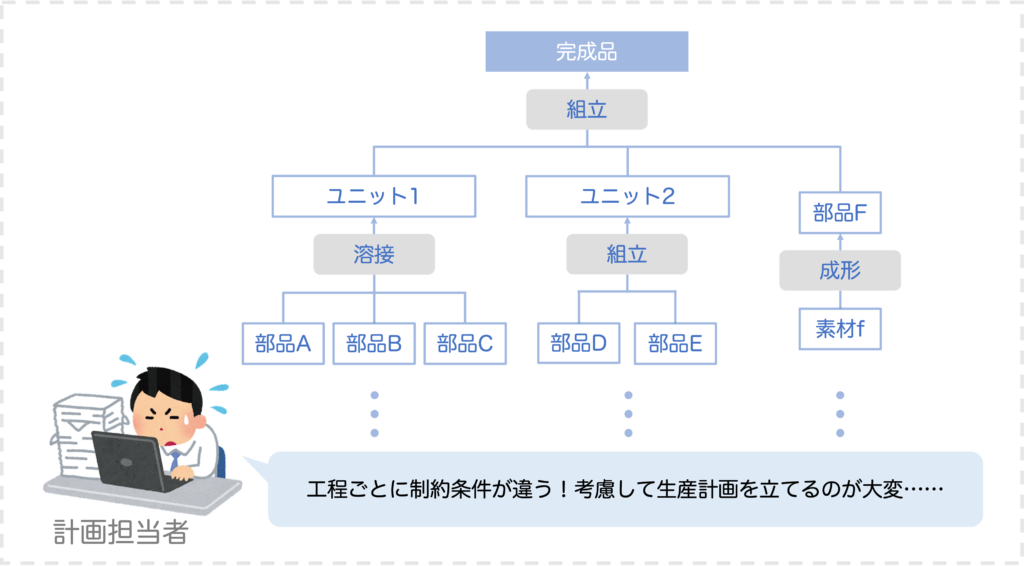
自動車部品組立は、生産ラインが多岐にわたる
加えて、制約条件をあらかじめ設定する必要がある生産スケジューラでは、制約条件の多さが導入のハードルになります。そこで、今回の事例では、優先順位の高い工程や機能から着手し、現場で確認しながら地道にPDCAを回して徐々にスケジューラを完成させる「スモールスタート」(※1)での導入を採用することにしました。
※1 スモールスタートとは、最初は限定的に着手し、徐々に範囲を拡大していく方法です。スモールスタートによる導入の特徴は、細かく確認と修正を繰り返すため、従来のシステム開発型に比べ手戻りが起こりにくいことです。この導入方法により、最適ワークスでは、最短3~6ヶ月程で現場にあった運用に至ることが可能です。
スモールスタートにより、わずか3ヶ月で仮運用へ
「スモールスタート」の進め方にスカイディスクと認識を合わせられたことで、その後の導入にもスムーズに移行することができました。まずは優先順位を検討。その後、制約条件を設定する段階では、具体的なアウトプットと綿密なコミュニケーションにより、短いスパンで改善を繰り返すことができました。その甲斐あって、約3ヶ月という短期間で、現場の制約条件を吸収した生産スケジューラのアウトプットを確認でき、実運用に一定の目処を立てることができました。
想定以上の波及効果も
従来は計画担当者が丸1営業日かけて、月次生産計画を作成していましたが、最適ワークスの導入によりオーダー情報などの必要事項を入力後、数分程度でAIが自動立案できることを確認しました。加えて、制約条件の設定も順調に進捗。仮運用の結果として、最適ワークスの導入により、属人化の解消と業務負担の軽減という、2つの導入目的を達成することが見込めました。また、当初から期待していた操作性についても満足のいくものでした。
さらなる波及効果もあります。これまでは計画作成で手一杯だったところ、今後は生産計画が自動立案されます。アウトプットをベースとして、そこから計画の手直しや制約条件の改善など、より生産性の高い計画を作成可能になるのではと期待されています。
実際に、担当者からは「これまでは生産計画の作成という難度の高い業務に1から追われて大変だったが、最適ワークスの導入後は、大部分が自動で行われるようになり、以前よりも業務の負担は楽になる。設定した制約条件の改善や、出力された計画の手直しなどを行うことになるが、『良い計画を作る』業務に向き合えるようになる。」といった声も聞かれました。
今後は、生産計画の精度を更に向上させていくことに加えて、最適ワークスで出した計画から設備ごとの稼働率等を算出し、そうした情報を工場全体の運営に役立ていくことも想定しています。
結果まとめ
- 丸一日かかっていた生産計画作成が、必要情報の入力とAIによる自動立案(数分程度)で可能に。計画担当者の業務負荷を軽減し、作業自体に忙殺されることなく、より生産性の高い生産計画を検討できるようになりました。
- 生産スケジューラの導入により、現場の暗黙知を制約条件として設定。工場の安定稼働には経営リスクだった、生産計画作成の属人化を解消しました。
- スモールスタートにより、多くの制約条件が存在する組立工程でも、効果的な生産スケジューラの導入が実現しました。
- 設備の稼働率など、今後の工場運営において取り組むデータ活用の基盤ができました。