投入順序を最適化して、段取り替えのタイミング重複を回避したい
- 自動車部品メーカー様
- 金属製品・加工
- (会社規模:100名以上500名未満)
- 金属加工
-
課題- 設備の生産品目を変更する際に行う、「段取り替え」のタイミングが設備間で重複するケースがある(設備に非稼働時間が発生)
- 現場の作業者がそれぞれの裁量で投入順序を決めており、作業が属人化している
-
解決策- 生産スケジューラを導入し、段取り替えによる待ち時間を最小化するような生産計画を立案する
- 生産計画を関係者に情報共有する
-
効果- 設備の非稼働時間が最小化され、ラインの生産性が向上
- 関係者がライン全体の生産計画を把握可能になり、アウトプットを基に議論できるようになった
背景と経緯
自動車部品メーカーのある生産ラインでは、設備の段取り替えのタイミングが重複することにより、設備が稼働できない時間が発生していました。
この工場では、作業員は1名につき3-4台の機械を担当しています。機械による工程は自動化されており、作業員の主な業務は生産品目を変更する際に行う、段取り替え(※)と呼ばれる作業です。
これまでは、ラインごとに割り振られた生産量を基に、作業員それぞれの裁量で生産作業が進められてきました。しかし、作業員が頭で投入順序を組み立てるには限界があり、特に、機械の段取り替えのタイミングが重複することが問題となっていました。
段取り替えが重複することの問題は、大きく2点あります。1点目は、連鎖的な計画遅れが発生する点です。1名の作業員が作業を行うため、段取り替えが重複すると、機械には「段取り替え待ち」の時間が生じます。結果として、連鎖的に計画遅れが発生し、納期遅れや生産完了時期の不透明化など、様々な問題の原因となっていました。
2点目は、設備に非稼働時間が生じる点です。設備をフル稼働できていない状況は、工場全体の生産効率向上を目指す上で、優先度の高い課題と認識されていました。
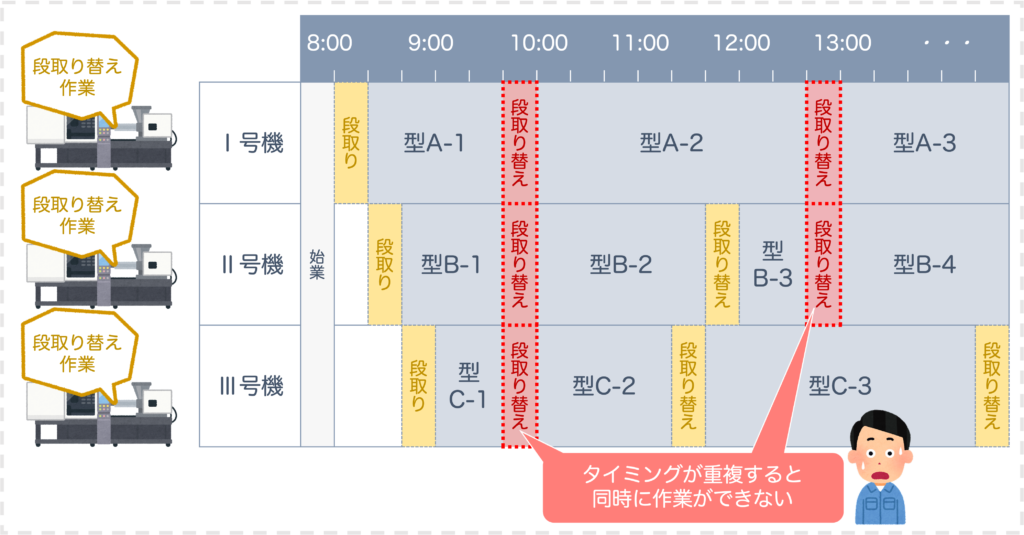
段取り替えのタイミングが重複した生産計画(Before)
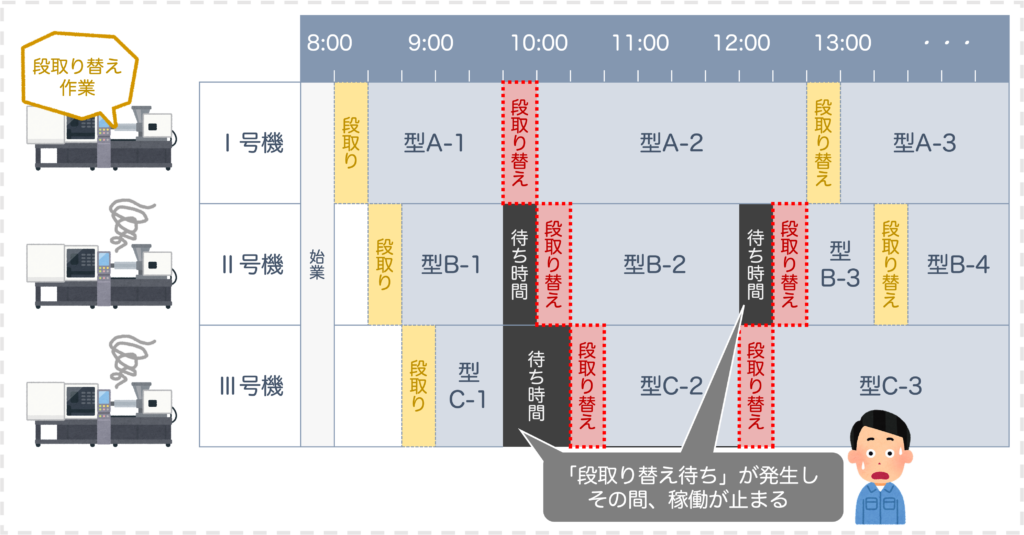
実際には「段取り替え待ち」により、設備の非稼働時間が発生(Before)
そこで、生産スケジューラを導入し、段取り替えのタイミングを考慮した生産計画を自動立案することにしました。制約条件の設定からアウトプットの確認までが早く、仮説ベースで制約条件を追加・修正できる点が決め手となり、最適ワークスを導入しました。
※ 段取り替えとは、生産開始に至るまでの準備を指します。生産する製品ごとに必要な設備・金型・材料などが異なるので、それぞれにあわせたものにラインや設備を取り替える作業です。
仮運用で制約条件を設定・検証
生産スケジューラによる自動立案には、工場の製造条件(制約条件)の設定が必要です。今回のケースでは、制約条件は作業員の頭の中に蓄積されています。暗黙知化した制約条件すべてを、システムに入力できる論理的な形式にすることは難しく、生産スケジューラ導入における大きな障壁となる作業です。
そこでまず、工場の中でも特定のラインに限定し、最適ワークスを仮運用しました。現場での運用の中で、高速にPDCAサイクルを回すことで、最適ワークスに制約条件を設定・修正していくことがねらいです。これにより、工場への影響を最小限に留めながら、現場での運用に即した制約条件を最適ワークスに設定することが可能となります。
現場特有の製造条件に対応した生産計画で、生産性アップ
約3ヶ月の現場での仮運用を経て、現場の制約条件を反映した生産スケジューラにより、投入順序を最適化した生産計画を立案。立案された生産計画で、「段取り替え待ち」時間の最小化について、効果を確認できました。これにより、計画遅れの発生件数は減少し、設備の非稼働時間も大幅に短縮できました。
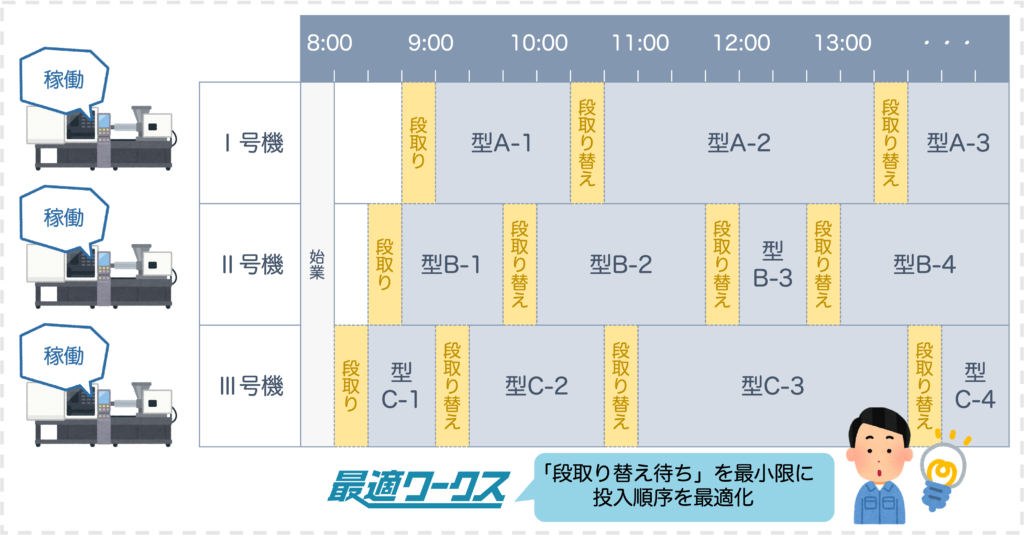
段取り替えのタイミングをずらし、非稼働時間を最小化(After)
加えて、仮運用では新たな意義も見出されました。関係者に生産計画が共有され、工場運営のベースとなる情報が集約されたことで、実際の数値や計画を基にした議論が活発化。
議論の中で生まれた仮説をシミュレーション的に検証する用途でも、最適ワークスが活用される機会が増えました。
これら導入効果が仮運用で確認されたことで、実運用への移行が決定。引き続き、生産計画を通じた現場の生産性向上を目指します。
結果まとめ
- 生産スケジューラによる投入順序の最適化により、段取り替えのタイミング重複を最小限にできた。
- 「計画遅れの頻発」「設備の非稼働時間」など、段取り替えの重複により発生していた問題が解消。
- 生産計画が関係者全員に共有され、アウトプットを把握できるように。工場運営を改善する議論に活用できるようになった。
- 本格導入前に、仮運用であっても生産スケジューラの導入効果が確認できた。スモールスタートにより、導入効果を実感した上で実運用に移行できた。