導入から3ヶ月での運用開始をスピード実現。現状把握から生産効率向上へのステップと、生産計画DXによる製造業務改革
- 大研化学製造販売株式会社様
- 化学
- (会社規模:50名以上100名未満)
- 電子材料
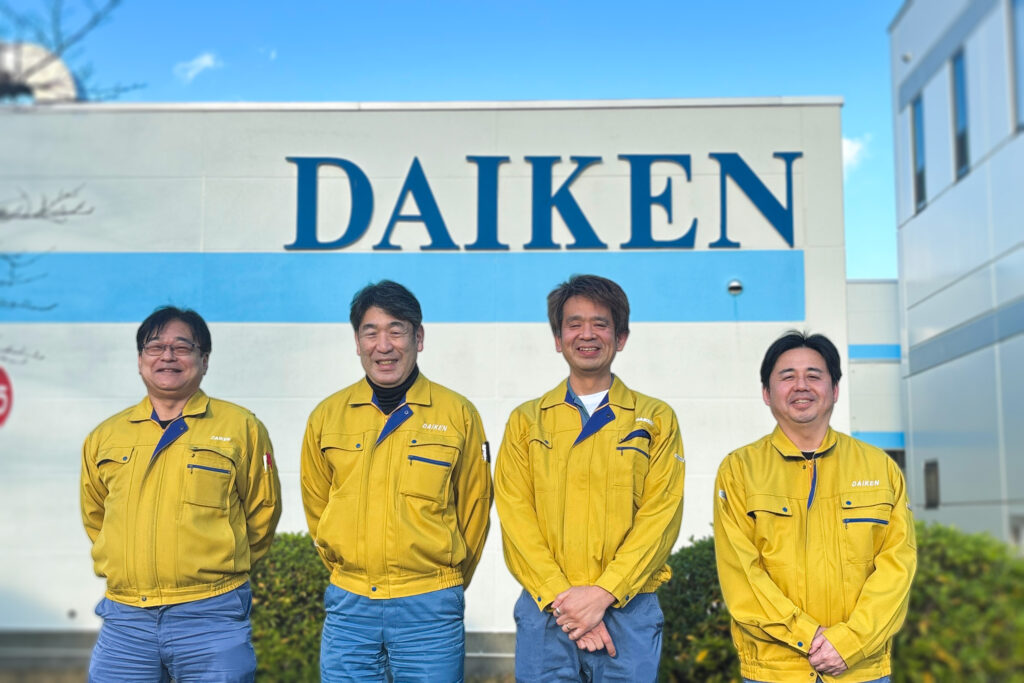
大研化学製造販売株式会社
左から、副工場長 清水さま、工場長 宮川さま、製造1課 課長 志田さま、製造2課 課長 前田さま
-
課題
- 業務属人化とブラックボックス化により、製造活動の現状把握が難しい
- エクセルとホワイトボードでは計画と作業指示が曖昧で、生産工程全体の進捗管理がしきれない
- 投入順序を決めるだけの計画作成に手間がかかり、計画修正も負担が大きい
- 進捗管理と納期遅延について、作業者に過剰な責任がかかっていた
-
解決策
- 生産計画のシステム化により、製造業務の整理と可視化を目指す
- AIを活用した生産計画立案により、計画業務の負担軽減と効率化を図る
- 計画共有と進捗報告をチャットツールで仕組み化し、作業指示と責任範囲を明確化
-
効果
- 計画作成と修正にかかる工数が大幅短縮され、AIによる効率的な計画立案で生産性が向上
- 報連相の円滑化により、管理者と作業者の責任範囲が適正化
- 製造活動の計画と進捗を管理できるようになり、納期管理の精度向上
- 生産工程全体の現状把握と、データを基にした改善活動ができる基盤が構築
大研化学製造販売株式会社(以下、「大研化学製造販売」)は、金属粉末や導電ペーストなどの電子部品用電極材料を主力製品とする電子材料の総合メーカーです。陶磁器の加飾技術を応用し、導電塗料へと転換した歴史を持ちます。
同社の福井工場では、業務の見える化を目的として、積極的にDXツールを活用。2024年4月には「最適ワークス」を導入し、同年7月には一部ラインから本運用を開始。生産計画業務の負担軽減、データ活用による生産性向上、そして業務の見える化を実現しました。現在は先行導入した製造1課にて効果を実感し、製造2課へと利用範囲を拡大中です。
導入の背景、生産計画DXによる具体的な変化、中小製造業におけるDXについて、代表取締役社長 原田氏らに話を伺いました(以下、敬称略)。
導入前の課題
属人化とブラックボックスからの脱却
原田:これまで現状の把握ができないまま、改善に手を付けられず、非効率な業務が多くありました。全社として、各部署の業務を“現状把握できる”ようにDXを進めてきました。
特に製造に関しては、属人化が昇進や職務分掌の問題に直結し、社内人材の流動性を損なう要因となっていました。業務がブラックボックス化しており、属人化しているから上司は部下に業務を引き継ぐことができず、部下も次のステップに進めないという状況です。
生産計画DXで期待した業務の見える化
原田:製造活動の『現状把握』については、計画や進捗管理にエクセルとホワイトボードを駆使して管理しているものの、従来の運用には限界を感じていました。新しく製造1課、2課の課長に就任した二人の現状把握のためにも、様々なツールを試したり、改善策を模索していた中で「最適ワークス」に出会い、導入を決めました。
製造工程と適応範囲
宮川:生産計画の対象は、福井工場で製造している製品です。まず製造1課を対象に運用を開始し、現在は製造2課にも範囲を拡大しています。
製造工程は大きく二つに分かれており、まず製造1課が担当する工程で、原料を製造します。次に、製造2課が担当する工程にて、原料と副材料などを混ぜて加工して仕上げます。その後、熟成・検査・梱包工程を経て最終製品となります。
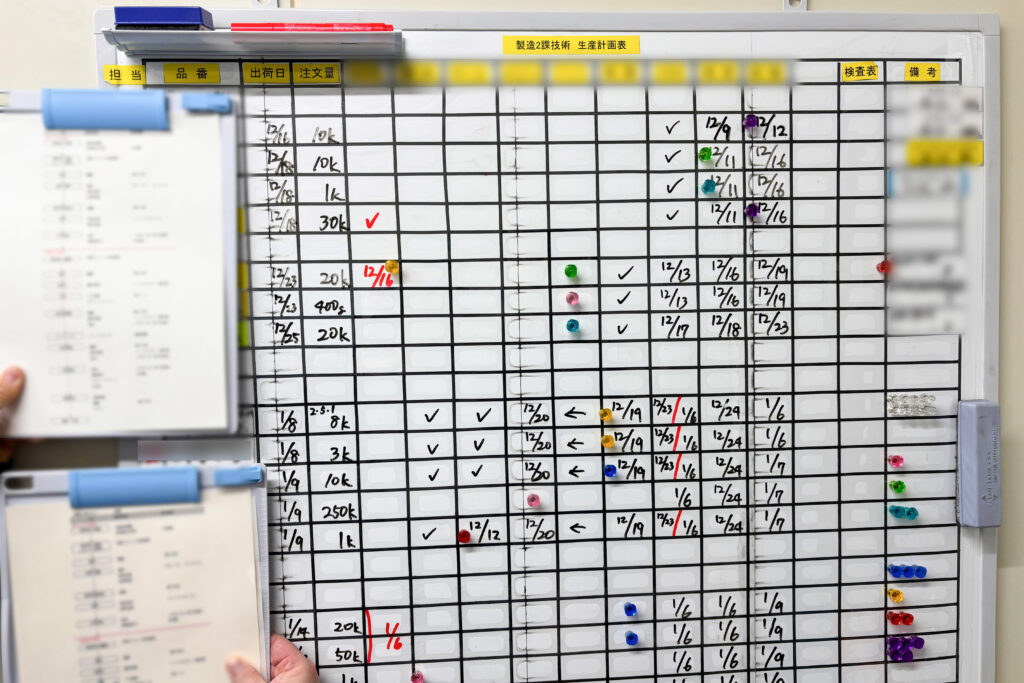
現場では工夫を凝らし、ホワイトボードを活用して計画と製造進捗を管理
導入後の効果
生産計画業務の負荷が大幅軽減
志田:従来は、エクセルで計画を立てていましたが、膨大な行数や細かすぎるシートを駆使する必要があり、1ヶ月分の計画作成に1日以上を費やしていました。さらに、受注情報に変更があると計画修正もすごく大変です。もう目が追いつかないような状態で……。製品の投入順序を決めるだけで精一杯で、その先の工程まで管理する余裕がありませんでした。
最適ワークス導入後は、投入順序だけでなく中間工程の順序や所要時間も把握できるようになりました。まず見た目で生産計画を把握しやすくなり、計画の見直しや修正も、驚くほど簡単になりました。
データで気づいた「生産能力2倍」の可能性
原田:計画業務自体の効率化ができたので、現在は、データに基づいて効率的な製造活動を検証し始めたところです。設備の稼働率を切り口に、改善のヒントを探っています。
印象的だったのは、従来2日かかっていた工程が、AIが立てた計画では1日で完了する計画になったことです。深掘りしたところ、ある作業が慣習的に「1日1回」となっていただけで、実際は1日2回可能なことが判明しました。これにより、生産効率が2倍に向上する可能性が見えてきました。これまでは「1日1回」に疑問を持つこともなく、改善したくてもエビデンスがありません。データで現状把握することで、問題点が明確になった出来事です。
責任範囲が明確化し、報連相がスムーズに
宮川:製造進捗の管理については、現在はチャットツールを活用して、志田課長が1週間分の計画を作業員ごとに共有し、日々の進捗やトラブルは報告をもらっています。これにより、計画と作業実績のギャップもすぐに把握可能になりました。報告内容が明確になり、無理なく続けられています。
志田:トラブルが発生した場合には、『途中でこういう問題がありました』といった報告が届きます。計画通りであれば、完了報告に『Good』スタンプを押すのみ。対面や電話での確認の手間が減り、製造の状況把握もラクになりました。
原田:上司が計画を示すことで、作業者は計画通りに進めれば良し、ということです。以前は計画がほぼなかったので、作業員に納期遅延のプレッシャーがありましたが、おかげで作業者本来の責任範囲に戻すことができました。
一番大きな変化は、ほうれんそう(報告・連絡・相談)が改善されたことです。業務がブラックボックス化して、作業者個人が責任を抱え込んでしまう状況だったのが、報告を通じて状況を共有することで、問題解決に向けてチームで動けるようになりました。
システム選定理由は「導入しやすさ」
柔軟性と直感的な操作性が魅力
原田:最適ワークスの導入前には、他の生産管理システムも2〜3社ほど検討しましたが、どれも自社の仕様に合いませんでした。システムが作り込まれすぎていて、柔軟に工夫する余地がなかったのです。
そんな中で最適ワークスを見つけたときは、画期的に感じました。仕様に柔軟性がありつつ、操作画面が見やすく直感的でとっつきやすい。専門性の高い業務システムは経験者向けになりがちですが、我々のような初心者でも扱いやすいところが大きな魅力でした。
決め手は「手軽なコスト感」
原田:正直、一番の決め手は費用の手軽さです。どんなツールでも、実際に試してみないと自社に合うかどうかはわかりません。最適ワークスには柔軟性のある仕様に期待していましたが、確信を持てるわけではなかったので、まずは試してみようという気持ちでスタートしました。数千万円もする大規模システムはリスクが高く、導入に時間がかかる上、運用に合わないケースもよく耳にします。その点、最適ワークスは「これはできそうだ」と感じつつも、仮に失敗しても許容できる範囲のコスト感だったのが大きな魅力でした。
導入支援のプロジェクト管理に助けられた
宮川:不慣れなITツールに加えて「業務フローをどう整理し、製造工程をシステムにどう設定するか?」など、初めてのシステム導入に、当初は頭を抱える場面も多かったです。けれど、エラーを解決しながら操作にも馴染み、いつの間にか使いこなせるようになりました。
原田:カスタマーサクセスの支援が心強く、すごく助かりました。中小企業では、導入プロジェクトに専任を置くのが難しく、導入作業を進めながら全体を管理するのは非常に負担が大きい実情があります。「新しいシステムを導入するのは社長がやらなきゃいけない」みたいな状況になってしまうんですよね。
その点、最適ワークスのコンサル的な支援と、プロジェクト管理の手厚いサポートは非常にありがたく、単なるツールというよりも、コンサルティングサービスだと感じています。このサポートがあったおかげで、ツール導入が前進し、運用まで漕ぎつけることができました。
ゼロから着手したDXの歩み
現状把握から、改善アクションができる状態へ
原田:そもそもDXの取り組みは、まず事務作業の現状把握から始めました。倉庫整理をしたところ、ほぼ未使用の設備や薬品を多数発見したことがきっかけです。まずは発注業務の透明性を高めるため、業務アプリ開発の「kintone」を導入し、資材部が一元管理する体制を構築しました。結果、無駄な発注をなくし、売上に対する原材料費を大幅に削減できました。
同時期には受発注管理のデジタル化も進め、売上データの集計や分析から、採算の取れない製品の見直しや値上げ交渉が可能になりました。受発注管理は「kintone」で行っており、「kintone」からオーダーを出して、最適ワークスで生産計画を立案する際に使用する形でデータを連携しています。これにより、受注情報の精度向上など、営業側の現状把握に大きく貢献しています。
品質管理も検査表のフォーマット統一から、検査情報を基にした自動アラーム通知まで、ITツール活用によって改善アクションにつながるような仕組み構築を進めています。
共通してやっていることは、現状把握できるように分散していたデータを集約し、仕組みとして解決するということです。今後は、CSVデータを介した業務の情報連携と、最終的にはRPAを活用して効率的なデータの繋ぎ込みを目指しています。
ITツールの現場浸透と人事評価
原田:私が社長に就任した際、工場内を観察すると、皆が「忙しい」「頑張っている」と動き回っていました。しかし客観的な基準がなく、評価が難しい状況でした。自己申告には限界があり、社員から「頑張っている」という声ばかりが届くと、私自身もメンタル的に追い詰められる部分がありました。
そこで、現状をしっかり把握し、定量的な評価を主体にしていきたい。それにより、作業者による業務量の負担の偏りもなくしたい、と考えました。
—— 現場でIT化への抵抗はありませんでしたか?
原田:抵抗する方も当然いましたね(笑)。そうした方には、ITに強い社員をサポート役としてつけ、業務を補助してもらう形にしました。また、報告をITツールで行い、報告が評価に繋がる仕組みにしたところ、自然と浸透していきました。
中小企業の業務改善は、教科書より実践ツール
原田:中小企業の業務改善では、実践的で使いやすいITツールの導入が重要だと考えています。まずはアナログな方法でも、生産管理・生産計画の基本ができてからシステム化すべきという意見もありましたが、教科書通りの進め方では、現実的にやることが多すぎて、作業量が増えるだけでつまずいてしまうんですよね。
リソースが小さい中小企業では、段階的な準備をする余裕がないので、実践的なITツールを導入してなるべく早く使いこなしていく方が、業務改善を進めるのに適していると実感しています。
今後の展望
原田:日々、様々な課題に取り組む必要がある状況の中、中小企業も多くの課題を抱えています。まずは、現状に対応できるよう適切なITツールを活用していきたいと考えています。一定のコストはかかりますが、業務効率化や競争力向上につながると信じています。特に、ITツールの活用によって工数削減できる点は非常に大きいですね。
世界的な競争をするにあたり、こうしたITツールやDXを駆使して、追いつき、追い越すことを目指していきたいです。日本のものづくりを継続するために、IoTやDXの力を最大限に活用し、挑戦を続けていきたいと考えています。
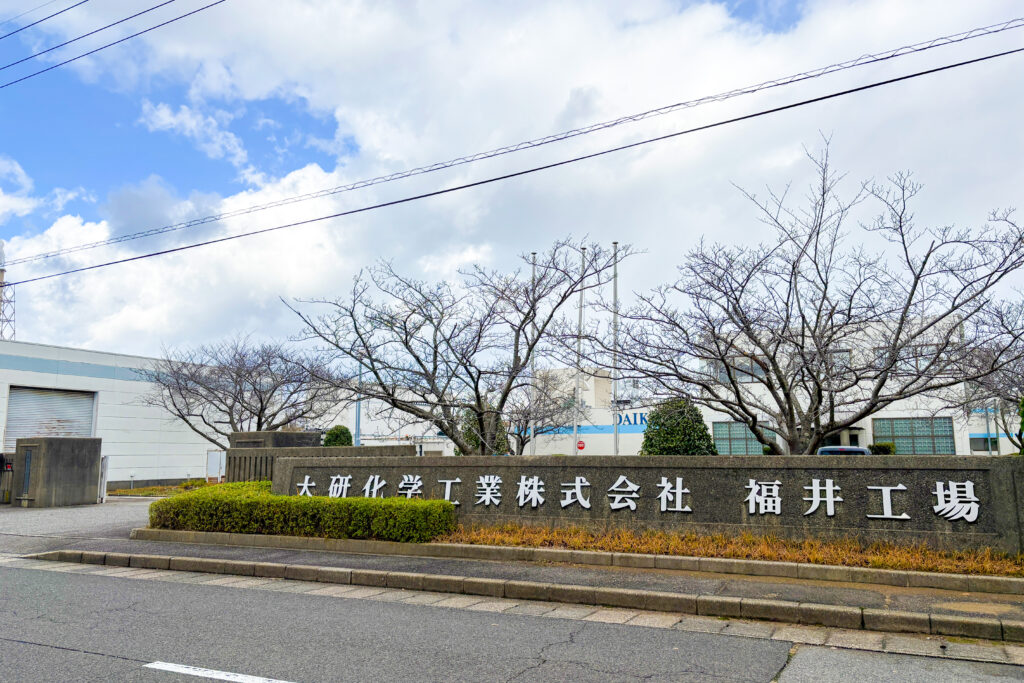
大研化学製造販売株式会社 福井工場
企業情報
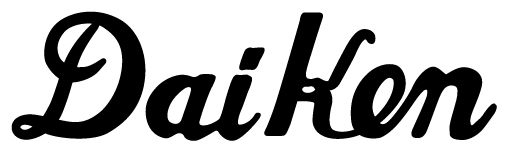
大研化学製造販売株式会社
代表者:代表取締役社長 原田 将弘/ 設立:2011年1月/ 主な事業内容:電子材料事業(金属粉末各種/導電ペースト各種)※大研化学工業株式会社の100%出資子会社として設立、主力の電子材料事業を分割