多角化による成長を加速させるために。かんばん方式だけでは管理できない製造現場を支える生産計画DXとは。
- 株式会社スザキ工業所様
- 金属製品・加工
- (会社規模:50名以上100名未満)
- 金属加工(プレス、溶接)
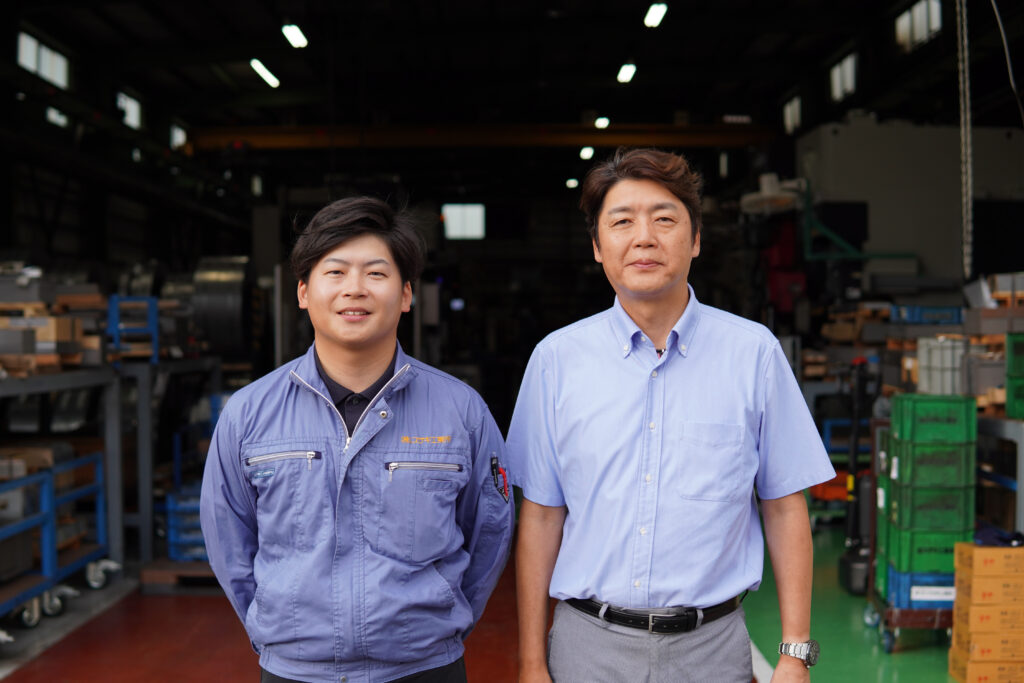
株式会社スザキ工業所
左から、 生産管理課 主査 兼 企画開発室 室長 兼 人事課 課長 鷲﨑 圭一朗さま、 代表取締役 鷲﨑 純一さま
-
課題
- 取引先の拡大により製造品目が多様化。生産計画が複雑化し、かんばん方式での一元管理が不可能に
- トラブルが頻発することで残業が常態化
- 特定の計画担当者に計画業務の負荷がかかっていた
-
解決策
- 最適ワークス導入を機に、マスターデータを整理して製造業務を可視化
- マスター登録をすることで、誰でも生産計画を立案できるように
-
効果
- 「無理のない計画」を立てられるようになり、残業やトラブル軽減
- 製造現場の改善活動に着手する基盤を構築できた
- 計画立案業務の効率化。海外技能実習生でも計画立案ができる状態に
スザキ工業所は岐阜県の自動車部品メーカーとして、金属プレス、溶接、組立加工に40年以上の実績を持っています。近年では多角化を進め、自動車業界以外にも事業を展開。現在60名ほどの従業員が勤務しており、そのうち海外技能実習生と正社員雇用の外国籍の方を合わせると全体の4割に達しています。
取引先の拡大により、製造品目が多様化。その結果、現場管理が複雑になりかんばん方式での限界を感じ、2023年3月より最適ワークスを導入し生産管理体制を強化しました。
導入に至った経緯、導入後の効果について、代表取締役 純一氏、生産管理課 圭一朗氏にお話を伺いました(以下、敬称略)。
背景
純一:弊社は元々、トヨタ系列の自動車部品がメインでした。プレスや溶接を行い、組み立て製造するというものです。当時は1社が100%でしたが、それではリスクが高いので、あるときから取引先の幅を広げる努力を始めました。現在では自動車部品は75%、残りの25%は農機具、建築機材、土木関連、福祉機器などです。
元々は、自動車部品のみのときは、いわゆる「かんばん式」で管理していました。いまはそれ以外の仕事、異なる種類の発注が混在していて、他の25%ほどの仕事を無理やりかんばん方式のやり方に統合しようと試みたりもしましたが難しい、という状況でした。
導入前の課題
きっかけは計画担当者の長期休業
圭一朗:きっかけは計画担当者が2ヶ月程、怪我で休んだことです。その間、代わりに課長が計画業務を行っていたのですが、ある日、帰宅前に現場を確認すると、課長が1時間前からやっていた計画作業にまだ取り組んでいて……。
事情を訊くと「計画を立てるのが大変なんです」と。優先順位や組み合わせを考えるのがすごく大変で、自動車部品と農機具の発注が混在して、さらに複雑になっている、と。
社長に状況を伝えて、人の力で今後やり続けるのは無理、これはどうにかしなくては、という話から「お前がDXの担当だ」と任命され、生産計画のDXから取り組むこととなりました。
多角化により複雑に、かんばん方式での限界
圭一朗:自動車業界の注文は、ある程度は平準化されていて、毎月毎日のオーダーが一定です。とはいえ、自動車業界でもバラつきのある会社もありますし、他の業界では平準化の考え方自体が薄いため、発注量や頻度に差異が出てきます。発注量や頻度が不定期で、急な注文や連続発注に対応する場面も多くなります。
純一:生産量を必要な分だけ最小限にしようとすると、一日の製造活動の中で製品の切り替えは必然的に多くなります。また、弊社は他社よりもさらに多品種少量生産なので、それに伴う段取り回数が多くなり、計画も複雑になりがちです。
かんばん方式で管理していても、まとめて製造して製品数を保持し、そこから出荷している会社も多いでしょう。うちは在庫の保管スペースが限られており、その方法ができないことや、会社の在庫をできるだけ持たない方針であることも、計画を複雑にしている要因でした。
純一:そのため、今までは担当者によって「生産指示が上手い・下手」がありました。計画がいまいちだったり、これくらいは製造できるだろう、という人の想いが乗った計画になっていると、実際は対応することが難しく残業が増えたり、無理に仕事を終わらせようとすることで事故が発生したりと、トラブルの種になることも多く発生していました。
導入後の効果
生産の見通しが立つこと、予実比較をもとにした改善
圭一朗:現在は「最適ワークス」を導入して、顧客のオーダーに対する生産予測の精度が格段に上がりました。
これまで紙で計画を立てていた時に、生産計画を評価する基準を持っていたわけではありません。なので、紙の計画と違う点もあるかもしれませんが、紙の計画上の生産点数と、最適ワークスの生産点数がだいたい同じになった事で良しとして、最適ワークスの運用を始めました。
いざ実際の生産実績と見比べると、最適ワークスでの計画の方が実態に近いことも多々あります。例えば、本当は2時間かかる作業でも、紙の計画では実は少し無理して、短く完了する計画に調整したりしていて。
今は、より現実的に即した計画となったことで、顧客ごとのオーダーに対して、予測が立てやすくなりました。生産の見通しが立つことで、有休も計画的に取得できる環境になりました。製造にゆとりが持てることでトラブルも減り、生産効率も改善しました。
圭一朗:また、紙の計画ではできていなかった、予実比較による改善活動にも着手できるようになりました。
生産計画のもう一つの目的は「弱点を見つける」ことだと思います。例えば、これまでの計画では段取り時間と生産時間は区別できていませんでした。これが最適ワークスにより可視化されました。段取りと生産の改善方法は違います。
本格的な改善活動はこれからですが、予実を確認したときに何が遅れたか分かることで、効果的な対策が打てるようになります。また、生産全般の遅れが発生したときに、それが特急オーダーなど差し込み業務の影響なのかが分かるようになった事も良かったです。
純一:以前は、計画を評価する明確な基準はなかったです。ただ、一般論として生産計画を立てて、一日仕事が進んで、それ通りに進むのであればそれで良し、と考えています。生産量も担保できて、残業時間も収まっているわけですから。
凄い生産計画を立てたとしてもそれで儲かるわけではないので、誰でも労力をかけずに普通の計画ができれば良いのです。今はマスター登録さえできていれば、海外技能実習生であっても、誰がやっても30分で終わる状態なので、そういう意味でも満足しています。
導入時のポイント
まず想定時間ベースでマスターを設定
圭一朗:導入も比較的スムースに進んだのかと思います。導入の際には、通常の業務と区分せず、オーダーが入るたびにマスター登録を進めるスタイルを取りました。最適ワークスでのマスター登録は凄く簡単なので、時間はかかりましたが、特に問題なく進められました。400点程のひと通りの製品についてマスター登録するのに3ヶ月程かかりました。
タイミング良く導入時期に様々なオーダーが入って、登録できる点数も多かったんですが、入力時には、まず数値を入力し、後で精査することを前提に、「だいたいパンチ数が○○回だから○時間」くらいの精度で登録し、段取り時間も基準値で○分、と決めで入力しています。製品マスターについても、今後一つ一つの製品について実際の作業と突き合わせて、計画の精度を上げていきたいなと思っています。
事業成長と業務標準化
標準化は、人材確保と活用を進めた結果
純一:彼(圭一朗)が家業を継ぐと宣言してくれて以来、事業を成長させる方向に舵を切り新規取引先の開拓に取り組んできました。弊社では、生産力を補うため、人材確保をする中で、外国籍や障がい者の雇用にも意識的に取り組んでいます。現在の従業員60名のうち4割は外国籍の方です。過去10年ほど、こういう人材環境において仕事をはかどらせるための工夫を続けてきました。
純一:業務を改善していく為には、データ化して誰でもできる状態にしないと、改善活動は進みません。業務指示を細かくして、分かりやすくする工夫として、指定には数字、アルファベット、色を利用したり、製品や機械を略称で呼ぶ習慣は廃止しています。
この前提があるので、評価は等級分けして行っています。「個々人のレベルを明確にし、そのレベルに応じて業務を任せたい」という考えです。すべての業務を標準化し、単純な仕事から高い技術力を要する仕事まで明確にしました。作業の難易度に応じて仕事をアサインしています。
標準化できて「仕事ができる」という評価
純一:過去に工場では「個人の技能があればいい」といった認識もありました。でも、私の考えは「その仕事を誰でも出来るようにすることが重要」というものです。固有の技術者を何人も育てるというのは、もう現実的ではない状況で、目指すのは誰もが80点の成果を上げられる状態です。残りの20点は特定の人が補えれば良いのです。
だから、我々の業務標準化はDXのためというより、さまざまな背景を持つメンバーに対応するためでした。「DXをやりたい」と意識したことはありませんが、結果的にDXとして成果を上げることにつながりました。
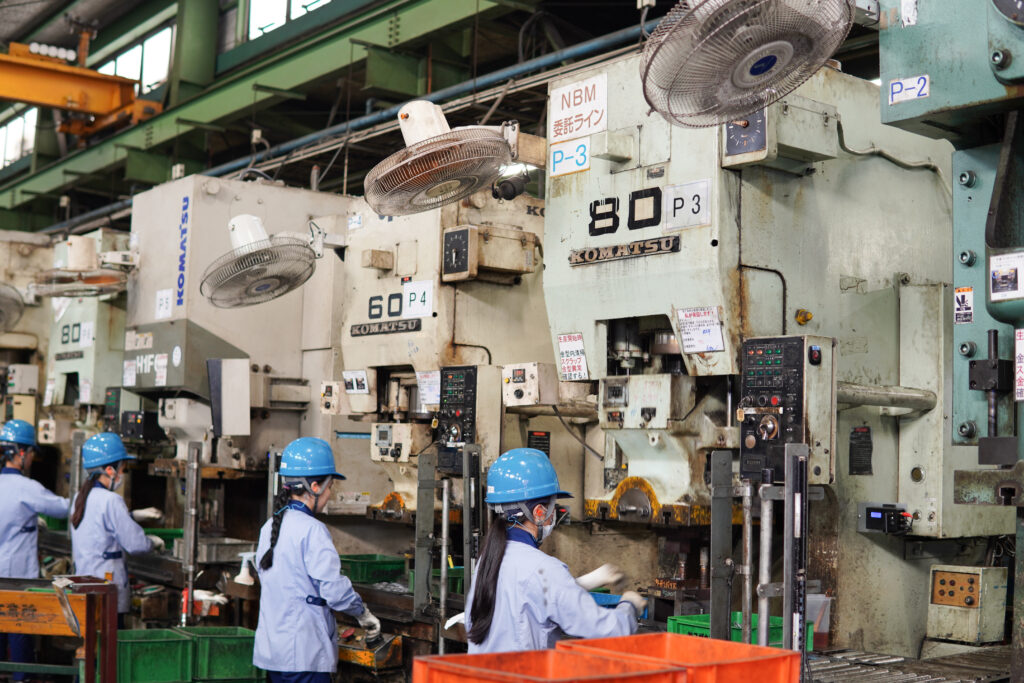
数字やアルファベット「P3」「P4」等を使用して、設備を指定する
今後の展望
圭一朗:最適ワークスは、工場のプレス工程にのみ導入しています。まずは残りの溶接工程にも、適応範囲を広げていきたいです。生産指示の仕組みが違うので、多少調整する必要がありますが、適用できそうという手応えはあるので問題なく進められると思っています。
純一:将来的には、生産計画と生産実績を紐付けて、資材発注の適正化を進めていきたいです。うちは材料の使用比率は60%以上、その発注量・使用量・在庫量の適正化が重要です。また「心配だから多めに製造しておいた」など、製品の隠れ在庫があることもあるので、資材発注や入荷実績、生産実績とともに、材料や製品の在庫状況を確認できるようにデジタル化していきます。在庫の上限ラインを設定し、誰もが目に見える形で管理できる体制にするのが目標です。
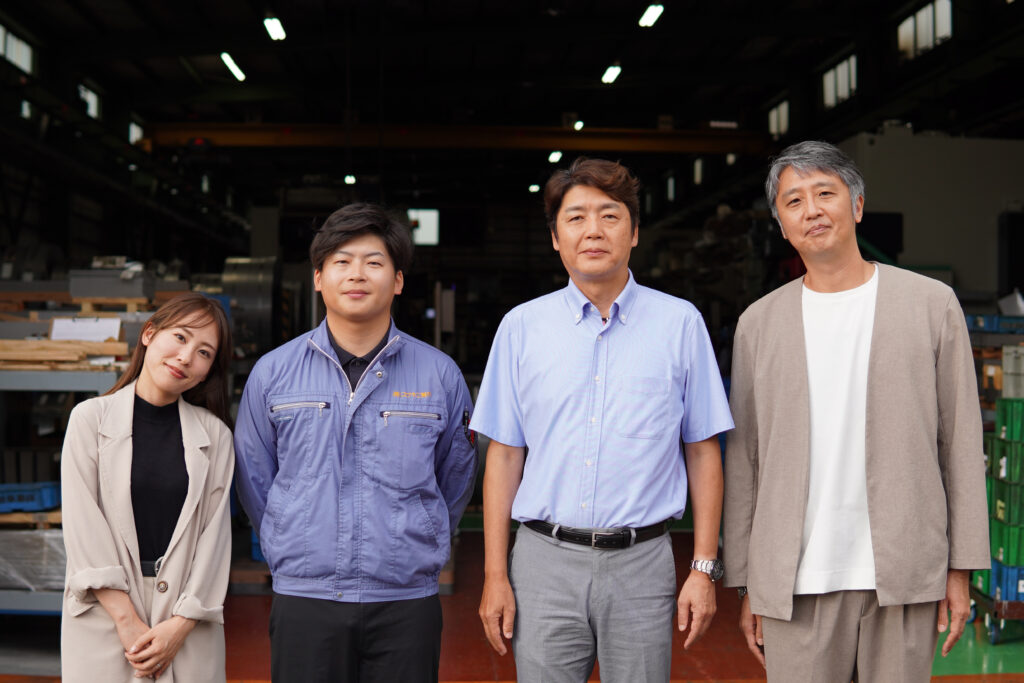
左から、担当 志村、スザキ工業所 圭一朗さま、純一さま、スカイディスク代表 内村
企業情報
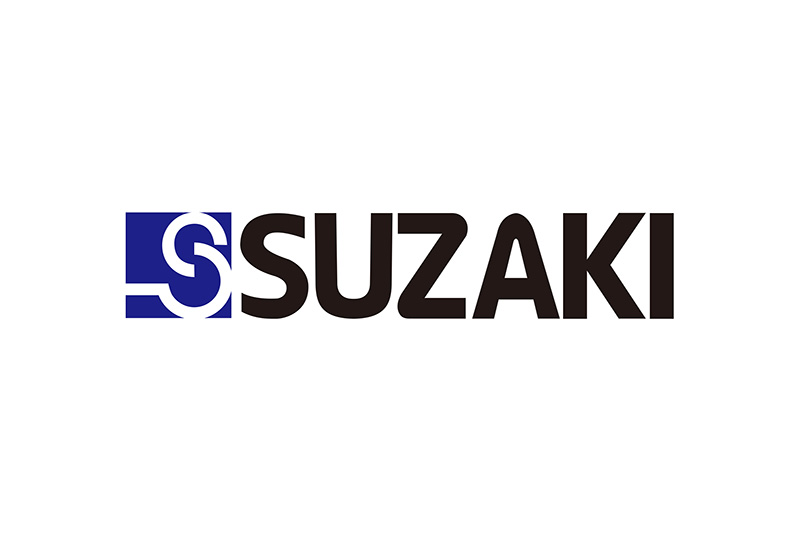
株式会社スザキ工業所
代表者:代表取締役 鷲崎 純一/ 設立:1979年1月/ 従業員数: 61名/ 事業内容:金属プレス、溶接、組立加工全般/ 金型 治具、設備、制御装置の設計製作/ プレス関連機器製造販売